Dry Sand Casting A Comprehensive Overview
Dry sand casting is a widely utilized metallurgical process that allows for the creation of metal parts with complex shapes and high dimensional accuracy. This technique is particularly favored in industries where high-quality castings are essential. The dry sand casting process has several advantages, such as the ability to produce intricate geometries, excellent surface finish, and minimal distortion during cooling.
The Basics of Dry Sand Casting
At its core, dry sand casting involves the preparation of a mixture of sand, clay, and water. Unlike traditional sand casting methods, where the mold remains damp, dry sand casting uses a non-hygroscopic sand that requires minimal moisture. The absence of excess water prevents the mold from deforming and enables a consistent and uniform casting process.
The process begins with creating a mold using dry sand. This sand mixture is typically bonded with a clay binder, which provides strength to the mold and allows it to hold its shape during the casting operation. After assembling the mold halves, a pattern—a replica of the desired object—is placed within the sand. When the sand is compacted around the pattern, it takes on its shape. Once the mold is completed, the pattern is carefully removed, leaving a hollow cavity that will be filled with molten metal.
Key Steps in the Dry Sand Casting Process
1. Pattern Fabrication Patterns can be made from various materials, including metal, plastic, or wood. The choice of material depends on the required precision, production volume, and budget.
2. Mold Making The dry sand mixture is compacted around the pattern to create the mold. This process typically involves mechanical vibration or manual techniques to ensure the sand has sufficient density and strength to retain the shape during metal pouring.
3. Pouring Molten Metal Once the mold is ready, molten metal is poured into the cavity. The metal must reach the desired temperature and composition to ensure it flows properly and fills all sections of the mold effectively.
dry sand casting
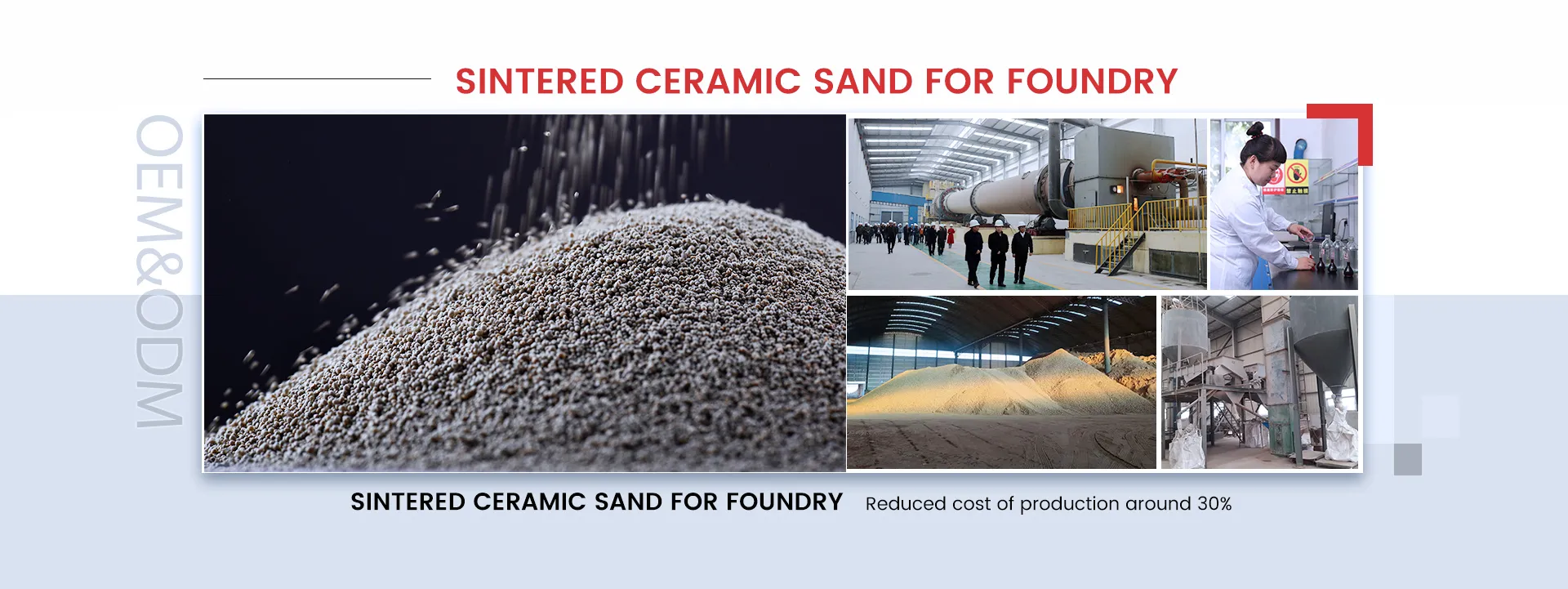
4. Cooling and Solidification After pouring, the molten metal begins to cool and solidify. The cooling rate can significantly impact the final properties of the casting, such as strength and surface finish.
5. Mold Removal Once the metal has cooled sufficiently, the sand mold is broken away, revealing the final casting. This requires careful handling to avoid damaging the cast part.
6. Finishing Operations The final step often involves cleaning the casting, removing any residual sand, and performing machining operations to achieve the desired tolerances and surface finishes.
Advantages and Applications of Dry Sand Casting
The primary advantages of dry sand casting include its ability to produce high-quality castings with excellent surface finishes and dimensional stability. Additionally, it allows for swift production cycles and can be utilized for both small and large scale manufacturing processes.
Dry sand casting is widely used in various industries, including automotive, aerospace, marine, and energy. Components such as engine blocks, pump housings, and intricate machine parts often rely on this casting technique for their manufacturing.
Conclusion
In summary, dry sand casting is a versatile and effective method for producing high-quality metal components. Its unique process characteristics provide numerous benefits, making it a reliable choice for manufacturers looking to achieve precision and quality in their cast products. As advancements in materials and technology continue to evolve, dry sand casting will remain an essential technique in the foundry industry, meeting the demanding requirements of modern engineering applications.
Post time:नवम्बर . 27, 2024 20:28
Next:Tips for Sanding Ceramic Surfaces to Achieve a Smooth Finish