The Sand Foundry Process A Comprehensive Overview
The sand foundry process is a crucial technique widely applied in metal casting, allowing for the production of complex shapes with high precision and tolerances. This method has been around for centuries, evolving from traditional practices into a modern, refined operation. In this article, we will explore the intricacies of the sand foundry process, covering its components, advantages, and applications.
At its core, the sand foundry process begins with the preparation of a mold made of sand. Sand is favored for its excellent thermal properties, availability, and the ability to produce intricate designs. The two primary types of sand used are silica sand and clay-based sand. Silica sand, known for its high melting point, helps withstand the heat produced during metal casting, while clay sand, often mixed with a binder, adds cohesion to the mold.
The first step in the sand foundry process is the creation of a pattern, which is essentially a replica of the final product
. Patterns can be made from various materials, including metal, wood, or plastic, and can be created using traditional woodworking techniques or advanced machining methods. The design of the pattern must consider factors such as shrinkage and draft angles to ensure that the final cast piece meets the required specifications.Once the pattern is ready, it is placed in a molding box, which is then filled with a mixture of sand and a binder. This mixture is compacted around the pattern to create a mold cavity. The compaction process is critical as it influences the mold's strength and the quality of the cast. Various techniques, such as manual ramming or mechanical molding machines, can be employed to ensure the sand is densely packed.
sand foundry process
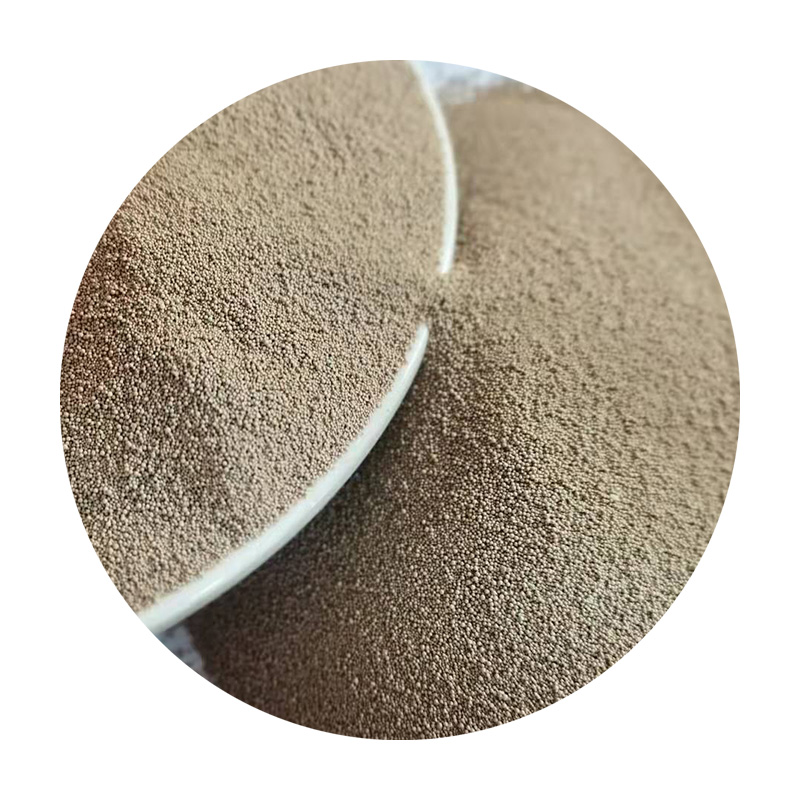
After the mold is created, the pattern is removed, leaving behind a hollow cavity that mirrors the shape of the intended product. The mold is then typically coated with a fine layer of sand to enhance surface finish and to prevent the metal from sticking to the mold. Additionally, gating systems are incorporated to allow molten metal to flow into the mold and air to escape, minimizing defects in the final casting.
With the mold prepared, the next stage involves melting the metal, which can be aluminum, iron, steel, or any other suitable alloy. Melting is performed in furnaces designed to achieve the high temperatures necessary for the specific metal. Once the metal reaches its molten state, it is carefully poured into the mold through the gating system, ensuring an even distribution throughout the cavity.
Upon solidification, the mold is broken open to reveal the cast product. This phase may involve various finishing operations, such as grinding, machining, and surface treatment, to achieve the desired specifications and surface finish. The sand used in the mold can often be reused after proper cleaning, making the sand foundry process an environmentally friendly option.
The sand foundry process is advantageous due to its adaptability, cost-effectiveness, and capability to produce large volumes of castings in diverse shapes and sizes. Its applications can be found across numerous industries, including automotive, aerospace, construction, and art. Despite the advent of advanced manufacturing technologies, sand casting remains a vital method revered for its reliability and versatility.
In conclusion, the sand foundry process is a fundamental technique in the field of metalworking that continues to evolve while maintaining its relevance across various industries. Understanding the detailed steps and materials involved helps appreciate the artistry and engineering that go into creating everything from intricate components to massive structural elements. As technology advances, the sand foundry process is likely to further refine its techniques, ensuring its place in the manufacturing landscape for years to come.
Post time:אוק . 02, 2024 01:10
Next:A Guide to Creating Your Own Foundry Sand for Metal Casting