How Much Does Sand Casting Cost?
Sand casting is one of the oldest and most versatile metal casting processes available, widely used in industries for creating intricate metal components and parts. While the advantages of sand casting are well-known, potential customers often wonder, How much does sand casting cost? The answer to this question can vary significantly based on numerous factors, which we will explore in this article.
Understanding Sand Casting Costs
The cost of sand casting can be broken down into several components, each contributing to the final price
. These components include material costs, tooling expenses, labor charges, and overhead costs.1. Material Costs The primary materials used in sand casting are the metal to be cast and the sand itself. Common metals used include aluminum, iron, bronze, and magnesium, and the cost of these metals fluctuates based on market conditions. For instance, aluminum prices may be lower during certain periods, affecting the overall cost of the casting process. Additionally, the type of sand and any additives used in the mixture play a role in the material costs, as higher quality sand or specialized mixtures may increase expenses.
2. Tooling Expenses Tooling is a crucial aspect of the sand casting process. It involves creating a mold, which can be made from various materials, including metal or plastic. The cost of producing molds can vary based on their complexity and the type of metal being cast. For simple designs, tooling costs may be relatively low, but for more intricate patterns, expenses can escalate quickly. In some cases, companies may employ advanced techniques such as 3D printing to create molds, which can also influence costs.
3. Labor Charges Labor costs represent another significant factor in the overall pricing. Sand casting requires skilled labor for both the setup and the actual casting process. The labor rates can differ based on geographical location, the complexity of the project, and the experience level of the workers involved. Additionally, if the casting project requires extensive quality control or post-processing work, these costs will further increase the final price.
how much does sand casting cost
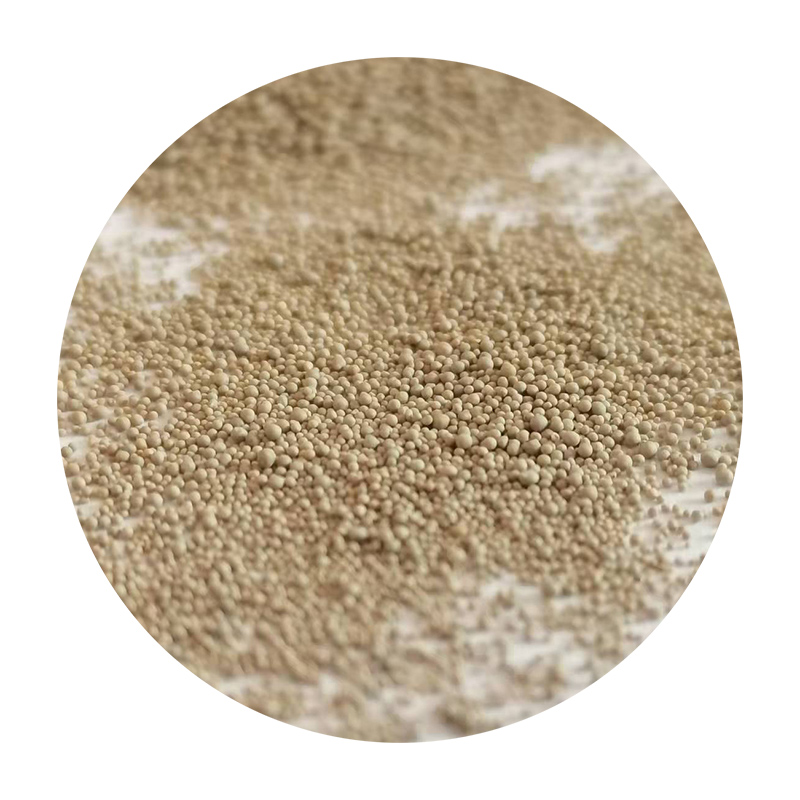
4. Overhead Costs Overhead expenses encompass everything from facility maintenance to utilities and administrative expenses. Foundries must consider these costs when determining pricing. Companies with more advanced technologies or those investing in sustainability practices may have higher overheads, which can be passed on to customers.
Cost Range
Given these factors, estimating the exact cost of sand casting can be challenging. However, on average, the cost of sand casting can range from $1 to $15 per pound, depending on the specifics of the project. For a more straightforward job, such as casting a small aluminum part, costs might fall on the lower end of this spectrum. Conversely, for a large, complex iron component, expect the price to rise significantly.
Economies of Scale
It's essential to note that the cost per unit can diminish significantly with larger production runs. When a foundry produces a high volume of parts, the initial tooling costs can be spread out over a greater number of units, resulting in a lower overall cost per item. This principle makes sand casting an attractive option for manufacturers looking to produce large quantities of identical parts.
Conclusion
In conclusion, the cost of sand casting is influenced by various factors, including material and tooling expenses, labor rates, and company overheads. Understanding these variables can help businesses better prepare for their casting projects and make more informed decisions regarding budgeting. Anyone considering sand casting for their manufacturing needs should consult with various foundries to obtain quotes and gain insight into the specific costs associated with their projects. This approach will ensure that you receive the best value for your investment in sand casting.
Post time:दिसम्बर . 10, 2024 19:38
Next:Innovative Techniques in Rapid Sand Casting for Enhanced Manufacturing Efficiency and Product Quality