Understanding Materials Used in Sand Casting
Sand casting is one of the oldest and most versatile metal casting processes used in manufacturing. It involves pouring molten metal into a mold made from sand and a binding agent, allowing manufacturers to produce intricate shapes and components with relative ease. The key to successful sand casting lies in the chosen materials, which play critical roles in shaping and enhancing the casting's quality. In this article, we'll explore the materials typically used in sand casting, their properties, and their contributions to the overall casting process.
1. Sand
The primary material in sand casting is, of course, sand. The most commonly used sand is silica sand, which is abundant, cost-effective, and has high melting points. Silica sand grains are spherical, allowing for better flow and compaction, which results in a smoother surface finish for the cast product. Other types of sand, such as olivine and zircon sand, have also gained popularity in specific applications due to their superior thermal properties and lower thermal expansion, which helps to minimize defects in the casting.
2. Binders
To create strong molds, a binder is added to the sand. Common binders used in sand casting include clay and synthetic resins. Clay, particularly sodium bentonite, is widely used for its ability to bond sand grains together when water is added. This creates a strong and cohesive mold that can withstand the weight and temperature of molten metal. In contrast, synthetic resins, such as phenolic resin or furan resin, offer superior durability and a more controlled cure time compared to clay. The choice of binder can significantly impact the strength and permeability of the mold, ultimately influencing the quality of the final casting.
3. Moisture
what materials are used in sand casting
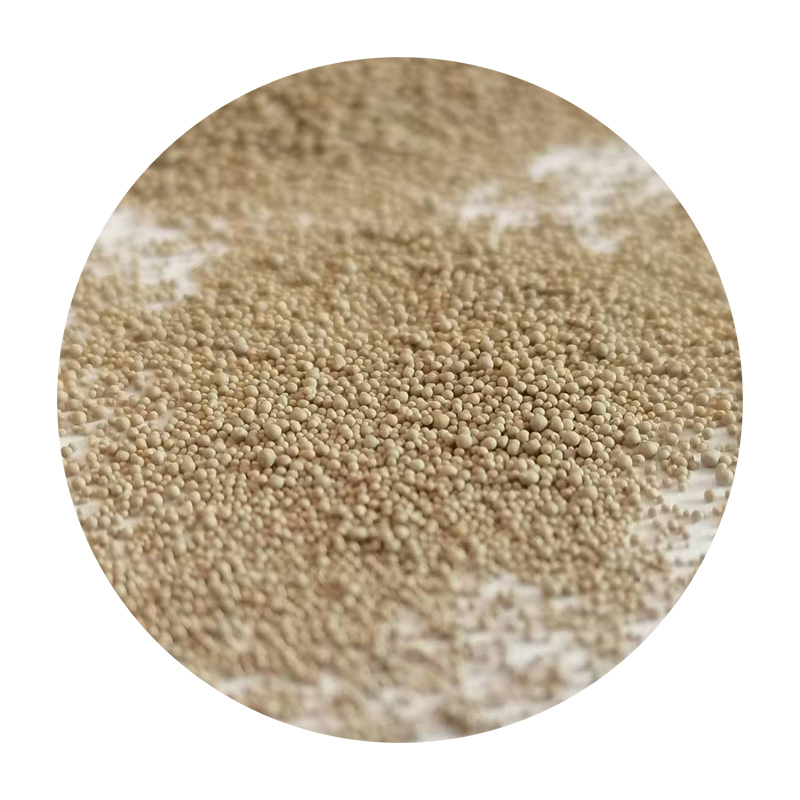
Water is another crucial ingredient in sand casting. It is added to the sand-binder mixture to activate the bonding properties of the binder, creating a cohesive mold that can hold its shape during casting. The moisture content must be carefully controlled; too little moisture can result in a brittle mold that fractures under the weight of the molten metal, while too much can lead to steam generation, resulting in defects. Typically, a moisture content of around 2-4% is ideal for creating stable and accurate molds.
4. Additives
To enhance specific properties of the sand mixture, various additives may be included. These additives can improve the mold's strength, thermal stability, and surface finish. For instance, coal dust or other carbonaceous materials can be added to minimize oxidation of the metal during casting, while various types of pigments can be used to improve the visual appearance of the molds. Additionally, materials such as calcium sulfate or starch can be used to modify the flow characteristics of the sand mixture, making it easier to fill complex mold designs.
5. Metal Alloys
While of secondary importance in terms of mold materials, the type of metal used for casting is equally vital. Common metals used in sand casting include iron, aluminum, brass, and bronze. Each alloy has unique properties that suit different applications. For example, iron boasts excellent wear resistance, making it suitable for industrial applications, while aluminum is lightweight and offers good corrosion resistance, making it ideal for automotive parts. The choice of metal also interacts with the properties of the sand and binder, influencing the overall casting quality.
Conclusion
In summary, the success of sand casting heavily relies on the materials used in the process. From the fundamental sand type to binders and moisture content, each material plays a crucial role in determining the quality and precision of the final product. By understanding and selecting the appropriate materials, manufacturers can optimize the sand casting process for specific applications, resulting in high-quality components that meet industry standards. As technology advances, the exploration of new materials and methods continues to enhance the capabilities of sand casting, ensuring its relevance in modern manufacturing.
Post time:ઓક્ટોબર . 02, 2024 00:18
Next:Techniques for Sanding and Finishing 3D Printed Models for a Smooth Surface