Sand Casting Alloys A Comprehensive Overview
Sand casting is one of the most widely used metal casting processes, primarily due to its versatility, cost-effectiveness, and ability to produce complex shapes. This technique involves creating a mold from a sand mixture, into which molten metal is poured, allowing it to solidify into the desired form. The selection of alloys used in sand casting significantly influences the quality and performance of the final product. This article explores various types of alloys commonly used in sand casting, their properties, advantages, and applications.
Types of Alloys Used in Sand Casting
1. Aluminum Alloys Aluminum is a popular choice for sand casting due to its lightweight nature, excellent corrosion resistance, and high strength-to-weight ratio. Common aluminum alloys used include 356, 319, and 413. These alloys are typically used in applications such as automotive components, aerospace parts, and marine fixtures. Aluminum's low melting point also makes it easier to work with, allowing for efficient production cycles.
2. Bronze Alloys Bronze, an alloy of copper and tin, is renowned for its durability and corrosion resistance. It is frequently used in sand casting for applications requiring high wear resistance, such as marine hardware, gears, and bearings. The casting process can include various bronze alloys, such as silicon bronze and aluminum bronze, each offering unique properties tailored to specific end-use applications.
3. Cast Iron Cast iron is another widely used material in sand casting, particularly for applications requiring excellent machinability and wear resistance. Gray cast iron, ductile cast iron, and white cast iron are the three main types. Gray cast iron is often used for engine blocks and pipes, while ductile cast iron is favored for automotive components due to its increased tensile strength and ductility.
sand casting alloys
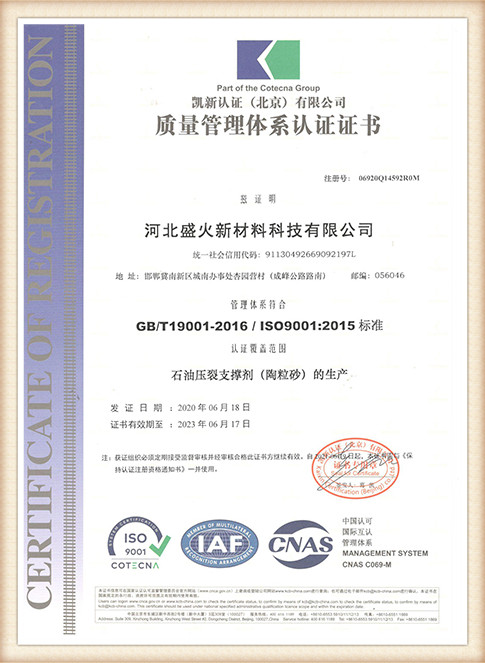
4. Steel Alloys Steel alloys, including carbon steel and stainless steel, are also suitable for sand casting. Carbon steel castings are commonly used in construction and infrastructure applications, while stainless steel castings offer superior corrosion resistance, making them ideal for chemical processing and food handling industries. Steel's high strength allows for the production of heavy-duty components.
5. Zinc Alloys Zinc alloys are gaining popularity in sand casting due to their excellent fluidity and ability to fill intricate molds. Zamak alloys, a group of zinc-aluminum alloys, are particularly noted for their good mechanical properties and are widely used in the automotive and consumer products industries. Additionally, zinc's ability to resist corrosion makes it a preferred choice for decorative applications.
Advantages of Using Alloys in Sand Casting
Using the right alloy in sand casting offers numerous advantages
- Customization Different alloys can be formulated with specific properties to meet the unique demands of various applications. - Strength and Durability Alloys often provide enhanced mechanical strength and durability compared to pure metals, making them suitable for challenging environments. - Cost-Effectiveness Utilizing cheaper and more readily available alloys can significantly reduce material costs while still achieving desired performance characteristics. - Machinability Many casting alloys exhibit excellent machinability, allowing for efficient post-casting processing. Conclusion
Sand casting remains a fundamental manufacturing technique, and the choice of alloys is crucial in achieving the desired balance between performance and cost. Aluminum, bronze, cast iron, steel, and zinc alloys each offer unique advantages that cater to a wide range of industries, from automotive to aerospace and beyond. Understanding the properties and applications of these alloys enables manufacturers to optimize their production processes and improve the quality of their cast products. As technology advances and new alloy formulations are developed, the versatility and effectiveness of sand casting are likely to continue evolving, solidifying its role as a core process in metal fabrication.
Post time:નવેમ્બર . 10, 2024 13:57
Next:Super Sand Bond G2 for Enhanced Durability and Performance in Construction Projects