The Fundamentals and Advantages of Sand Casting
Sand casting is one of the oldest and most widely used metal casting processes. It involves creating a mold from sand to shape molten metal into desired components. The versatility, cost-effectiveness, and ability to produce complex geometries make sand casting a favored technique across numerous industries, including automotive, aerospace, and art.
The Sand Casting Process
The sand casting process begins with the preparation of the mold. A pattern, which is a replica of the final product, is created, often from materials like wood, metal, or plastic. This pattern is then used to create a mold cavity in a mixture of sand and a bonding agent, typically clay or resin. Once the pattern is embedded in the sand, the mixture is compacted around it to form a negatively shaped mold.
After the mold is prepared, it is carefully removed from the pattern, leaving behind a cavity that matches the pattern's shape. The two halves of the mold are then reassembled and secured. Next, molten metal—usually an alloy suitable for the intended application—is poured into the mold through a sprue (a channel that allows metal to flow in). The metal fills the cavity and solidifies upon cooling.
Once the metal has cooled and solidified, the mold is broken away to reveal the finished casting. The casting may require further finishing processes such as machining to meet the precise specifications and tolerances required for its application.
Advantages of Sand Casting
1. Cost-Effective One of the most significant advantages of sand casting is its economical nature. The materials used, primarily sand and a binder, are relatively inexpensive. The process also supports low production costs, making it ideal for both small-scale and large-scale manufacturing.
2. Versatility Sand casting can accommodate a wide range of metals and alloys, including aluminum, cast iron, steel, and bronze. This versatility allows manufacturers to produce various components that meet diverse application requirements.
sand casting company
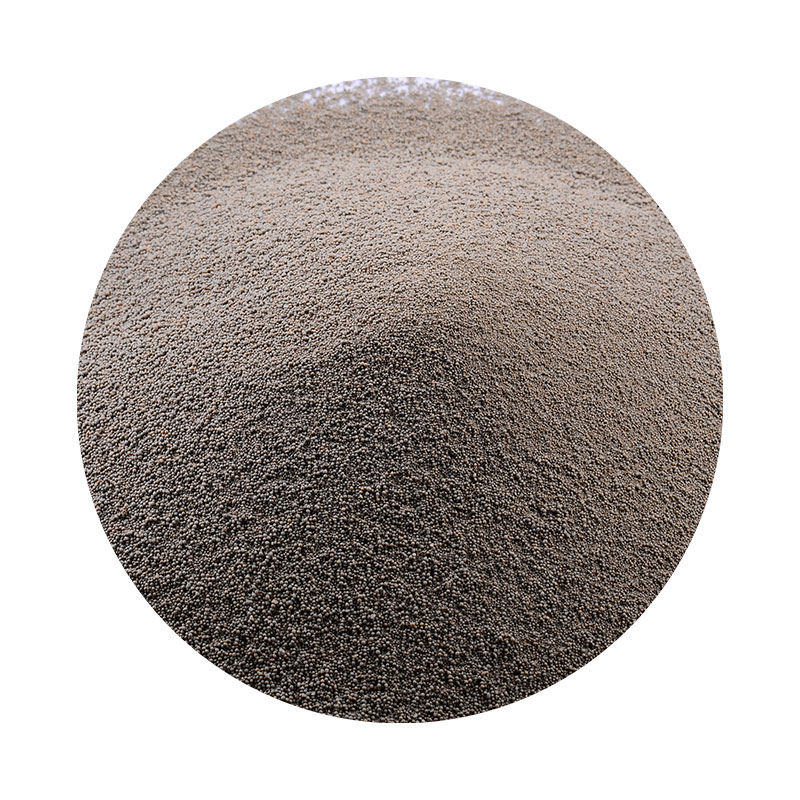
3. Large Size Capability Sand casting molds can be made to accommodate large castings. Industries that require the production of large components, such as wind turbines or heavy machinery parts, often rely on sand casting due to its capacity to create large molds without extensive tooling.
4. Complex Geometries Sand casting is particularly well-suited for creating intricate designs that would be challenging or impossible with other casting methods. The flexibility of shaping and the lack of stringent limitations mean that complex internal and external features can be achieved.
5. Low Tooling Costs Unlike other manufacturing processes such as die casting or investment casting, which require expensive molds and tooling, sand casting utilizes patterns and sand molds that can be produced at a lower cost. This factor makes sand casting accessible for custom or one-off products.
6. Recycling Capability Used sand can be cleaned and reused multiple times, reducing the environmental impact and material waste associated with casting. This recycling aspect points towards a sustainable manufacturing approach.
Applications of Sand Casting
The applications of sand casting are vast. In the automotive industry, it is used to manufacture engine blocks, transmission cases, and custom components. The aerospace sector benefits from sand casting for producing lightweight structural elements and details where precision is crucial. Additionally, the art and sculpture sectors utilize sand casting to create unique and complex artwork.
Conclusion
In summary, sand casting is a time-tested manufacturing process that has adapted to modern technological advancements. Its cost-effectiveness, versatility in material and design, and ease of operation make it a popular choice for various industries. As manufacturers continue to seek efficient and sustainable methods to create parts, sand casting remains a viable option, upholding its relevance in contemporary manufacturing practices. Whether you’re producing high-volume parts or unique, one-off components, sand casting is a valuable technique in the foundry landscape, proving that sometimes, the oldest methods are still the best.
Post time:नवम्बर . 10, 2024 11:28
Next:Comprehensive Sand Casting Solutions for Efficient Metal Fabrication and Production