Understanding Foundry Sand Types Their Roles and Significance
Foundry sand is a crucial component in the metal casting industry, playing a pivotal role in the production of high-quality castings. With various types available, each suited for specific applications, understanding the distinctions and characteristics of foundry sand types is essential for optimizing casting processes. In this article, we will explore the different types of foundry sand, their properties, applications, and the importance of selecting the appropriate type for various foundry operations.
1. Silica Sand
Silica sand, often referred to as quartz sand, is the most commonly used type of foundry sand. It consists primarily of silicon dioxide (SiO2) and features excellent thermal properties, making it ideal for casting applications. The grain shape, size, and distribution are critical factors influencing the final casting quality. Silica sand is utilized in metal molding processes and other types of casting due to its ability to withstand high temperatures and its low thermal expansion. However, it can also create environmental and health concerns due to the risk of silica dust exposure, necessitating safety precautions during handling and use.
2. Silica Flour
Silica flour is finely milled silica sand, characterized by its smaller particle size. It is used to enhance the strength of molds and cores and helps to improve the surface finish of castings. Silica flour provides a high degree of permeability which allows gases to escape during the metal pouring process, reducing the likelihood of casting defects. It is particularly useful in applications demanding precise tolerances and superior surface finishes, although the handling of silica flour must be done with care due to similar health risks as regular silica sand.
Resin-coated sand has gained popularity in the foundry sector due to its superior binding properties. This type of sand consists of a base sand coated with a synthetic resin, which, when heated, hardens and binds the sand grains together. This type is particularly useful in production applications where high strength and dimensional accuracy are required. The key advantage of resin-coated sand is its ability to produce complex geometries and thinner sections in castings, enabling foundries to achieve intricate designs with smoother surface finishes.
foundry sand types
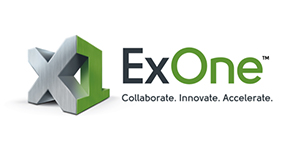
4. Clay-Based Sand
Clay-based sand, composed of a mix of sand and clay, such as bentonite, is another essential foundry sand type. The clay content provides excellent bonding properties, allowing the sand to maintain its shape when wet. This type is mainly used in green sand molding processes, a traditional method where moist sand molds are created. Green sand systems are valued for their cost-effectiveness, ease of use, and the ability to produce high-quality castings. However, the performance of clay-based sand is strongly influenced by the properties of the clay used, requiring careful management of materials.
5. Ceramic Sand
Ceramic sand is utilized primarily for the production of precision castings in high-performance industries, including aerospace and automotive applications. This sand is heat-resistant and highly durable, making it an excellent choice for investment casting processes. Its spherical shape improves flowability and allows for better packing density, leading to enhanced mold strength and dimensional accuracy. While more expensive than traditional sands, the performance benefits often justify the cost when precision and quality are paramount.
6. Other Specialized Sands
In addition to the major types mentioned above, various other specialized sands are used in niche applications within the foundry industry. For example, zircon sand, with its high thermal stability and low thermal expansion, is employed for specific casting scenarios requiring enhanced performance. Similarly, olivine sand offers excellent refractory characteristics and is utilized in particular casting environments.
Conclusion
Understanding the different types of foundry sand and their unique properties is essential for any foundry operation. The choice of sand can significantly influence the quality, performance, and efficiency of the casting process. By selecting the right type of foundry sand—silica, resin-coated, clay-based, ceramic, or specialized options—foundries can optimize their operations, reduce defects, and produce high-quality castings that meet industry standards. As the industry evolves, ongoing innovations in foundry sand technology will likely lead to even better materials and processes, further enhancing the capabilities of modern foundries.
Post time:נוב . 24, 2024 10:12
Next:bauxite frac sand