Understanding Sand Casting Tolerances
Sand casting is a widely used manufacturing process that allows for the production of complex metal parts through the creation of molds from sand. This versatile technique has applications across various industries, from automotive to aerospace. One critical aspect of sand casting that impacts the quality and functionality of the produced components is the tolerances. Tolerances refer to the permissible limits of variation in physical dimensions and allow for the control of product quality. Understanding sand casting tolerances can significantly enhance both the production process and the final product's performance.
Definition of Tolerances
Tolerances in manufacturing are the permissible limits of variation in dimensions and other specified criteria. They play a crucial role in ensuring consistency and functional compatibility of parts that are manufactured. In sand casting, tolerances are particularly important since the process involves several variables, including mold materials, pouring temperatures, and cooling rates. The dimensional accuracy of a sand-cast part can be affected by these factors, making a clear understanding of tolerances essential for manufacturers.
Types of Tolerances in Sand Casting
The tolerances for sand casting can be classified into three main categories dimensional, geometric, and surface finish tolerances
.1. Dimensional Tolerances These refer to the allowable variations in the size of a part. In sand casting, dimensional tolerances are crucial because the casting process can often produce parts that are slightly larger or smaller than intended. The American Foundry Society (AFS) provides general guidelines for sand casting tolerances, often recommending a dimensional tolerance of ±0.5% for parts up to 100 mm. For larger components, this tolerance can increase, reflecting the challenges associated with larger molds and patterns.
sand casting tolerances
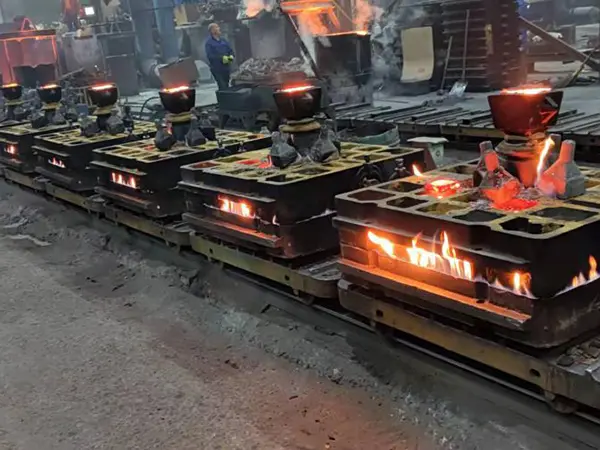
2. Geometric Tolerances These tolerances account for the shape of the part and include factors such as flatness, circularity, and position. Maintaining geometric tolerances is important, especially for parts that fit together, as poor geometric conformance can lead to assembly issues and malfunctions. Geometric tolerances often range from ±0.5 mm to ±2 mm, influenced by the complexity of the shape and the intended application of the part.
3. Surface Finish Tolerances The quality of the surface finish is vital for both aesthetics and function. A rough surface can lead to friction, wear, and corrosion, while a properly finished surface can enhance durability and reduce manufacturing costs in subsequent processes, like machining. Surface finish is typically measured in terms of Ra (roughness average), with sand casting finishes generally ranging from Ra 3.2 to Ra 12.5 micrometers, depending on the casting method and requirements.
Factors Affecting Tolerances
Several factors can influence the tolerances achieved in sand casting. These include
- Mold Material and Quality The type of sand and binding agents used can impact the precision of the mold, which, in turn, affects the dimensional accuracy of the final casting. - Pouring Technique The skill of the foundry worker and the method used to pour the molten metal into the mold can lead to variances in the size and shape of the casting. - Cooling Rate The speed at which the molten metal cools can lead to shrinkage or warping, thereby affecting tolerances.
Conclusion
In conclusion, understanding sand casting tolerances is essential for manufacturers aiming to produce high-quality, functional parts. By incorporating stringent tolerance specifications into their design and production processes, they can ensure a high level of assembly compatibility and performance for their products. An awareness of the types of tolerances, the factors that influence them, and the best practices in managing them can lead to improved efficiency and reduced costs across the production cycle. As industry demands evolve and technology advances, refining tolerance standards in sand casting will remain a key driver of competitiveness in manufacturing sectors.
Post time:נוב . 08, 2024 23:20
Next:Key Stages in the Sand Casting Process Explained