Understanding the Metal Sand Casting Process
Metal sand casting is a widely used manufacturing process that involves pouring molten metal into a mold made of sand to create intricate and detailed parts. This method has been employed for centuries and remains a cornerstone technique in various industries, including automotive, aerospace, and artistic metalworking. This article will delve into the metal sand casting process, its advantages, applications, and factors influencing its effectiveness.
The Casting Process
The sand casting process begins with the creation of a mold. The mold is typically made from a mixture of sand and a bonding agent, such as clay or resin. The specific type of sand used can greatly affect the quality of the final product. When the sand is compacted around a pattern—an exact replica of the final product—the pattern is then removed, leaving a cavity that mirrors its shape.
The next step involves melting the chosen metal, which can vary depending on the application, such as aluminum, iron, or bronze. The molten metal is then poured into the cavity of the sand mold. After allowing sufficient time for the metal to cool and solidify, the mold is broken apart, revealing the cast metal part. Following this, any excess material—commonly referred to as flash—is trimmed away, and the surface is finished as necessary.
Advantages of Metal Sand Casting
One of the primary advantages of metal sand casting is its versatility. The process can accommodate a wide range of metal alloys, making it suitable for producing everything from small components to large, complex structures. It is also capable of creating intricate shapes with excellent surface finish and dimensional accuracy.
Another benefit is the relatively low cost of molds and tooling. Unlike more advanced techniques, such as die casting, sand molds can be created without the need for expensive machinery. This affordability renders sand casting an attractive option for both small-scale production and large-scale casting operations.
Furthermore, sand casting allows for the reuse of sand, making it an environmentally friendly choice. After the metal is cast, the sand can be cleaned and recycled for future molds, minimizing waste and reducing material costs.
metal sand casting process
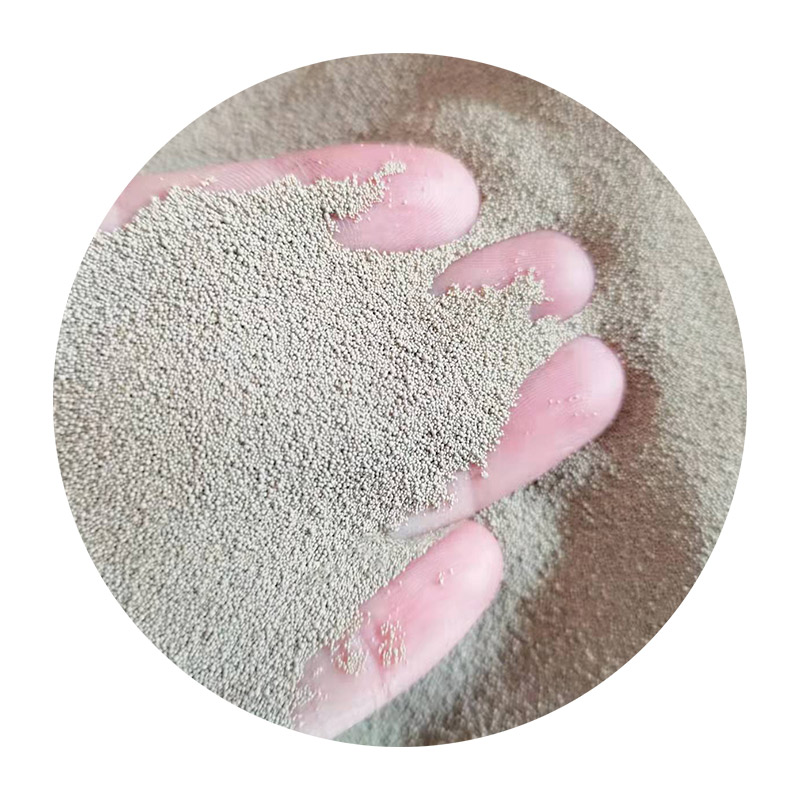
Applications of Metal Sand Casting
Due to its adaptability, metal sand casting is utilized across a vast spectrum of applications. In the automotive industry, for example, components such as engine blocks, transmission cases, and various structural parts are often produced using this method. In aerospace, sand casting is employed for creating intricate parts that meet strict safety standards and weight requirements.
Artisan metalworkers also appreciate the sand casting process for producing decorative art pieces and jewelry. The method allows for a high degree of creativity and customization, which is often essential in artistic endeavors. Beyond these industries, sand casting finds use in manufacturing machinery parts, pumps, valves, and even historical replicas.
Factors Influencing the Effectiveness of Sand Casting
While metal sand casting offers numerous benefits, several factors can influence the success of the process. The quality of the sand used is paramount; it must possess the correct balance of strength, permeability, and cohesiveness to withstand the pouring of molten metal without collapsing or allowing air to escape.
The skill and experience of the foundry workers also play a critical role. From mold preparation to pouring and finishing touches, every step requires precision and expertise to achieve the desired results. Finally, the design of the casting, including the incorporation of proper draft angles and details for ease of mold release, can significantly affect the quality and accuracy of the final product.
Conclusion
Metal sand casting remains a fundamental technique in manufacturing, offering flexibility, cost-effectiveness, and a wide range of applications. As industries continue to evolve and innovate, the sand casting process is likely to adapt, further integrating new technologies and methods to enhance its efficiency and product quality. Understanding this age-old technique is crucial for anyone involved in manufacturing or engineering, as it underscores the balance between tradition and modernity in the world of production.
Post time:נוב . 04, 2024 19:06
Next:steps in sand casting