Lost Foam Metal Casting An Innovative Approach to Metal Fabrication
Lost foam metal casting is an advanced manufacturing process that has gained considerable attention in recent years due to its ability to produce complex shapes with high precision and minimal material waste. This method, which originated in the early 1970s, combines the techniques of traditional metal casting with modern materials to create intricate components for various industries, including automotive, aerospace, and art. The following explores the principles, advantages, applications, and future of lost foam metal casting.
At the core of lost foam casting is the use of a foam pattern—typically made from expanded polystyrene (EPS) or similar materials. The process begins by creating a foam model of the part that needs to be manufactured. This foam model is then coated with a refractory material to form a durable shell. Once the shell is created, the coated foam pattern is placed in a mold and the molten metal is poured over it. As the metal fills the mold, the extreme heat causes the foam to vaporize and dissipate, leaving behind a cavity that corresponds precisely to the intended shape of the final product. This unique feature allows for the production of complex geometries that are often difficult to achieve with traditional casting methods.
One of the most significant advantages of lost foam metal casting is its capacity to minimize material wastage. Conventional casting processes typically require significant machining to achieve the desired final dimensions; however, because the foam pattern can be made to near-net shape, the need for extensive secondary operations is greatly reduced. This not only conserves materials but also cuts down on production time and costs, making it an economically viable option for manufacturers.
Additionally, this casting method excels in producing lightweight components. As industries increasingly focus on enhancing energy efficiency and reducing emissions, the ability to create lightweight but strong parts using lost foam technology is particularly appealing. For example, automotive manufacturers can produce intricate engine components that are lighter than those made via traditional methods, leading to improved fuel efficiency without sacrificing performance.
lost foam metal casting
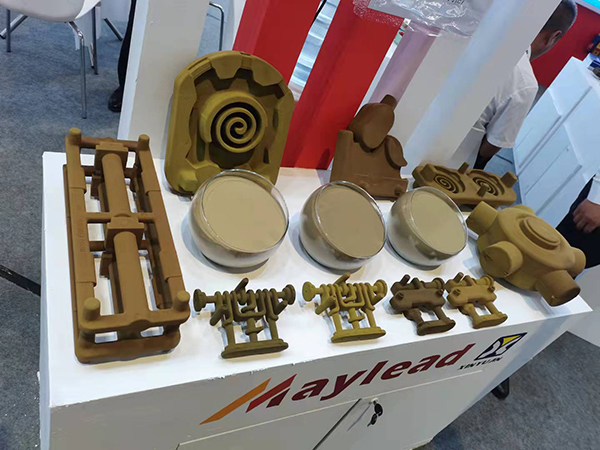
The versatility of lost foam metal casting also extends to its compatibility with various metals, including aluminum, iron, and nickel-based alloys
. This adaptability allows it to cater to the specific material requirements of different applications, providing manufacturers with greater flexibility in terms of production choices.The applications of lost foam metal casting are vast and varied. In the automotive industry, it is commonly used for manufacturing engine blocks, transmission cases, and other critical components. Aerospace manufacturers utilize this technique for fabricating lightweight structural components and thermal management parts, which are essential in high-performance aircraft. Furthermore, artists and sculptors have embraced lost foam casting for creating intricate metal artworks that showcase fine details, previously unattainable through traditional fabricating methods.
Despite its advantages, lost foam metal casting does face some challenges. The accuracy of the final product heavily relies on the quality of the foam pattern and the controlling parameters during the casting process, such as pouring temperature and speed. Any inconsistencies can lead to defects in the final piece. Additionally, the initial investment in equipment and the processing of foam materials can be relatively high, which may deter smaller companies from adopting this technique.
Looking to the future, the integration of advanced technologies such as additive manufacturing (3D printing) with lost foam metal casting presents exciting possibilities. By using 3D printing to create foam patterns, manufacturers can take advantage of advanced design capabilities and rapid prototyping, further enhancing the efficiency and effectiveness of the lost foam process. Research and development are ongoing to refine these techniques, which could establish lost foam metal casting as a dominant method in metal manufacturing.
In conclusion, lost foam metal casting is a revolutionary approach to metal fabrication that aligns with modern manufacturing needs for efficiency, precision, and sustainability. As industries continue to evolve and demand more complex and lightweight components, this innovative casting method will play an increasingly important role in meeting those challenges. With ongoing advancements and integration with new technologies, the future looks bright for lost foam metal casting, making it an invaluable asset in the world of manufacturing.
Post time:נוב . 20, 2024 04:52
Next:zand in hars gebruiken