The Role of Ceramic Foundry Sand in Modern Manufacturing
In the world of metal casting, the materials and methods used in the foundry process are crucial to ensuring product quality and efficiency. Among these materials, ceramic foundry sand has emerged as a prominent player due to its unique properties and advantages over traditional sand types.
Ceramic foundry sand, predominantly composed of spherical aluminosilicate particles, offers a notable improvement in the casting process. Its spherical shape allows for better flowability, reducing the friction between particles and leading to a denser, more uniform mold. This characteristic enables the creation of more intricate designs with higher precision—a key factor in industries ranging from automotive to aerospace.
One of the most significant advantages of ceramic foundry sand is its high resistance to thermal shock. In casting applications, the temperature can fluctuate significantly as molten metal is poured. Traditional sands may crack or deform under these extreme conditions, compromising the mold's integrity. However, ceramic sands maintain their structural stability, ensuring that the final cast product is not only consistent in shape but also of superior quality.
ceramic foundry sand
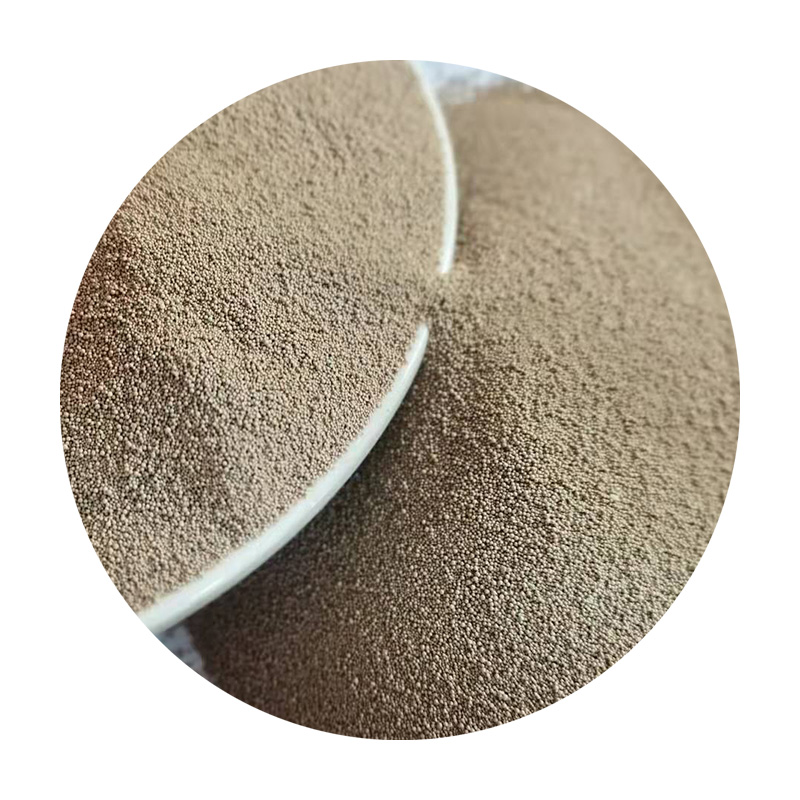
Moreover, ceramic foundry sand has a lower expansion rate than conventional sands, which minimizes the issue of mold shifting or deformation during the cooling process
. This characteristic is particularly beneficial when producing complex geometries where dimensional accuracy is of paramount importance. As a result, manufacturers are increasingly turning to ceramic sands to enhance the precision of their castings, ultimately leading to better-fitting components that require less machining.Environmental concerns also play a significant role in the adoption of ceramic foundry sand. Traditional sand casting methods often involve the use of materials that can be detrimental to the environment, such as silica sand, which can pose health risks to workers due to inhalation. Ceramic foundry sand, on the other hand, is often produced from recyclable materials and is less hazardous, aligning with the industry's growing emphasis on sustainability.
The economic impact of using ceramic foundry sand is another aspect worth considering. Although the initial cost of ceramic sand can be higher than that of traditional sand, its benefits often offset these initial expenses. Reduced waste, fewer rework costs due to improved casting precision, and shorter processing times contribute to lower overall production costs. As manufacturers seek to improve their bottom line, investing in ceramic foundry sand becomes an attractive proposition.
In conclusion, ceramic foundry sand is redefining the metal casting landscape. Its superior flowability, resistance to thermal shock, low expansion rate, environmental friendliness, and cost-effectiveness position it as a leading material in modern foundry applications. As industries continue to demand higher precision and efficiency in manufacturing, the role of ceramic foundry sand will likely expand, ushering in a new era of casting technology that prioritizes both quality and sustainability. The future of casting may very well rest in ceramic sands, transforming not only how we produce but also the environmental impact of those processes.
Post time:अक्टूबर . 31, 2024 12:13
Next:Golden Sands Concrete Solutions for Durable and Reliable Construction Projects