Types of Sand Casting An Overview
Sand casting, also known as sand mold casting, is one of the oldest and most widely used metal casting processes. It involves creating a mold from sand, into which molten metal is poured to create a particular part or product. The versatility and ease of the sand casting process make it highly popular across various industries, including automotive, aerospace, and artistic applications. This article will explore the primary types of sand casting used in the industry today.
1. Green Sand Casting
Green sand casting is the most common type of sand casting. The term green refers to the moisture content of the sand mixture, which typically includes sand, clay, and water. This mixture has excellent shape retention properties and is relatively inexpensive, making it ideal for high-volume production.
Green sand molds are formed by compacting the mixture around a pattern of the desired object. Once the mold is created, the pattern is removed, leaving a cavity that is then filled with molten metal. The use of water in the sand helps to bind the grains together, providing a strong mold that holds its shape during the pouring of the metal. Green sand casting is suitable for a wide range of materials and is often used for iron and steel castings.
2
. Dry Sand CastingAs the name suggests, dry sand casting employs a mixture of sand and a binder that does not contain moisture. This method produces molds that are more durable compared to green sand molds, making them ideal for more intricate designs and high-precision components.
The dry sand mixture is baked in an oven after the mold is formed, which hardens the binder and creates a strong mold that can withstand the high temperatures of molten metal. This type of casting is particularly beneficial for large production runs where the cost of the materials can be amortized over a significant number of parts. However, the initial setup costs can be higher than for green sand casting given the need for specialized equipment.
types of sand casting
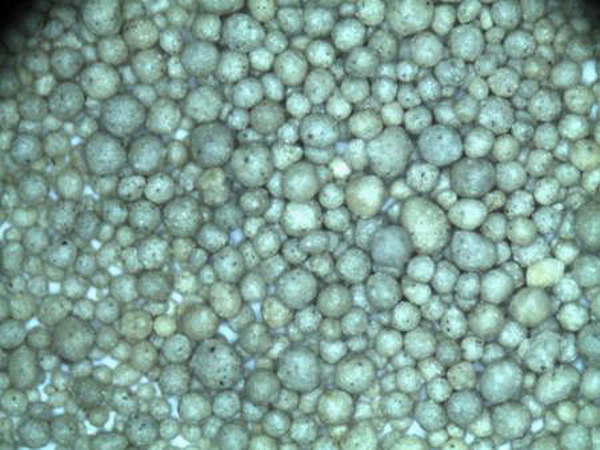
3. Skin-Dried Sand Casting
Skin-dried sand casting is a hybrid process that combines elements of both green and dry sand casting. In this method, a thin layer of the mold is dried using heat to create a stronger outer shell while the core remains moist. This technique provides enhanced surface finish and dimensional accuracy, making it suitable for parts that require both significant durability and aesthetic quality.
Skin-dried sand molds can be advantageous in reducing the time it takes to prepare the molds and can lead to increased productivity. This method is often utilized in the production of automotive components and complex geometries that demand a high degree of precision.
4. No-Bake Sand Casting
No-bake sand casting utilizes a chemical binder that hardens at room temperature without the requirement of heat. The sand mixture is formed around patterns and left to harden over time. This method is highly flexible and allows for intricate designs and complex shapes to be produced with relative ease.
No-bake casting is particularly advantageous for components that may be challenging to create using traditional methods. The lower working temperature also means that it can handle a wide range of metals, including aluminum and brass. Moreover, because no heat is involved in hardening the molds, this method can lead to reduced energy costs.
Conclusion
Sand casting remains a vital manufacturing technique due to its simplicity, adaptability, and cost-effectiveness. Each type of sand casting offers distinct advantages that cater to diverse production needs, allowing manufacturers to choose the most suitable method for their specific applications. Whether it is green sand for high-volume production, dry sand for durability, skin-dried for precision, or no-bake for flexibility, understanding these types can help industries optimize their casting processes and produce high-quality components efficiently. As technology advances, innovations in sand casting methods continue to emerge, further enhancing its viability in modern manufacturing.
Post time:સપ્ટેમ્બર . 26, 2024 00:24
Next:Exploring the Benefits and Techniques of Metal Sand Casting in Manufacturing