Why is Sand Casting Used?
Sand casting, one of the oldest and most versatile metal casting processes, has remained a preferred method for manufacturing metal parts and components across various industries. This technique involves creating a mold from compacted sand, into which molten metal is poured to shape the desired object. Despite the advancements in materials and technologies, sand casting is widely utilized due to its numerous benefits and inherent advantages.
First and foremost, the primary advantage of sand casting is its cost-effectiveness. The materials used in sand casting—primarily sand, clay, and water—are readily available and inexpensive. This makes sand casting an attractive option for both small-scale production and large-scale manufacturing. Additionally, the equipment required for sand casting, such as molds, patterns, and furnaces, is relatively low in cost compared to other casting methods. Therefore, companies can save capital investment while achieving effective production.
Another significant benefit of sand casting is its flexibility in terms of part size and complexity. Sand casting can produce a wide range of metal components, from small intricate parts to large heavy machinery components. This capability stems from the nature of sand itself, which can easily accommodate detailed features and complex geometries. As a result, engineers and designers enjoy the freedom to create innovative designs without worrying about the limitations that other methodologies, like die casting, may impose.
Moreover, sand casting supports various metals and alloys, including iron, aluminum, copper, and magnesium, among others. This versatility empowers manufacturers to select materials that best fit the performance requirements of their products. Different materials can possess distinctive properties, such as strength, weight, and corrosion resistance, allowing designers to optimize their products for specific applications.
why is sand casting used
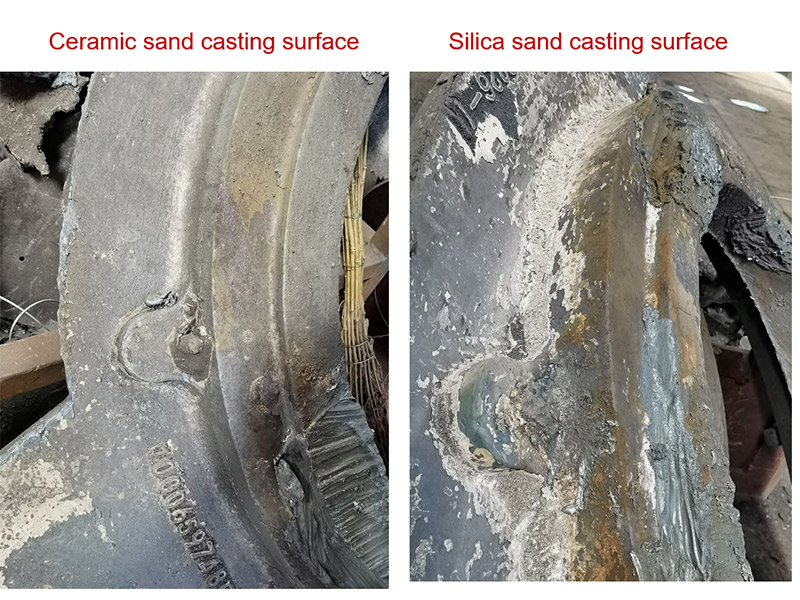
The production process in sand casting accommodates low-volume production runs efficiently. In many industries, the need for custom or low-volume parts is prevalent. Sand casting can adapt to these needs, as patterns can be made quickly and modified easily. This ability to produce small batch runs without significant tooling costs or delays positions sand casting as an efficient solution for bespoke projects or prototypes.
Additionally, the sand casting process yields excellent surface finish and dimensional accuracy. While the surface finish obtained may not match that of more advanced casting methods, processes like sand blasting or machining can be employed post-casting to achieve the desired quality. Furthermore, the inherent properties of sand ensure that thermal expansions and contractions during the cooling phase do not significantly distort the shape of the castings, thus maintaining dimensional integrity.
Environmental considerations also play an essential role in the growing adoption of sand casting. The process generates minimal waste, as used sand can be recycled and reused multiple times, reducing environmental footprint. Additionally, with the rise of green sand casting techniques, manufacturers can now utilize eco-friendly materials that further lessen the impact on nature while maintaining the benefits of traditional sand casting processes.
Lastly, sand casting enables excellent production rates, particularly in a foundry setting where multiple parts can be cast simultaneously. As a result, manufacturers can meet high-demand requirements without compromising on quality or performance. This efficiency means that industries relying on swift turnaround times, such as automotive and aerospace, can depend on sand casting for critical components.
In conclusion, the continued popularity of sand casting is attributable to its cost-effectiveness, versatility, flexibility, and relatively straightforward production process. As it supports a wide range of materials and can produce components of various sizes and complexities, sand casting remains indispensable in modern manufacturing. While it faces competition from other casting methods, the distinct advantages it offers ensure its relevance in fulfilling the diverse needs of industries across the globe. Whether it’s for creating automotive parts, machinery components, or artistic sculptures, sand casting is a method that embodies both tradition and innovation in the metalworking landscape.
Post time:ינו . 01, 2025 11:34
Next:Enhancing Lost Foam Casting with Advanced Coating Techniques for Optimal Results