Understanding Sand Casting A Comprehensive Overview
Sand casting, also known as sand mold casting, stands as one of the oldest and most widely used metal casting processes in modern manufacturing. This method enables the creation of intricate metal parts that are essential in various industries, including automotive, aerospace, and machinery. The versatility, cost-effectiveness, and ability to produce complex shapes make sand casting an invaluable technique in the metalworking realm.
The Sand Casting Process
The sand casting process begins with the preparation of a mold. The first step involves creating a pattern, which is a replica of the final product made from materials like wood, plastic, or metal. This pattern is then covered with a mixture of sand and binding agents to form a mold. The primary binding agents used in sand casting include clay, which serves to hold the sand grains together, and sometimes chemical binders that enhance the mold's strength.
Once the sand is compacted around the pattern, the mold is ready for the next step removing the pattern to create a cavity in the sand. This cavity serves as the negative form of the object to be cast. The mold is then assembled, ensuring that all pieces fit securely to prevent leakage during the pouring of molten metal.
Next, the molten metal is prepared for pouring. This metal is heated to a specific temperature, based on its alloy composition, and once it reaches a liquid state, it is poured into the cavity of the sand mold. This step is crucial, as the quality of the metal and the precision of the pouring can significantly affect the final product.
After the molten metal has cooled and solidified, the next step involves breaking away the sand mold to reveal the cast part. This process is known as shakeout. The sand can often be reused, making sand casting an environmentally friendly option in comparison to other methods. Once the casting is retrieved, it usually undergoes finishing processes like machining, grinding, or polishing to achieve the required final dimensions and surface finish.
Advantages of Sand Casting
sand casting description
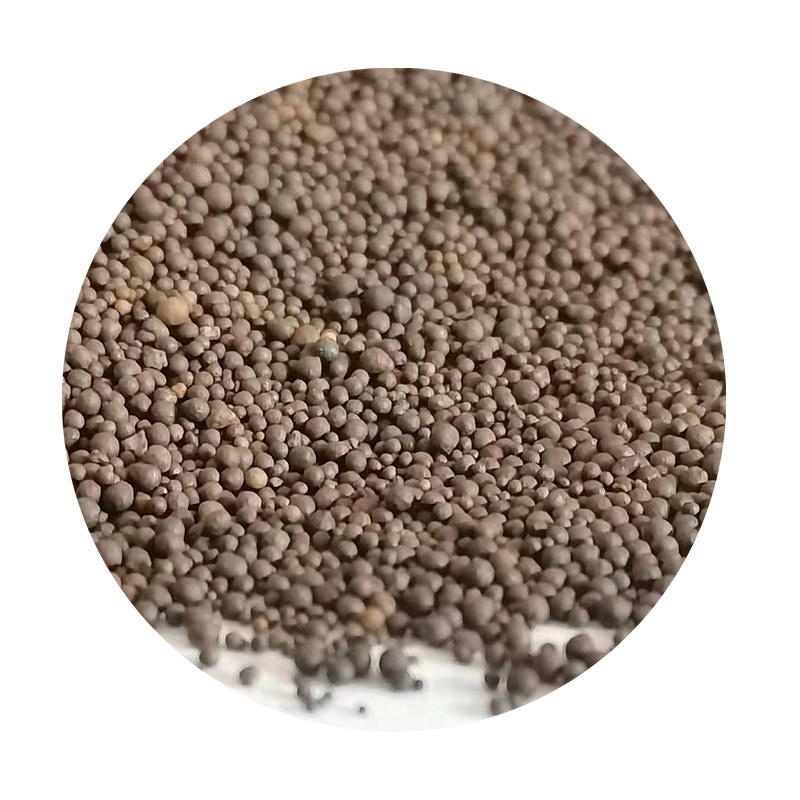
One of the most significant advantages of sand casting is its ability to accommodate a wide range of metal alloys, including iron, aluminum, bronze, and magnesium. This flexibility allows manufacturers to choose the most suitable material for specific applications. Additionally, sand casting can produce large castings weighing several tons, making it ideal for heavy-duty applications.
Cost-effectiveness is another compelling advantage. The materials used in sand casting, primarily sand and metal, are relatively inexpensive. Moreover, the production process requires less complex equipment compared to other casting methods, such as die casting, which significantly reduces initial setup costs. This affordability makes sand casting a popular choice for both small and large production runs.
The complexity of shapes achievable through sand casting is noteworthy. Designers can create intricate geometries that may be challenging to achieve through other manufacturing methods. This capability opens doors for innovation and creativity in design, rendering sand casting an attractive option for engineers and designers alike.
Challenges and Considerations
Despite its many benefits, sand casting is not without its challenges. The dimensional accuracy of sand castings can vary, leading to potential complications during subsequent machining processes. Additionally, surface finish quality might not always meet the stringent requirements of high-precision industries, necessitating further finishing work.
Another challenge lies in ensuring mold integrity. If the sand mixture is not properly prepared or compacted, defects such as sand inclusions or blowholes may occur in the final casting, compromising its structural integrity.
Conclusion
In summary, sand casting remains a fundamental method in the manufacturing industry due to its versatility, cost-effectiveness, and capacity for complex shapes. Understanding the intricacies of the sand casting process, from mold preparation to the final casting, allows manufacturers to leverage its advantages while being mindful of its limitations. As technology continues to advance, the sand casting process may evolve further, integrating modern materials and techniques that enhance its efficiency and performance in the manufacturing landscape. Thus, sand casting will undoubtedly continue to play a significant role in the production of metal components for years to come.
Post time:નવેમ્બર . 11, 2024 08:49
Next:sand preparation in foundry