Sand Casting of Stainless Steel An Overview
Sand casting is a versatile and widely used manufacturing process that allows for the production of complex metal shapes. Stainless steel, known for its corrosion resistance, strength, and aesthetic appeal, has become a popular choice in various industries. Combining stainless steel with sand casting provides a robust and efficient method for creating intricate designs and components. This article explores the advantages of sand casting stainless steel and its applications, processes, and challenges.
What is Sand Casting?
Sand casting is a process whereby a mold is made from a mixture of sand and a binding agent, into which molten metal is poured. Once the metal cools and solidifies, the mold is broken apart to retrieve the finished product. This method is particularly well-suited for producing large and complex parts, making it an ideal choice for industries ranging from automotive to aerospace, and even art.
Advantages of Sand Casting Stainless Steel
1. Complex Geometries Sand casting can accommodate intricate shapes and detailed designs that are often challenging to achieve with other manufacturing processes. This capability is particularly valuable in industries where precision and innovation are critical.
2. Cost-Effectiveness Compared to other casting methods, sand casting is generally more cost-effective for low to moderate production volumes. The molds can be created relatively quickly, and the materials used (sand and binding agents) are generally inexpensive.
3. Material Versatility Sand casting can be applied to various alloys, including different grades of stainless steel. The versatility of the process allows manufacturers to choose specific stainless steel grades based on the required properties of the final product, such as strength, corrosion resistance, and temperature tolerance.
4. Mechanical Properties Items produced through sand casting typically exhibit excellent mechanical properties. The cooling process in sand casting allows for controlled solidification, resulting in good microstructures and internal integrity.
The Sand Casting Process
The process of sand casting stainless steel involves several critical steps
1. Pattern Creation A pattern of the item to be cast is created, typically from wood or metal. This pattern is used to form the sand mold.
sand casting stainless steel
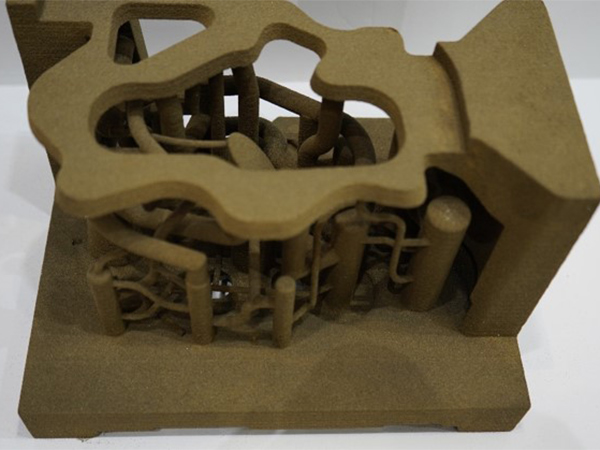
2. Mold Preparation The mold consists of two parts (the cope and the drag), formed by compacting sand around the pattern. The pattern is removed once the sand has set, leaving a cavity that matches the shape of the desired product.
3. Pouring Molten stainless steel, heated to temperatures around 1400 to 1600 degrees Celsius, is poured into the mold cavity. The quality of the pour is crucial, as it affects the final properties of the cast metal.
4. Cooling After pouring, the molten steel is allowed to cool and solidify within the mold. Cooling times can vary based on the size and complexity of the cast.
5. Finishing Once cooled, the mold is broken away to reveal the cast component. Post-processing steps, including grinding, machining, and surface finishing, are often required to achieve the desired surface quality and dimensions.
Challenges in Sand Casting Stainless Steel
Despite its many advantages, sand casting stainless steel does present certain challenges
1. Surface Finish Achieving a smooth surface finish can be difficult in sand casting, often requiring additional machining or finishing processes to meet stringent specifications.
2. Dimensional Accuracy While sand casting can produce complex shapes, maintaining tight tolerances can be challenging. Some applications may necessitate additional machining to achieve precise dimensions.
3. Defects Common casting defects like porosity, shrinkage, and inclusion can occur, which may compromise the integrity of the finished product. Careful control of the melting and pouring processes is necessary to mitigate these issues.
Conclusion
Sand casting stainless steel stands out as an effective manufacturing process that marries flexibility with material performance. Its ability to produce complex geometries economically makes it an enduring choice for various industrial applications. While challenges exist, advancements in technology and techniques continue to enhance the capabilities of sand casting, ensuring its vital role in the future of manufacturing. As industries seek innovative solutions, sand casting stainless steel is poised to remain a key player, offering strength, durability, and versatility.
Post time:אוק . 12, 2024 10:07
Next:Understanding Gold Sand and Its Significance in Nature and Mining