The Accuracy of Sand Casting A Comprehensive Overview
Sand casting is one of the oldest and most widely used metal casting processes. It involves creating a mold from a mixture of sand and a bonding agent, typically clay, to produce metal parts. The accuracy of sand casting is a crucial factor for manufacturers when deciding on this method for producing components across various industries. This article delves into the intricacies of sand casting accuracy, exploring its strengths, limitations, and the factors that influence the final product’s quality.
Understanding Sand Casting
The sand casting process begins with creating a mold. The pattern, which represents the final part, is made from metal, plastic, or wood and is pressed into a sand mixture to create a negative impression. Once the mold is complete, molten metal is poured in. After cooling, the mold is broken away to reveal the cast part. This method is favored for its flexibility in producing complex shapes and its ability to accommodate various metals, such as aluminum, iron, and bronze.
Factors Influencing Accuracy
The accuracy of sand casting is affected by several factors
1. Mold Quality The quality and precision of the mold directly impact the final product's dimensions. A well-constructed mold will ensure tighter tolerances, resulting in a more accurate casting. Any imperfections or misalignments in the mold can lead to defects in the cast part.
2. Pattern Design The design of the pattern is critical. It must account for factors such as shrinkage, which occurs as the metal cools. Patterns are often oversized to compensate for this shrinkage. Moreover, the pattern's surface finish can affect the quality of the mold, thereby influencing the final casting accuracy.
how accurate is sand casting
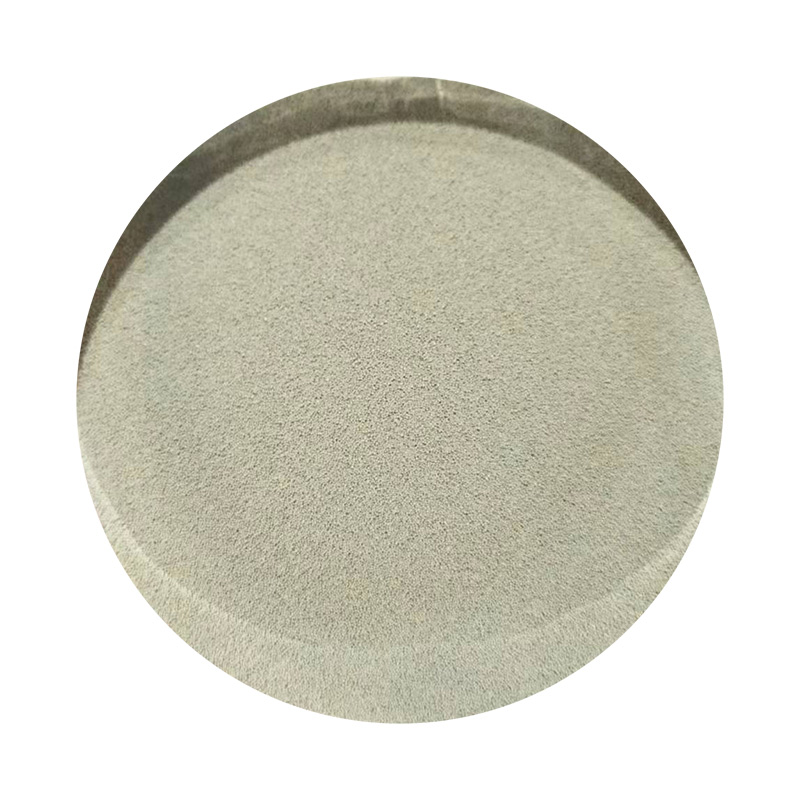
3. Sand Properties The type and quality of sand used play a vital role. Fine sands provide better surface finishes and allow for finer details, while coarser sands may lead to a rougher cast surface. Additionally, the moisture content and bonding agents used can affect the sand’s strength and ability to hold the shape under pressure.
4. Pouring Technique The method of pouring molten metal into the mold must be carefully controlled. Variations in temperature, pouring speed, and pressure can lead to issues such as misruns, cold shuts, or porosity, all of which can compromise accuracy.
5. Post-Casting Processes After the casting is complete, further treatments like machining or surface finishing can enhance accuracy. However, these processes may also introduce additional costs and time into the production schedule.
Pros and Cons of Sand Casting Accuracy
While sand casting can achieve notable accuracy, it is essential to recognize its limitations. It typically achieves tolerances of about ±0.5% of the part’s dimension, which can be sufficient for many applications. However, for parts requiring high precision—such as aerospace components—other methods, like investment casting or die casting, may be preferred.
Despite these limitations, sand casting offers several advantages, including cost-effectiveness for low-volume production and the ability to create large, complex parts. It is particularly beneficial for custom and one-off parts, where the cost of creating specialized molds for other casting processes would be prohibitively expensive.
Conclusion
In conclusion, sand casting is a versatile manufacturing process with a commendable track record for producing accurate metal parts. Its accuracy can be optimized through careful attention to mold quality, pattern design, material selection, and pouring techniques. While it may not always be the best choice for high-precision applications, its adaptability to different shapes and sizes, combined with cost-effectiveness, ensures it remains a popular choice in various manufacturing fields. Understanding the factors that influence accuracy will allow engineers and manufacturers to leverage sand casting effectively in their production processes.
Post time:दिसम्बर . 05, 2024 15:41
Next:sanding clear resin