Why is Sand Casting Used?
Sand casting is one of the oldest and most widely used metal casting processes, and it has stood the test of time for a multitude of reasons. This method involves using sand as the primary molding material, and it is revered for its versatility, cost-effectiveness, and adaptability in various fields, including automotive, aerospace, and manufacturing industries. This article explores the reasons behind the continued popularity of sand casting.
1. Cost-Effectiveness
One of the most significant advantages of sand casting is its cost-effectiveness. The raw materials used in sand casting—primarily sand, metal, and a bonding agent—are relatively inexpensive compared to other casting methods. Moreover, the equipment necessary for sand casting is generally less expensive to acquire and maintain. This lower investment barrier makes sand casting an attractive option for small to medium-sized businesses, as well as large-scale productions.
2. Versatility and Flexibility
Sand casting is highly versatile. It can accommodate a broad range of metal alloys, including aluminum, bronze, iron, and magnesium. This versatility allows manufacturers to choose materials that suit specific application requirements and performance characteristics. In addition, sand casting can produce complex shapes and large components. This flexibility in design is particularly beneficial in industries that require intricate features, such as automotive and aerospace sectors.
3. Large-Scale Production Capability
Sand casting is well-suited for both one-off and large-scale production runs. It can efficiently produce small quantities of parts for prototyping, as well as high volumes for mass production. The process can be easily adjusted to accommodate different production scales without significant alterations in tooling or setup. This makes it a preferred choice for companies that produce a range of products with varying demand levels.
4. Complexity and Surface Finish
why is sand casting used
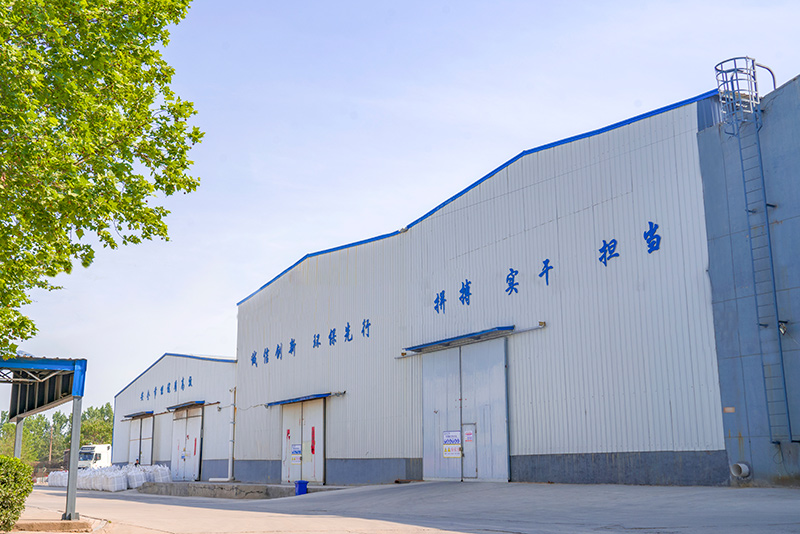
While sand casting is often viewed as a method suited for basic shapes, it is surprisingly capable of producing complex geometries. Advanced techniques, such as the use of 3D printed molds or cores, allow for intricate designs that would be challenging with other casting techniques. Furthermore, although sand casted parts typically have a rough surface finish, modern treatments and post-processes can improve this aspect significantly, meeting the requirements for many applications.
5. Easy to Modify
The sand casting process can be easily modified to accommodate changes in design or to correct errors, making it a flexible option for manufacturers. If a design requires alterations, modifications can be made relatively quickly without the need for extensive retooling or significant downtime. This adaptability is particularly beneficial in industries where design changes are common.
6. Environmental Benefits
In today's environmentally conscious world, sand casting has an advantage due to its relatively low environmental impact compared to other casting processes. Most of the materials used in sand casting can be reused multiple times, and many foundries are adopting practices to recycle sand. This reduces waste and aligns with the sustainability goals of many modern manufacturing facilities.
7. Accessibility and Skill Availability
The skill level required for sand casting is widely accessible. Many technicians and craftsmen are trained in traditional sand casting techniques, and the learning curve is achievable for those entering the field. This widespread availability of skilled labor helps facilitate easier implementation of sand casting processes across various industries.
Conclusion
In summary, sand casting remains a highly favored method in metal fabrication due to its cost-effectiveness, versatility, adaptability to complex designs, and environmental sustainability. Its capacity to scale from small to large production runs and the ease of modifying molds make it a practical choice for many manufacturers. As industries continue to evolve, sand casting will likely remain a relevant and valuable casting method, affirming its place in modern manufacturing. The combination of traditional practices and modern technologies ensures that sand casting will continue to meet the diverse needs of today’s market.
Post time:נוב . 10, 2024 17:06
Next:Innovative Applications of Resin Bound Sand in Modern Construction and Landscaping