Dry Sand Casting Process An Overview
Dry sand casting, also known as green sand casting, is a widely used metal casting process that involves the creation of metal parts and components by pouring molten metal into a mold made from sand. Unlike traditional sand casting, dry sand casting utilizes a special blend of sand that is treated and dried, yielding several advantages in terms of precision and surface finish. This article explores the dry sand casting process, its advantages, applications, and best practices for achieving optimal results.
The Dry Sand Casting Process
The dry sand casting process begins with the preparation of the dry sand mixture. This mixture typically comprises sharp, uniform grains of silica sand combined with additives such as clay and water to bind the grains together. The sand is then heated to remove moisture, ensuring that when the molten metal is introduced, there will be minimal reaction between the sand and the metal.
Next, a pattern, usually made from metal or plastic, is created to form the shape of the desired part. This pattern is placed in a flask, a box that holds the sand, and the dry sand mixture is packed around the pattern. The sand is tightly compacted to form a rigid mold that can withstand the weight and heat of the molten metal. Once the sand is compacted, the pattern is carefully removed, leaving a hollow cavity that replicates the desired component.
After this, the mold halves are assembled and any gating systems required for pouring the metal are installed. Gating systems are essential for controlling the flow of the molten metal into the mold cavity. Once everything is set up, the steel or metal is heated and melted in a furnace. With utmost care, the molten metal is poured into the mold through the gating system.
Once the metal cools and solidifies, the mold is broken apart, and the casting is removed. The casting usually requires a finishing process to remove any imperfections, improve surface finish, and ensure dimensional accuracy. This often involves machining or surface treatments.
Advantages of Dry Sand Casting
dry sand casting process
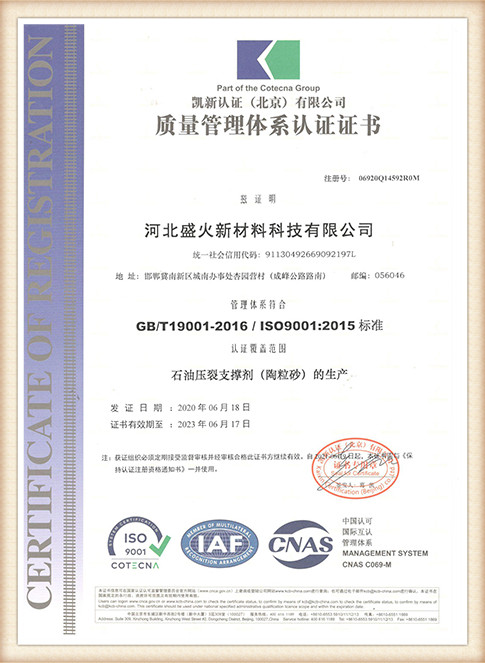
One of the main advantages of dry sand casting is its ability to produce high-quality casting with excellent surface finishes. The dry nature of the sand mixture prevents moisture-related defects such as porosity and gas inclusions, commonly found in traditional sand casting. Additionally, dry sand molds are more dimensionally stable and can be reused multiple times, making the process cost-effective and efficient.
Furthermore, dry sand casting allows for greater detail and more complex geometries, providing manufacturers with the ability to produce intricate designs. The method is also adaptable for various metals, including ferrous and non-ferrous alloys, making it versatile for different applications in industries such as automotive, aerospace, and construction.
Applications
The applications of dry sand casting are vast and encompass a variety of industries. In the automotive sector, it is often used to create engine blocks, cylinder heads, and other critical components that require durability and precision. In the aerospace industry, dry sand casting can be utilized for the production of lightweight yet strong aircraft parts. Furthermore, the construction industry frequently relies on this casting process to produce components like decorative architectural elements and structural supports.
Best Practices for Optimal Results
To achieve the best results in dry sand casting, manufacturers need to adhere to specific best practices. It is essential to ensure the consistency of the sand mixture, maintain optimal compaction levels, and closely control the pouring temperature of the molten metal. Regular inspections and testing of molds can prevent defects, and investing in quality patterns can enhance the overall quality of castings.
In conclusion, the dry sand casting process is a robust and efficient method for producing high-quality metal parts. Its unique advantages make it suitable for a wide range of applications, which continues to evolve as technology advances. As manufacturers continue to explore its potential, dry sand casting remains a vital component in modern manufacturing processes.
Post time:दिसम्बर . 22, 2024 21:14
Next:Innovative Techniques in Lost Foam Casting for Enhanced Metal Fabrication Processes