The 3D Sand Printing Process Revolutionizing Manufacturing
The advent of 3D printing technology has marked a significant turning point in the manufacturing sector, with various techniques being adapted for diverse materials. Among these innovations, the 3D sand printing process has emerged as a unique and transformative method, primarily used in the production of complex geometries for industries ranging from aerospace to automotive. This article delves into the intricacies of the 3D sand printing process, exploring its methodology, advantages, and applications.
Understanding 3D Sand Printing
3D sand printing, often referred to as binder jetting, involves the use of sand as the primary material, combined with a binding agent to create three-dimensional objects. Unlike traditional sand casting, where patterns are made from metal or wood and require complex assembly, 3D sand printing simplifies this with a layer-by-layer approach. The process begins with a digital design, typically created using CAD (Computer-Aided Design) software. This model is translated into a series of layers, which will guide the printer during production.
The printing process initiates by spreading a thin layer of sand onto a build platform. A specialized printer then deposits a liquid binder onto the sand in the precise areas dictated by the digital model. This binder adheres the sand particles together, forming a solid structure. Once a layer is completed, the platform lowers, and a new layer of sand is applied, repeating the process until the entire object is built. After printing, the loose sand is brushed away, leaving behind a highly detailed and intricately designed object.
Advantages of 3D Sand Printing
One of the most significant benefits of 3D sand printing is its ability to create complex geometries that would be challenging or impossible to achieve with traditional manufacturing techniques. This capability allows for the production of lightweight structures with intricate internal channels, which are crucial for applications in cooling systems or lightweight components in aerospace engineering.
Moreover, 3D sand printing is highly efficient and reduces waste significantly. Conventional methods often involve substantial material loss during machining or casting processes. In contrast, the layer-by-layer approach used in 3D sand printing ensures that only the necessary material is used, minimizing scrap and optimizing resource utilization.
3d sand printing process
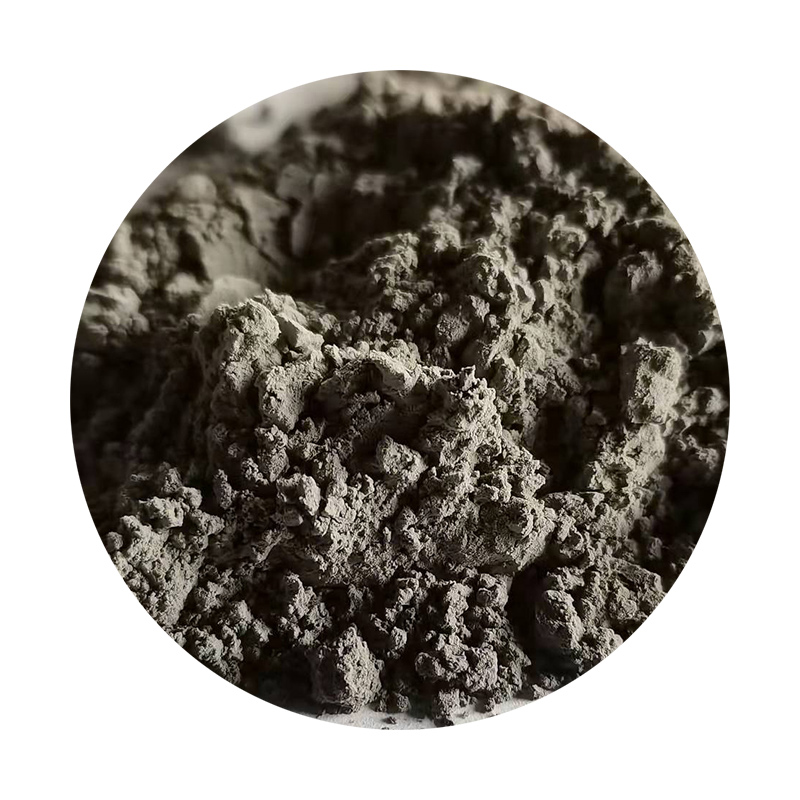
Additionally, the process enables rapid prototyping, allowing manufacturers to produce and alter designs quickly. This flexibility is essential in industries where innovation and speed to market can determine competitiveness. A single file can lead to the production of numerous prototypes, each customizable to fit specific requirements or improvements, reducing time and cost dramatically.
Applications of 3D Sand Printing
The applications of 3D sand printing are vast and varied. In the automotive industry, manufacturers use this technique for creating sand molds and cores for casting engines, which streamlines the production process while enhancing design capabilities. This method allows for the development of lighter parts, contributing to overall fuel efficiency.
In the aerospace sector, where precision and weight are paramount, 3D sand printing is employed to produce complex components that optimize performance while adhering to strict safety standards. This technology also finds a vital role in the field of art and architecture, allowing designers to produce elaborate models or unique sculptures that wouldn’t be feasible with traditional sculpting methods.
Furthermore, the ability to produce custom molds on demand has made it easier for businesses in various sectors to enter niche markets, providing tailored solutions without the need for significant upfront investment in tooling.
Conclusion
The 3D sand printing process stands as a testament to the evolving landscape of manufacturing technology. By merging efficiency with unprecedented design freedom, it is paving the way for innovation across numerous industries. As advancements continue to enhance the capabilities and applications of this technology, it is clear that 3D sand printing will play an increasingly prominent role in shaping the future of manufacturing, pushing the boundaries of what is possible in production and design. The potential for customization, reduced waste, and enhanced performance makes it an essential tool in the modern manufacturer's arsenal, fundamentally redefining how products are conceived and created.
Post time:नवम्बर . 12, 2024 02:28
Next:cheap sand casting