Lost Foam Castings An Innovative Approach to Metal Casting
Lost foam casting (LFC) is a highly efficient and sophisticated casting process that has gained popularity in various manufacturing industries. This method utilizes the simplicity of foam patterns and the versatility of molten metal to produce high-quality castings with intricate details. As technology advances and industry demands evolve, lost foam casting has emerged as a preferred choice for manufacturers seeking precision and efficiency.
At the core of the lost foam casting process is the use of expendable foam patterns, which are made from polystyrene or other similar materials. The foam pattern is created by shaping it into the desired form, allowing for the reproduction of complex geometries with minimal undercuts. This enables designers to realize their vision without being limited by the constraints typically associated with traditional casting methods. Upon completion of the foam pattern, it is coated with a layer of sand and binders. This sand mold serves as the cavity into which molten metal will be poured.
Lost Foam Castings An Innovative Approach to Metal Casting
Moreover, the lost foam casting process is particularly advantageous for producing complex shapes that would otherwise be challenging or impossible to achieve with traditional sand casting methods. The ability to create intricate designs without the need for tooling sets LFC apart and allows for greater creativity in product development. This flexibility in design can lead to innovative solutions that optimize performance and functionality in the final product.
lost foam castings
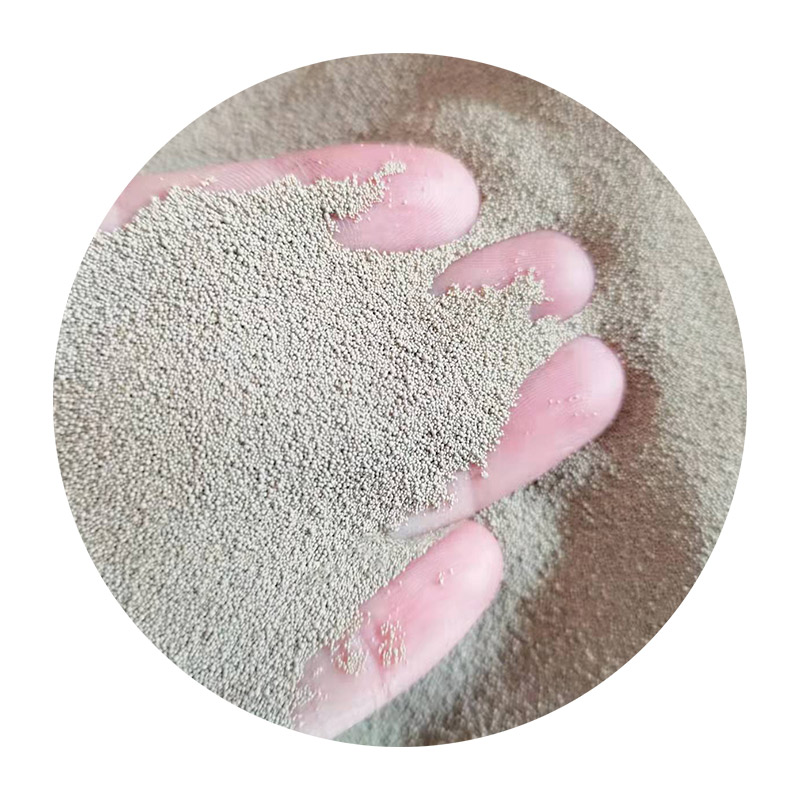
In addition to its design benefits, lost foam casting is also a more sustainable and environmentally friendly option compared to traditional casting techniques. The process generates less waste, as the foam used for patterns is completely consumed during casting. Additionally, LFC often uses recyclable materials, which minimizes the environmental impact. Companies that prioritize sustainability in their manufacturing processes can enhance their brand reputation while also contributing to a greener future.
Despite its numerous advantages, lost foam casting is not without its challenges. Achieving the ideal temperature control and managing the vaporization of the foam can be complex, requiring experienced personnel to oversee the process. Moreover, certain metals may not be suitable for this technique, limiting its applicability based on the material requirements of a specific project.
Nonetheless, ongoing advancements in technology and materials science continue to improve the lost foam casting process. Research is focused on enhancing the quality of foam patterns, optimizing the sand coatings, and refining the overall processing parameters to yield even better results. As manufacturers increasingly adopt automated solutions, the integration of robotics and digital monitoring systems is expected to elevate the efficiency and precision of lost foam casting.
In conclusion, lost foam casting is an innovative metal casting technique that offers remarkable benefits in terms of design flexibility, cost efficiency, and environmental sustainability. Its ability to produce high-quality castings with complex geometries positions it as a valuable method in various industries. As technology continues to evolve and improvements are made, lost foam casting is poised to play an even more significant role in the manufacturing landscape, helping to create the next generation of components that meet the demands of modern consumers and industries alike.
Post time:दिसम्बर . 13, 2024 21:11
Next:Understanding the Resin Sand Casting Technique for Efficient Metal Production