The Art and Science of Sand Casting Processes
Sand casting, also known as sand mold casting, is one of the oldest and most widely used manufacturing processes in the metalworking industry. This method leverages the natural properties of sand to create molds for metal casting, combining both artistry and engineering. With a rich history that dates back thousands of years, sand casting remains a popular choice for producing a diverse range of metal components, from intricate small parts to large industrial machinery.
Process Overview
The sand casting process begins with the creation of a mold. The primary material used for this mold is sand, often combined with a binder to help the grains stick together. The most common type of sand used is silica sand, which provides the necessary thermal resistance required during the casting process.
1. Mold Design and Creation The first step involves designing the part to be cast. This includes creating a pattern, usually made from wood, metal, or plastic, which serves as a replica of the intended product. Once the pattern is made, it is pressed or packed into fine sand mixed with a binding agent to form a two-part mold—a cope and a drag. The cope is the upper part of the mold, while the drag is the lower part.
2. Pattern Removal After the sand is packed tightly around the pattern, the two mold halves are carefully separated to remove the pattern. This leaves a hollow cavity in which the metal will be poured.
3. Pouring the Metal Once the mold is ready, molten metal is poured into the cavity. Bronze, aluminum, cast iron, and steel are commonly used metals, depending on the desired properties of the finished product. The metal typically retains the same shape as the pattern in the mold.
4. Cooling and Solidification After pouring, the metal cools and solidifies within the mold. This cooling phase can vary in time depending on several factors, including the thickness of the casting and the type of metal used.
5. Mold Removal and Finishing Once the metal has completely cooled, the mold is broken apart, and the sand is removed. The casting is then subjected to various finishing processes, such as grinding, machining, or polishing, to achieve the desired dimensions and surface finish.
Advantages of Sand Casting
sand casting processes
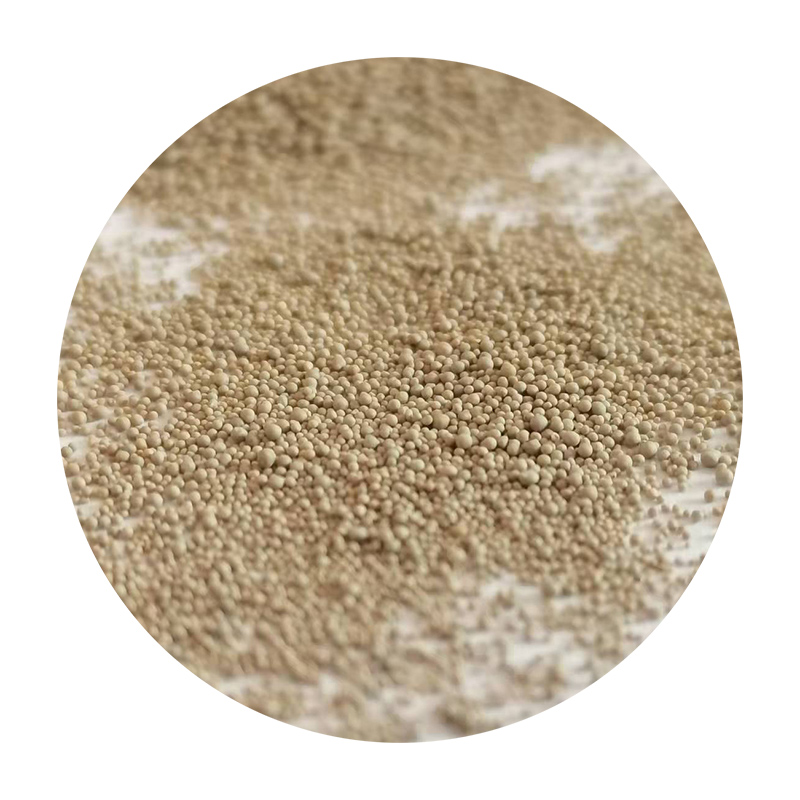
Sand casting offers several benefits that make it a preferred method for many manufacturers
- Versatility One of the biggest advantages of sand casting is its versatility. It can accommodate a wide variety of shapes and sizes, making it suitable for both simple and complex designs.
- Cost-Effectiveness The materials used in sand casting are relatively inexpensive. Furthermore, because the process can be easily scaled, it is economically viable for both low and high production volumes.
- High Tolerance The process can achieve good dimensional accuracy and surface finish compared to other casting methods. Although further machining might be required, sand casting can produce parts that are close to final dimensions.
- Reusability of Sand The sand used in the casting process can often be reused for multiple cycles, reducing material waste and costs.
Applications of Sand Casting
Sand casting is utilized in a vast array of industries. It is heavily employed in automotive manufacturing for engine blocks, transmission cases, and various other components. Additionally, it is prevalent in the aerospace sector for producing turbine blades and structural components.
Other applications extend to the construction industry, where sand casting is used to create architectural features and structural parts. The versatility and cost-effectiveness of sand casting also make it attractive for artistic endeavors, including sculptures and fine jewelry.
Conclusion
In conclusion, sand casting is a timeless technique that seamlessly marries art with engineering. Its long-standing presence in the manufacturing landscape is a testament to its effectiveness and adaptability. As industries evolve and modern technologies surface, the fundamental principles of sand casting remain integral, continuing to provide solutions for producing high-quality metal parts. With growing demands for customization and innovation, the future of sand casting is poised to adapt and thrive, ensuring its place in the manufacturing processes of tomorrow.
Post time:נוב . 05, 2024 21:55
Next:advantages and disadvantages of sand casting