The Art and Science of Sand Casting Iron
Sand casting, also known as sand molded casting, is one of the oldest and most widely used metal casting techniques in the world. This method has been employed for centuries to produce complex shapes and components from a variety of metals, particularly iron. In this article, we explore the fundamental processes, advantages, and applications of sand casting iron.
What is Sand Casting?
Sand casting involves creating a mold from a mixture of sand, clay, and water. The process begins by creating a pattern—an exact replica of the object to be cast. This pattern is usually made from metal, plastic, or wood, and is designed to be slightly larger than the finished product to account for shrinkage during cooling.
The pattern is pressed into a sand mixture to form a mold cavity. The sand used in this process is typically fine and has great refractory properties, allowing it to withstand high temperatures without deforming. After the pattern is removed, the two halves of the mold are bound together, and the molten iron is poured into the cavity to create the desired shape.
Advantages of Sand Casting Iron
1. Versatility Sand casting can produce a wide range of sizes and shapes, from small intricate parts to large components. This versatility makes it suitable for various industries, including automotive, aerospace, and construction.
2. Cost-Effectiveness The sand casting process is economical, especially for low to medium production runs. The materials used—principally sand—are inexpensive and readily available. Additionally, the ability to create molds without significant cost outlay makes it an attractive option for many manufacturers.
3. High Tolerance Levels Although the surface finish of sand-cast products may not be as smooth as that produced by other methods, the dimensional tolerances achievable in sand casting can be very precise, making it suitable for parts that require careful specifications.
4. Good Thermal Properties Iron, especially cast iron, exhibits excellent thermal stability. This characteristic allows it to retain heat for extended periods, making it suitable for applications such as cookware and engine components.
sand casting iron
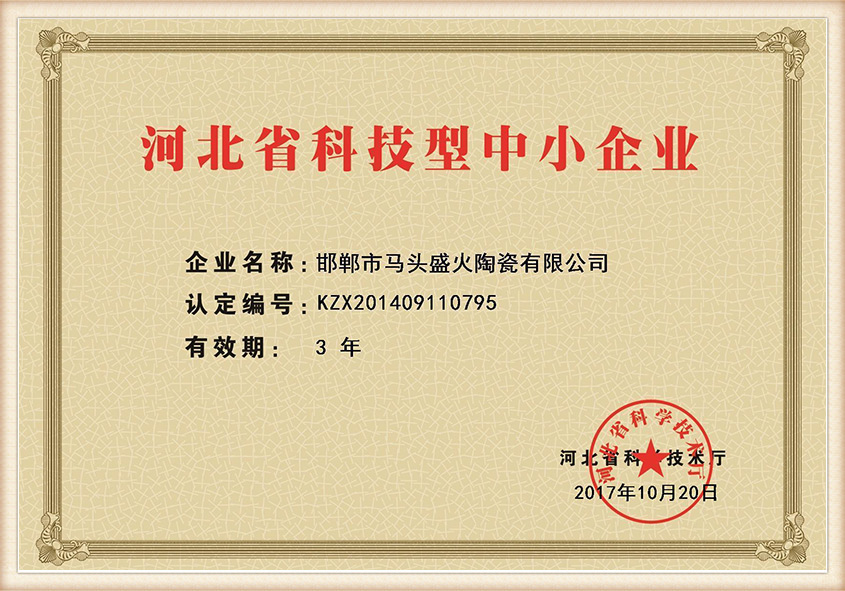
The Sand Casting Process
1. Pattern Making As mentioned, patterns are created to replicate the final product accurately. This phase is crucial, as defects in the pattern can lead to imperfections in the final casting.
2. Mold Preparation The sand mixture is prepared and compacted around the pattern to form the mold. This step often involves the use of binding agents to ensure the sand maintains its shape.
3. Melting and Pouring Iron is melted in a furnace, reaching temperatures of over 1,400 degrees Celsius. Once the iron is molten, it is poured into the prepared mold.
4. Cooling and Cleanup After the iron solidifies, the mold is broken apart to release the cast object. The casting may require additional machining to achieve precise dimensions and a smooth surface.
Applications of Sand Casting Iron
The applications of sand casting iron are extensive. It is commonly used to manufacture engine blocks, pipes, fittings, and intricate components for machinery. Additionally, the automotive industry relies heavily on this method for producing critical parts that require durability and strength.
Conclusion
Sand casting iron embodies both the artistry and engineering prowess of metalworking. Its long-standing history coupled with modern advancements continues to make it a preferred choice for manufacturers worldwide. As industries evolve and demand precise, durable components, the relevance of sand casting will endure, proving that traditional methods can combine seamlessly with contemporary technology. Whether for a hobbyist or a large-scale manufacturer, the beauty of sand casting lies in its ability to transform raw materials into functional art.
Post time:નવેમ્બર . 12, 2024 00:50
Next:super sand g2