The 3D Sand Printing Process Revolutionizing Manufacturing and Design
3D sand printing is an innovative technique that is transforming the fields of manufacturing, design, and engineering. This advanced process leverages the principles of additive manufacturing to produce complex sand molds and cores used primarily in metal casting. By utilizing a digitally controlled sand printer, manufacturers can create intricate designs with unprecedented precision and speed. This article explores the intricacies of the 3D sand printing process, its advantages, applications, and future potential.
Understanding the Process
The 3D sand printing process begins with the creation of a computer-generated model designed using Computer-Aided Design (CAD) software. This digital model is then converted into a format that the sand printer can interpret. The printer uses a binding agent to selectively solidify layers of sand, building the model layer by layer from the bottom up. Unlike traditional sand casting methods, which rely on physical patterns, 3D sand printing allows for the direct creation of molds without the need for tooling.
As the printer works, it deposits a thin layer of sand across the build platform. Following this, a liquid binder is sprayed onto the sand, causing the particles to adhere together. This process is repeated in successive layers until the final part is completed. The resulting mold or core is incredibly accurate, featuring fine details that are difficult or impossible to achieve with traditional methods. After printing, any excess sand is removed, and the mold is ready for metal casting.
Advantages of 3D Sand Printing
One of the primary advantages of 3D sand printing is its ability to produce complex geometries. Traditional sand casting often involves extensive machining and manual labor to create intricate patterns. In contrast, 3D sand printing allows for the instantaneous creation of complex designs without the high costs associated with tool manufacturing. This capability is particularly beneficial in industries where customized parts are crucial, such as in aerospace and automotive sectors.
Another significant benefit is the reduction of lead times. Conventional mold-making processes can take weeks, if not months, to complete. However, 3D sand printing can produce molds in a fraction of the time, sometimes in just hours. This optimization of time and resources enables manufacturers to respond quickly to changes in market demand, prototype new designs faster, and reduce time-to-market for new products.
3d sand printing process
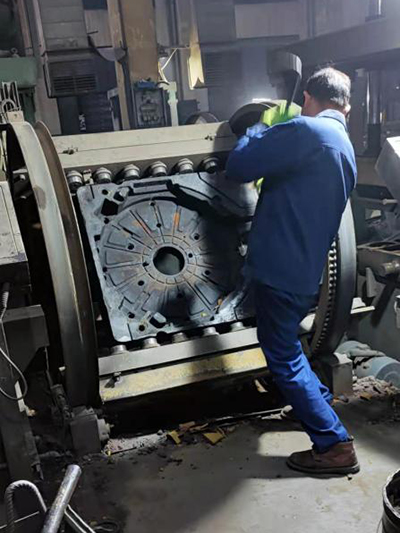
Moreover, there is a notable reduction in material waste associated with 3D sand printing. Traditional molding processes often result in significant waste as excess material is trimmed away. With 3D sand printing, the additive nature of the process ensures that only the necessary material is used, contributing to more sustainable manufacturing practices.
Applications in Various Industries
The applications of 3D sand printing are vast and varied. In the automotive industry, it is used to create prototype parts and custom components for vehicles. Companies can design and test intricate designs rapidly, allowing engineers to iterate on designs without the prohibitive costs of traditional tooling.
In the aerospace sector, where weight reduction is a critical factor, 3D sand printing enables the production of lightweight components that maintain structural integrity. This technology is also being explored for medical applications, where custom prosthetics can be designed and produced to fit an individual’s anatomy, offering improved comfort and functionality.
Future Potential
The future of 3D sand printing looks promising as technology continues to advance. Innovations in materials science, particularly the development of new binders and sand compositions, will enhance the performance and capability of sand printing. Furthermore, as businesses shift towards more sustainable and efficient practices, the adoption of 3D sand printing is likely to increase.
In conclusion, the 3D sand printing process represents a significant leap forward in manufacturing technology. With its ability to produce intricate designs quickly and with minimal waste, it is revolutionizing industries from automotive to aerospace and beyond. As the technology evolves, it will undoubtedly lead to new applications and improvements, making it an essential tool for the future of manufacturing and design.
Post time:अक्टूबर . 19, 2024 09:32
Next:Exploring the Role of Facing Sand in Foundry Processes and Metal Casting Techniques