Sand Casting of Cast Iron An Overview
Sand casting is one of the oldest and most versatile metal-forming processes, playing a crucial role in the manufacturing of cast iron components. This method offers a combination of affordability, flexibility, and durability, making it suitable for a wide range of applications, from automotive parts to industrial machinery.
The Basics of Sand Casting
At its core, sand casting involves creating a mold out of sand, which is then filled with molten metal to form the desired shape. The casting process begins with the preparation of the sand mold. A pattern or model of the object to be cast is made, usually from a material such as wood or metal, and coated with a release agent to prevent the cast from sticking to the mold.
The mold itself is fashioned by mixing fine sand with a binder, typically clay or resin, to enhance strength and cohesion. The two mold halves are formed around the pattern, which is then removed to leave a cavity shaped like the desired part. The two halves are then fitted together, and the molten cast iron is poured into the cavity through a gating system, where it solidifies as it cools.
Properties of Cast Iron
Cast iron is a group of iron-carbon alloys with a carbon content greater than 2%. It is renowned for its excellent castability, good machinability, and impressive wear resistance. There are various types of cast iron, including gray iron, ductile iron, and white iron, each having distinct characteristics suitable for different applications.
Gray iron is the most commonly used type, noted for its good fluidity and machinability. It has excellent wear resistance, making it ideal for engine blocks, cylinders, and other high-wear components. Ductile iron, on the other hand, has enhanced ductility and impact resistance, making it a preferred choice for critical applications where strength and toughness are paramount.
Advantages of Sand Casting Cast Iron
sand casting cast iron
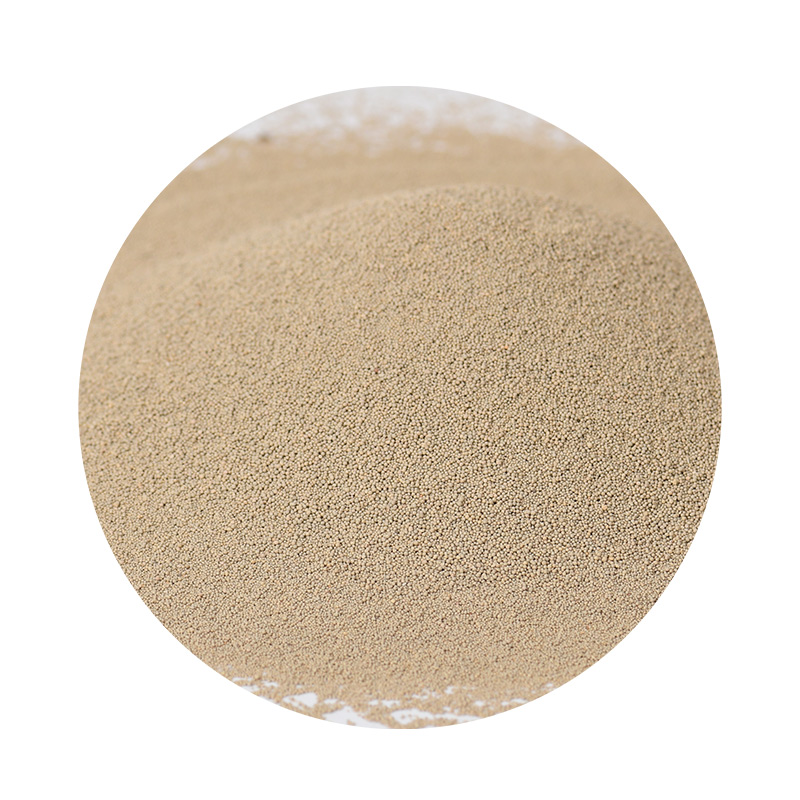
1. Cost-Effectiveness Sand casting is economical, especially for low to medium production runs. The raw materials—silica sand, clay, and metal—are relatively cheap, allowing manufacturers to produce components without incurring exorbitant costs.
2. Design Flexibility This casting method accommodates a wide variety of part sizes and complexities. Complex shapes can be achieved without the need for extensive tooling modifications, making it easier to iterate designs.
3. Scalability Sand casting is suitable for both small and large production volumes. As demand fluctuates, manufacturers can easily scale production up or down without significant capital investment.
4. Material Variety While cast iron is the primary material used, sand casting is compatible with many other metals and alloys, allowing for a diverse range of applications beyond iron.
Challenges and Considerations
Despite its advantages, sand casting also presents some challenges. The quality of the mold plays a significant role in determining the final product's surface finish and dimensional accuracy. Additionally, moisture content in the sand can affect the casting process and lead to defects such as porosity or sand inclusion.
To mitigate these issues, manufacturers often employ quality control measures and advanced molding techniques, such as the use of resin-coated sand or 3D printing for intricate molds. Innovations in mold design can greatly improve the overall efficiency and success rate of the casting process.
Conclusion
In summary, sand casting of cast iron remains a widely used method for producing a variety of parts, combining cost-effectiveness with design flexibility. While it faces challenges associated with mold quality and precision, ongoing advancements in technology and materials continue to enhance its viability. As industries evolve and demand for durable yet affordable components rises, sand casting will undoubtedly retain its importance in the metalworking landscape. Whether for heavy machinery or intricate components, the sand casting process is a testament to the enduring legacy of traditional manufacturing methods in modern production.
Post time:Nov . 07, 2024 13:12
Next:Exploring the Benefits and Applications of Sand and Resin Composites