Lost Foam Casting Manufacturers An Innovative Approach to Precision Casting
Lost foam casting (LFC) has emerged as an innovative technique in the field of manufacturing, offering a unique solution for producing complex metal components with high precision and minimal waste. This method, which involves creating a foam pattern that is coated with a layer of refractory material, has gained considerable attention among manufacturers looking to enhance efficiency and reduce costs.
One of the primary advantages of lost foam casting is its ability to produce intricate shapes that would be challenging or impossible to achieve with traditional casting methods. By using foam patterns, manufacturers can create complex geometries without the need for elaborate tooling. This flexibility not only speeds up production times but also allows for greater design freedom. As industries increasingly demand customized and complex parts, LFC manufacturers are well-positioned to meet these needs.
The process of lost foam casting begins with the creation of a foam pattern, typically made from polystyrene or similar materials. This pattern is coated in a fine layer of sand mixed with a binding agent, which helps retain the shape during the casting process. Once the mold is prepared, liquid metal is poured over the foam pattern. As the metal fills the mold, it causes the foam to vaporize, creating a precise cavity for the metal to take shape. This elimination of the foam results in minimal clean-up and post-processing, streamlining the overall manufacturing process.
lost foam casting manufacturers
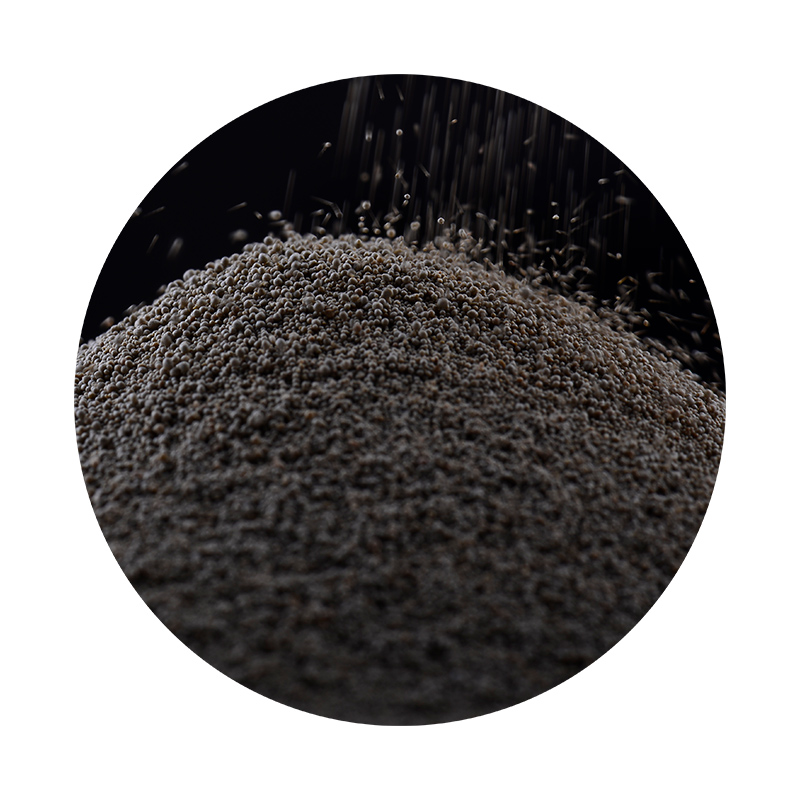
Lost foam casting is particularly beneficial in industries such as automotive, aerospace, and heavy machinery, where the need for lightweight yet durable components is critical. Manufacturers are increasingly turning to LFC to produce engine components, structural parts, and other intricate items that require high performance. By leveraging this technology, companies can also achieve significant cost savings due to reduced material waste and shorter lead times.
Furthermore, lost foam casting manufacturers are embracing advancements in technology and automation to enhance their production capabilities
. The integration of computer-aided design (CAD) software and automated systems allows for more precise pattern creation and mold-making processes, improving overall quality and consistency in the final products.As environmental concerns grow, the lost foam casting process is also recognized for its sustainability benefits. The method generates less excess material compared to traditional casting practices, contributing to a smaller carbon footprint. Manufacturers committed to sustainable practices find LFC an attractive option in their pursuit of greener production methods.
In conclusion, lost foam casting manufacturers are at the forefront of a transformative trend in manufacturing. With its ability to produce complex, high-quality components efficiently and sustainably, LFC positions itself as a vital process in various industries. As technology continues to evolve, so too will the capabilities and offerings of lost foam casting manufacturers, paving the way for future innovations in precision casting.
Post time:נוב . 20, 2024 16:08
Next:fill 3d print with sand