The Cost of Sand Casting An Overview
Sand casting, a widely used metal casting process, involves pouring molten metal into a mold made from sand. This method is favored for its versatility and ability to produce complex shapes, making it essential in various industries such as automotive, aerospace, and manufacturing. However, understanding the costs associated with sand casting is crucial for businesses and individuals looking to invest in this manufacturing technique.
Breakdown of Sand Casting Costs
1. Material Costs The primary materials used in sand casting include sand, metal (such as aluminum, iron, or bronze), and other additives. The cost of high-quality sand can vary significantly based on its composition and purity. For instance, silica sand is commonly used and can cost approximately $20 to $50 per ton. The price of the metal is more variable, influenced by market fluctuations. As of 2023, aluminum might cost around $1 per pound, while cast iron could be closer to $0.50 per pound.
2. Labor Costs Sand casting requires skilled laborers to operate machinery, prepare molds, and manage the casting process. Labor costs can vary based on the region and the complexity of the project. On average, hourly rates for foundry workers may range from $15 to $30, depending on their skill level and experience. In addition to the basic labor costs, there may be additional expenses related to training and safety measures in the workplace.
3. Tooling and Equipment Creating molds and core boxes involves upfront investment. Tooling costs can be significant, especially for intricate designs. A basic mold might cost anywhere from $1,500 to $5,000, depending on its complexity and the type of metal being cast. Advanced tooling, especially for high-volume production, can exceed these estimates significantly.
4. Overheads Manufacturing facilities incur various overheads including utilities, maintenance, insurance, and administrative salaries. These costs should be factored into the overall price of sand casting. In smaller foundries, overhead might account for 30% to 50% of total costs.
how much does sand casting cost
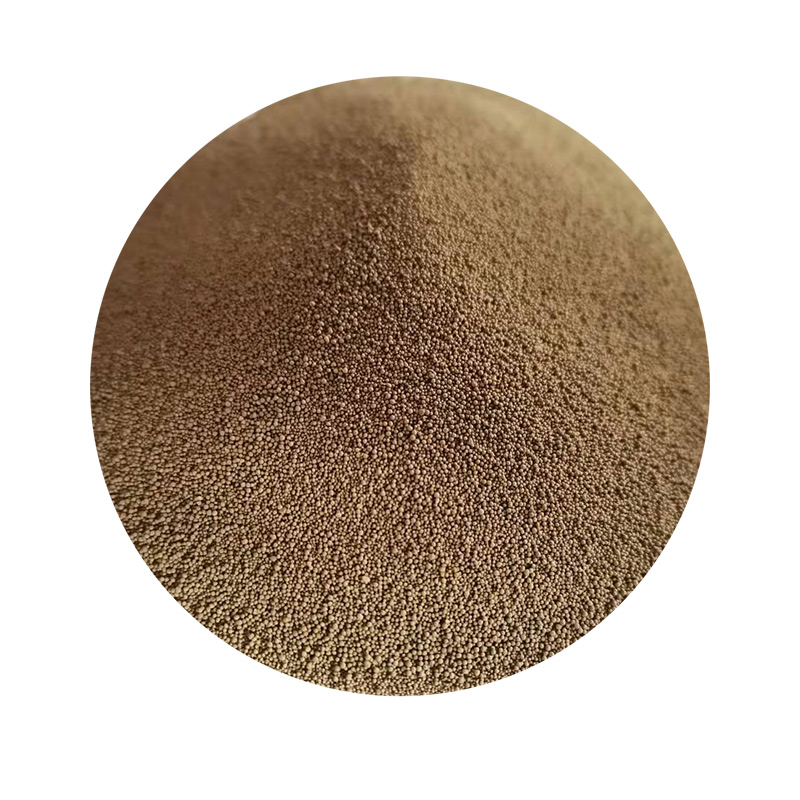
5. Production Volume The quantity of parts being produced will greatly influence the overall cost per unit. Higher production volumes typically reduce the cost per unit due to the amortization of tooling costs and labor. For instance, producing 100 units may yield a significantly lower cost per unit compared to producing just 10 units, thanks to economies of scale.
6. Post-Processing Costs After casting, parts often require additional finishing processes such as machining, cleaning, and inspection, which can add to the overall cost. Machining might add $0.50 to $3.00 per part, depending on the complexity and the time required for finishing.
7. Design Considerations The simplicity or complexity of the design impacts the price as well. More complex designs require more intricate molds, leading to higher costs. Variations in wall thickness, intricate detailing, or tight tolerances can significantly raise expenses.
Conclusion
In summary, the cost of sand casting is influenced by multiple factors, including material prices, labor, tooling, overheads, production volume, post-processing needs, and design complexity. On average, one can expect the total cost per part to range from $5 to $100 or more, depending on these variables.
For businesses or individuals considering sand casting, it’s essential to conduct a thorough cost analysis and communicate clearly with suppliers to obtain precise quotations. By understanding each component of the cost structure, manufacturers can make informed decisions and optimize their production processes for financial efficiency.
Post time:दिसम्बर . 13, 2024 12:26
Next:Innovative Techniques in Resin Sand Casting for Enhanced Metal Casting Efficiency