Understanding Sand Castings A Comprehensive Guide for Suppliers
Sand casting is a widely utilized manufacturing process in which molten metal is poured into a mold made from sand to create various metal components. This versatile process is cherished for its ability to produce complex shapes, making it a go-to choice for many industries, including automotive, aerospace, and construction. For suppliers in the sand casting sector, understanding the intricacies of this method is essential for meeting customer demands and maintaining a competitive edge.
What is Sand Casting?
At its core, sand casting involves creating a mold from a mixture of sand and a bonding agent, often clay. The mold is formed based on a model of the desired part, which is usually made of metal, plastic, or wood. Once the mold is prepared, molten metal is poured into it, allowed to solidify, and then removed to reveal the finished part. This process is advantageous for producing large and complex shapes that might be challenging to achieve with other fabrication methods.
Advantages of Sand Casting
One of the primary benefits of sand casting is its cost-effectiveness. The materials involved, primarily sand and metal, are relatively inexpensive, making it a preferred choice for producing large quantities of parts. Furthermore, the process is adaptable to various metals, including aluminum, iron, and magnesium, allowing suppliers to cater to diverse customer needs.
Another significant advantage of sand casting is its ability to produce components with excellent dimensional accuracy. Modern technologies, such as computer-aided design (CAD) and additive manufacturing for pattern making, further enhance the precision of sand casting.
Market Demand for Sand Castings
sand castings supplier
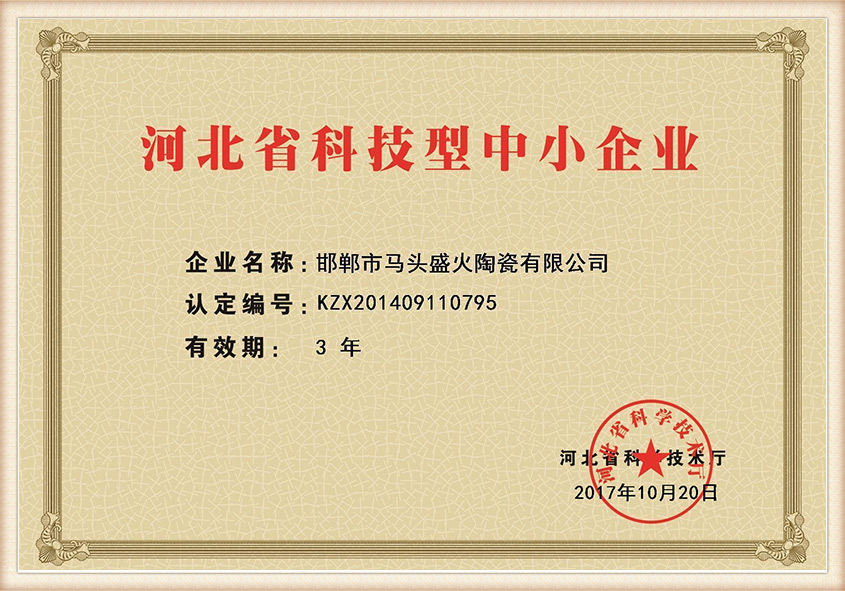
The global market for sand castings is continually growing, driven by the increasing demand for metal components across various sectors. The automotive industry is a notable consumer, utilizing sand castings for engine blocks, transmission cases, and other critical components. Similarly, the aerospace sector relies on sand castings for lightweight yet durable parts.
As suppliers navigate this expanding market, they must be aware of the trends influencing demand. For instance, the push for sustainability is leading many manufacturers to seek out eco-friendly materials and processes. Suppliers that can offer sustainable sand casting solutions will likely have a competitive advantage.
Challenges Faced by Sand Casting Suppliers
Despite its numerous advantages, sand casting is not without challenges. Quality control is a significant concern, as defects in the casting process can lead to costly rework or scrap. Suppliers must implement stringent quality assurance measures, including regular inspections and testing, to ensure they meet industry standards.
Additionally, the labor-intensive nature of sand casting can lead to variability in product quality. Investing in skilled labor and employee training will help minimize inconsistencies and enhance production efficiency.
Conclusion
In conclusion, sand casting presents unique opportunities and challenges for suppliers in the manufacturing sector. By understanding the process, advantages, and market dynamics, suppliers can position themselves strategically in this competitive landscape. Embracing technology, focusing on quality control, and committing to sustainability will be key factors in driving success in the sand casting industry. As demand continues to rise, those who adapt and innovate will undoubtedly thrive in this ever-evolving field.
Post time:ઓક્ટોબર . 04, 2024 09:07
Next:how much does sand casting cost