Understanding Foundry Sand Properties, Types, and Applications
Foundry sand is a critical component in the metal casting process, primarily used in the production of molds and cores to create complex shapes and intricate designs in various metals. Its unique properties make it suitable for reusability and recycling, contributing to sustainable practices in foundries. This article will explore the types, properties, and applications of foundry sand, as well as its role in modern manufacturing.
Types of Foundry Sand
There are several types of foundry sand, each suited to different casting processes
1. Silica Sand The most commonly used type of foundry sand, silica sand is primarily composed of silicon dioxide (SiO2). Its high melting point and grain structure make it ideal for creating molds that can withstand the intense heat of molten metal. Its availability and cost-effectiveness further cement its popularity in foundry operations.
2. Green Sand This is a mixture of silica sand, clay, and water, which provides the binding properties needed for mold making. The clay component helps the sand grains stick together, allowing for intricate mold designs. Green sand is particularly popular due to its ease of use and the ability to create smooth surface finishes.
3. Resin Sand This type of sand is coated with a resin or a binder, enhancing the strength and durability of the molds. Resin sands are typically used in processes that require higher precision and finer details. They offer excellent dimensional accuracy and surface quality, making them ideal for intricate castings.
4. Shell Molding Sand A type of sand bonded with thermosetting resins, shell molding sand is used to produce thin-walled molds. Its application allows for finer surface finishes and more complex geometries, making it a preferred choice for high-volume production.
Properties of Foundry Sand
The properties of foundry sand are paramount to its functionality in the casting process
- Grain Shape and Size The shape and size of sand grains significantly affect the mold quality and casting surface finish. Round grains pack more densely and provide better flowability, while angular grains offer superior strength.
foundry sand pdf
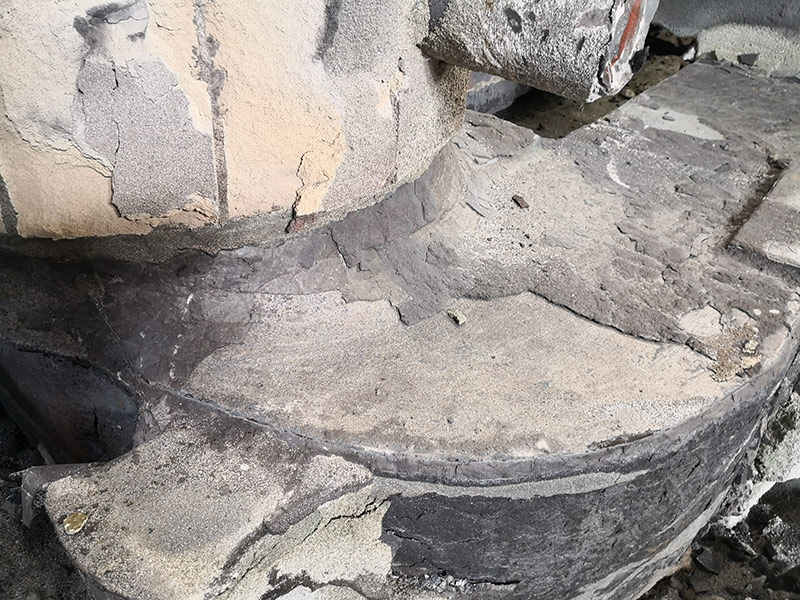
- Refractoriness This property refers to a sand's ability to withstand high temperatures without melting or deforming. Silica sand has high refractoriness, which is essential for maintaining mold integrity during casting.
- Moisture Content The right moisture level is crucial in foundry sand, as it affects the bonding and strength of the mold. Too much moisture can lead to defects, while too little can result in weak mold structures.
- Cohesiveness This governs how well the sand binds together, which is crucial for maintaining mold shape during the pouring of molten metal.
Applications of Foundry Sand
Foundry sand is widely used across various industries
1. Automotive Industry Castings are integral in manufacturing automotive components like engine blocks, transmission cases, and intricate parts that require precision and strength.
2. Aerospace Industry With high standards for quality and performance, foundry sand is utilized to create parts that can withstand extreme conditions, ensuring safety and reliability.
3. Consumer Goods Household items and appliances often rely on foundry processes for components made from metals that require precise casting techniques.
4. Marine Structures Foundry sand also plays a role in producing parts for ships and offshore structures, where durability and resistance to harsh environments are essential.
Conclusion
Foundry sand plays an invaluable role in metal casting processes, supporting a wide array of industries by providing strength, precision, and cost-effectiveness. Understanding the different types of foundry sand, along with their unique properties and applications, is essential for manufacturers looking to optimize their processes and produce high-quality metal components. The ongoing advancements in materials science and environmental practices also promise to enhance the sustainability and efficiency of foundry sand use in the future.
Post time:दिसम्बर . 30, 2024 19:41
Next:Exploring the Role of Sand in Enhancing Sand Casting Techniques and Applications