The Art and Science of Iron Sand Casting
Iron sand casting is a fascinating process that combines traditional techniques with modern technology to transform raw materials into intricate, functional metal components. This method involves the use of iron-rich sand, which is molded and shaped to create desired forms, all while retaining the intrinsic properties of iron. As we delve into the process, applications, and benefits of iron sand casting, it becomes apparent why this technique has stood the test of time and continues to play a crucial role in various industries.
Understanding Iron Sand Casting
At its core, iron sand casting involves the preparation of a mold using iron sand, typically composed of magnetite (Fe3O4) or other iron oxides. The process begins with the design of a pattern, which is a replica of the component to be created. This pattern can be made from various materials, including wood, metal, or plastic, and is crucial as it dictates the shape and dimensions of the final product.
Once the pattern is constructed, it is placed into a mold box, which is then filled with iron sand. The sand is compacted around the pattern to create a negative impression, forming the mold cavity. After the mold is prepared, the pattern is removed, leaving a hollow space that reflects the pattern's shape. The next step involves pouring molten iron into the mold cavity, where it will solidify and take the shape of the original pattern.
The Process of Sand Casting
The sand casting process can be broken down into several key steps
1. Pattern Making Designing and crafting a precise pattern to ensure accurate reproduction in the final casting. 2. Mold Preparation Mixing iron sand with a binding agent, usually a form of clay, and compacting it around the pattern.
3. Melting the Iron Heating iron to its melting point, typically around 1500°C (2732°F), and ensuring it reaches the desired viscosity for smooth pouring.
4. Pouring Transferring the molten iron into the mold cavity.
iron sand casting
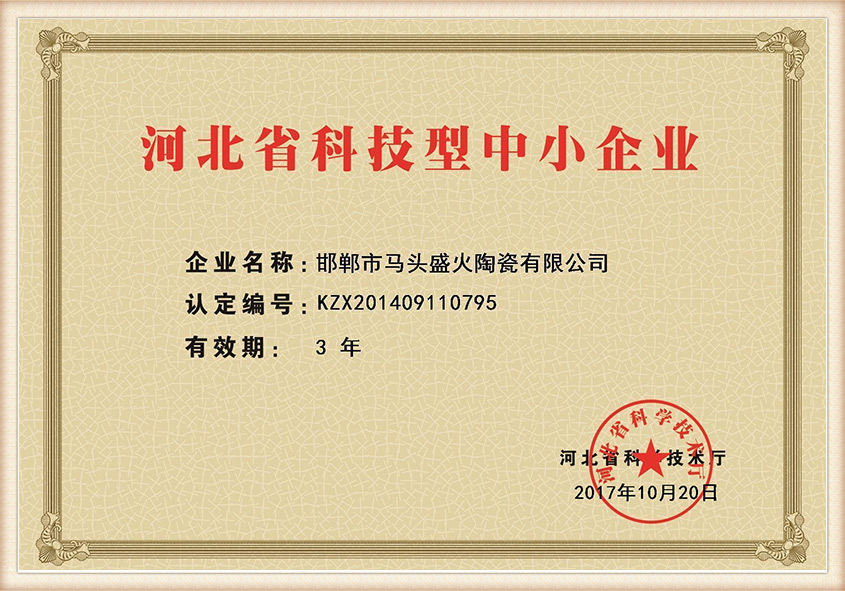
5. Cooling Allowing the cast to cool and solidify, which can take from several minutes to hours, depending on the size of the component.
6. Casting Removal Breaking away the sand mold to retrieve the finished iron casting.
7. Finishing Cleaning, machining, and inspecting the casting to meet the required specifications and tolerances.
Applications of Iron Sand Casting
Iron sand casting has diverse applications across multiple sectors. In the automotive industry, it is commonly used for manufacturing engine blocks, cylinder heads, and transmission housings due to the durability and strength of iron. The construction industry also benefits from this technique, producing components such as manhole covers, brackets, and architectural elements.
Moreover, the art of iron sand casting extends to artistic creations and sculptures. Skilled artisans utilize the technique to make intricate designs that showcase the beauty of iron while highlighting its versatility. In essence, the adaptability of iron sand casting exponentially increases its range of applications, from functional machinery parts to aesthetically pleasing art pieces.
Benefits of Iron Sand Casting
The advantages of iron sand casting are considerable. The method allows for high precision and the creation of complex shapes, which may not be feasible with other manufacturing techniques. Iron sand is also readily available, making the process cost-effective and environmentally friendly when using recycled materials.
Furthermore, the mechanical properties of cast iron, such as good wear resistance and excellent machinability, ensure that the final products are reliable and long-lasting. Additionally, the ability to produce large quantities in a single casting run enhances efficiency and productivity.
In conclusion, iron sand casting is a time-honored technique that marries artistry and engineering. From its intricate processes to its wide-ranging applications, it remains a vital manufacturing method. As industries continue to innovate and demand high-quality components, iron sand casting is poised to adapt and thrive, ensuring its legacy for years to come. Whether for functional uses or creative endeavors, the world of iron sand casting holds endless possibilities.
Post time:दिसम्बर . 22, 2024 17:06
Next:Services de moulage au sable personnalisés et de haute qualité pour vos projets industriels