Sand casting is a fundamental and widely used manufacturing process that has been around for centuries. It involves pouring molten metal into a sand mold to create complex and durable components for various industries. The versatility and cost-effectiveness of sand casting have made it an indispensable technique in the production of metal parts for everything from automotive components to artistic sculptures.
One of the primary reasons for the popularity of sand casting is its ability to produce intricate shapes that would be challenging or impossible to achieve with other methods. The sand mold can be easily shaped and altered, allowing for the creation of detailed patterns. This flexibility makes sand casting ideal for industries that require customized parts, such as aerospace, machinery, and even consumer goods.
.
After the metal solidifies, the sand mold is broken away to reveal the finished product. This process can be repeated multiple times, allowing manufacturers to produce both individual parts and large quantities efficiently. Moreover, the sand used in this process can often be reclaimed and reused, minimizing waste and reducing costs.
sand cast industries
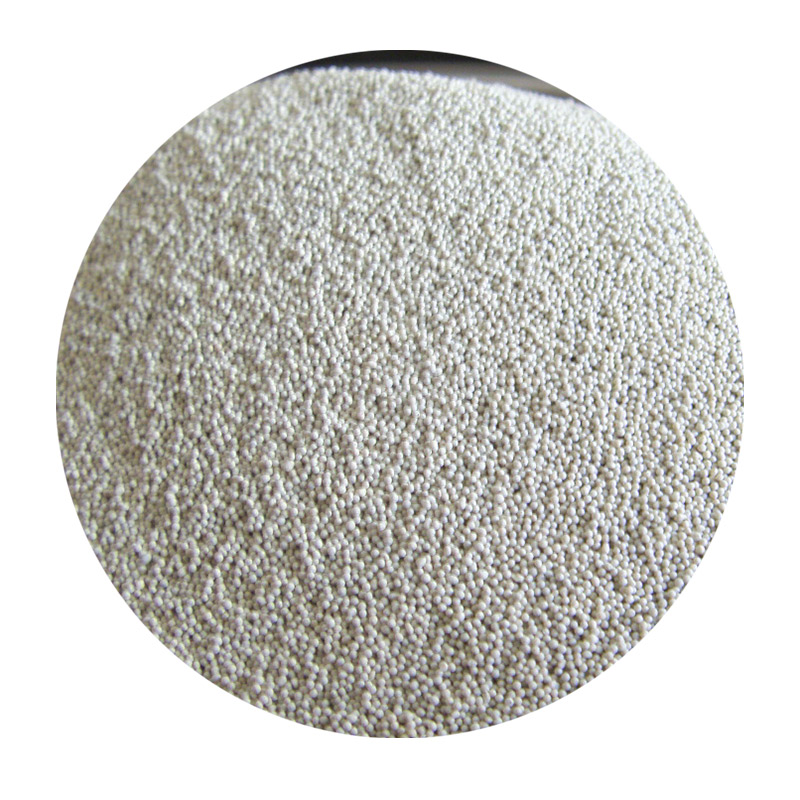
Another advantage of sand casting is its compatibility with various metals, including aluminum, copper, and iron. This versatility enables manufacturers to select materials that best suit their application requirements. For example, aluminum castings are commonly used in the automotive industry for lightweight yet strong components, whereas iron castings are prevalent in machinery and construction applications.
Despite its many benefits, sand casting is not without its challenges. The quality of the final product can be affected by factors such as the quality of the sand, the precision of the mold, and the pouring technique. Defects such as sand inclusions, porosity, and dimensional inaccuracies can occur if these aspects are not carefully controlled. Therefore, continuous advancements in technology and quality control measures have become critical in enhancing the reliability of sand casting.
In recent years, innovations like computer-aided design (CAD) and 3D printing have started to revolutionize the sand casting industry. CAD software allows for more precise mold designs, while 3D printing technology enables the rapid prototyping of molds, significantly reducing lead times. This convergence of traditional techniques with modern technology is not only improving product quality but also expanding the possibilities of what can be manufactured through sand casting.
In conclusion, sand casting remains a cornerstone manufacturing method that combines ancient techniques with modern advancements. Its adaptability, efficiency, and ability to produce complex parts make it a favored choice across various industries. As technology continues to evolve, the sand casting industry is poised for further growth and innovation, ensuring its relevance in the ever-changing landscape of manufacturing.
Post time:אוק . 06, 2024 08:18
Next:hydro super sand