The Advantages and Applications of Resin Sand in Modern Casting
Resin sand, commonly referred to as phenolic resin sand or simply resinsand, has emerged as a revolutionary material in the foundry industry, particularly in casting operations. Unlike traditional sand molds, resin sand combines sand grains with a resin binder, providing superior properties that cater to the demanding requirements of modern manufacturing. This article aims to explore the advantages of resin sand, its applications, and its growing significance in the foundry landscape.
Enhanced Mold Strength and Stability
One of the standout features of resin sand is its remarkable strength and stability. The addition of phenolic resin significantly enhances the mechanical properties of the sand, allowing for the production of molds that can withstand higher temperatures and pressure during the casting process. This increased strength minimizes the risk of sand mold breakage, which is a common issue faced with traditional sand molds. The ability to maintain structural integrity is critical, especially when dealing with complex geometries and high-precision components.
Superior Surface Finish
The surface finish of cast products is a crucial factor that affects their aesthetic appeal and functional performance. Resin sand molds typically yield a smoother surface compared to those made from traditional green sand. This is particularly advantageous for industries that require high-quality finishes, such as automotive, aerospace, and artistic castings. The fine surface texture not only reduces the need for extensive post-casting machining but also enhances the overall quality of the final product.
Improved Casting Precision
Precision is paramount in casting operations, especially with the rise of advanced manufacturing techniques. The thermal properties and dimensional stability of resin sand allow for greater accuracy in the casting process. When manufacturers aim to produce parts with tight tolerances, resin sand provides a reliable solution, reducing the likelihood of defects and dimensional discrepancies. This precision is vital for high-performance applications where even minor errors can lead to significant costs and safety concerns.
resin sand
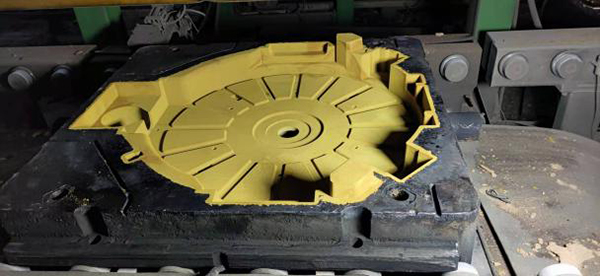
Reduced Environmental Impact
Sustainability is a rising concern across industries, and the foundry sector is no exception. Traditional sand casting processes can generate significant waste and pollution, while the use of resin sand offers a more environmentally friendly approach. Many suppliers are now offering reclaimed resin sand solutions, allowing for the recycling of materials from previous projects. Additionally, the inherent efficiency of resin sand casting reduces the overall energy consumption during the molding and curing processes, further diminishing the environmental footprint.
Versatile Applications
The versatility of resin sand extends beyond mere aesthetic and structural benefits. Industries ranging from automotive and aerospace to art and sculpture are increasingly incorporating resin sand into their casting operations. For example, in the automotive sector, resin sand is ideal for producing complex engine components that require both precision and durability. In artistic applications, sculptors benefit from the detailed finishes achievable with resin sand molds, allowing for intricate designs that were previously challenging to produce.
Challenges and Future Directions
Despite its many advantages, the adoption of resin sand is not without challenges. The initial cost of resin sand systems can be higher than traditional methods, and the need for specialized equipment and training may deter some foundries. However, as the technology matures and more foundries recognize the long-term benefits, it is expected that resin sand will gain further traction.
In conclusion, resin sand represents a significant advancement in casting technology, offering numerous benefits that cater to the demands of modern manufacturing. With enhanced mold strength, superior surface finishes, improved precision, reduced environmental impact, and versatile applications, resin sand is poised to play a pivotal role in the future of the foundry industry. As manufacturers continue to seek innovative solutions to meet the challenges of contemporary production, resin sand will undoubtedly be at the forefront of those efforts.
Post time:נוב . 08, 2024 12:04
Next:Top Manufacturers of Resin Coated Sand for Industrial Applications