Understanding Sand Casting Components
Sand casting, one of the oldest and most versatile metal casting processes, has proved its worth over centuries for manufacturing a variety of components. This process involves shaping molten metal within a mold made of sand, which, once cooled, becomes the desired component. This article will delve into the essential components of sand casting, explaining how each part contributes to producing high-quality castings.
1. Mold
The mold is the most critical component in the sand casting process. It is made from a mixture of sand, clay, and water, which is formed to create the shape of the desired part. Molds can be classified into two types green sand molds and dry sand molds. Green sand molds use moist sand, which provides excellent mold flexibility, allowing intricate details to be captured. Dry sand molds, on the other hand, are baked to harden the sand mixture, which results in a more rigid mold. While green sand is often preferred for its ease and cost-effectiveness, dry sand is typically used for more complex and precision-required designs.
2. Pattern
The pattern is a replica of the final product and is inserted into the sand to create the mold cavity. Patterns can be made from various materials such as wood, metal, or plastic, depending on the volume of production and the required precision. Patterns can be of different types, including single-use patterns, which are discarded after one use, and permanent patterns, which can be used multiple times to produce castings consistently. The design of the pattern must account for shrinkage—a common phenomenon in metal casting—and should allow for proper draft angles to facilitate easy removal from the mold.
3. Core
For components that require internal features, cores are introduced into the mold. Cores are usually made of sand and held within the mold to create hollow sections in the cast part. The placement and design of cores are crucial as they impact the strength and integrity of the final casting. Cores can also be coated with resin or use other binding agents to enhance their strength. Proper venting should be provided to allow gases to escape during the pouring of molten metal, preventing defects like blowholes.
4. Melting Furnace
sand casting components
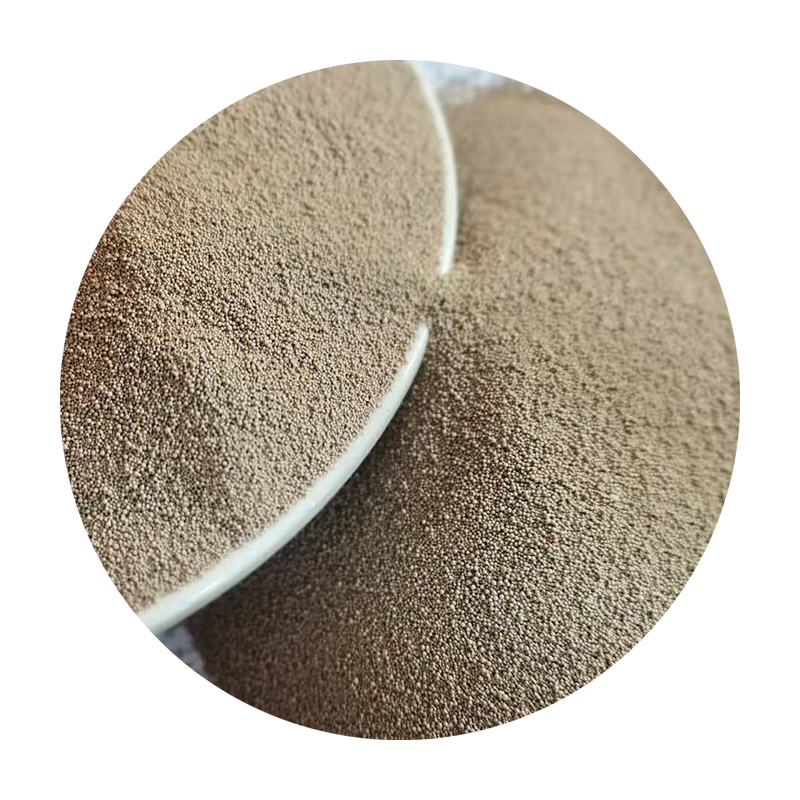
The melting furnace is where the raw metals are transformed into molten form. Various types of furnaces, such as induction furnaces, electric arc furnaces, or oil-fired furnaces, can be used based on the type of metal being melted. Each furnace type has its advantages and is chosen based on the production needs, efficiency, and cost considerations. Controlling the temperature and maintaining the homogeneity of the molten metal is crucial, as impurities or inconsistencies can significantly affect the quality of the final product.
Once the metal is molten and ready, it must be transferred into the mold through an efficiently designed pouring system. This system is critical to minimize turbulence during the pour to avoid introducing air pockets or imperfections in the casting. Equipment such as ladles or automated pouring systems can be used to ensure a smooth and controlled pouring process, which is important for achieving the desired surface finish and dimensional accuracy.
6. Cooling and Solidification
After the molten metal is poured into the mold, it begins to cool and solidify. The cooling rate can influence the microstructure and mechanical properties of the casting. The finer grain structure tends to develop with slower cooling rates, leading to improved strength. Proper cooling techniques, including controlling the ambient temperature and using chillers when necessary, can ensure that the casting solidifies correctly without forming defects such as cracks or warpage.
7. Finishing Processes
Once the casting has cooled sufficiently, it is removed from the mold and needs further finishing to reach the final specifications. This can include processes such as trimming, grinding, and surface treatment. The finishing touches are vital to ensure that the component not only meets aesthetic requirements but also adheres to functional specifications, including tolerances and surface finish quality.
Conclusion
In conclusion, the sand casting process is a complex series of steps that involves various components, each playing a vital role in the production of high-quality castings. Understanding the intricacies of these components—from the mold and pattern to the pouring methods and finishing techniques—enables manufacturers to optimize processes, reduce defects, and enhance the overall efficiency of their production systems. Whether for small-scale or large-scale production, mastering these elements is essential in the art and science of sand casting.
Post time:નવેમ્બર . 05, 2024 04:50
Next:sand casting company