The Sand Casting Process An Overview
Sand casting is one of the oldest and most versatile foundry processes in metalworking, widely used to create complex shapes and components in various industries. This method involves a series of steps, from pattern creation to the final casting, resulting in high-quality metal products.
The first step in the sand casting process is the preparation of the mold. A pattern, typically made from wood, metal, or plastic, is designed to match the desired end product. This pattern is then placed into a mixture of sand and a binding agent, often clay, forming the mold. The sand is compacted around the pattern to create a negative impression. This allows for intricate designs and details to be captured in the mold.
Once the mold is prepared, the next critical step is the pouring of molten metal. The metal, which can be aluminum, iron, or other alloys, is heated to a temperature that allows it to become liquid. It is then poured into the cavity of the mold, filling the negative space created by the pattern. This phase of the process requires precision and care, as any impurities or irregular temperatures can lead to defects in the final product.
sand casting process
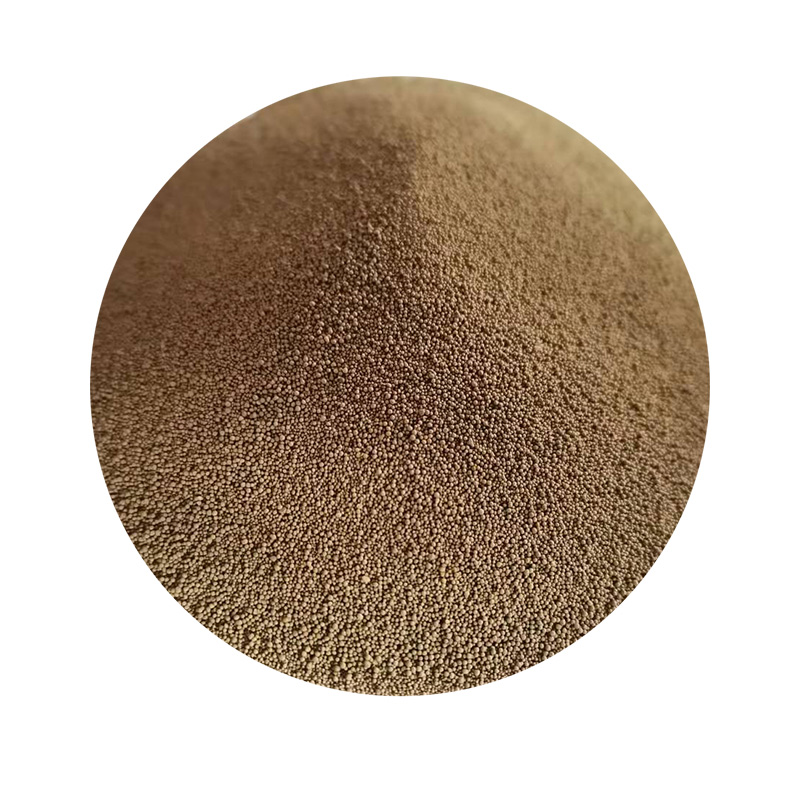
After the metal has cooled and solidified, the next step is to break open the mold and remove the casting. This can be done either by hand or with specialized machinery, depending on the size and complexity of the casting. Once removed, the casting often requires additional processes such as cleaning, machining, or finishing to achieve the desired surface quality and dimensional accuracy.
There are several advantages to using sand casting as a manufacturing technique. First and foremost, it is cost-effective, particularly for producing small to medium-sized production runs. The materials used for the molds are relatively inexpensive, and the flexibility of the process allows for rapid modifications to patterns as needed. Additionally, sand casting can accommodate very large components that other casting methods may struggle with.
However, sand casting does have its drawbacks. The surface finish of sand castings is generally poorer compared to other casting methods, such as investment casting. Furthermore, the dimensional accuracy may not be as high, necessitating additional machining processes for precision applications. Despite these limitations, sand casting remains a popular choice due to its adaptability and low costs.
In conclusion, the sand casting process is a time-tested method that plays a crucial role in modern manufacturing. Its ability to produce complex shapes with relative ease makes it ideal for a variety of applications across different industries. As technology advances, new materials and techniques continue to enhance the efficiency and effectiveness of sand casting, ensuring its place in the future of metalworking.
Post time:אוק . 30, 2024 14:16
Next:golden sands