The Sand Casting Industry An In-Depth Look
The sand casting industry is a vital part of the manufacturing sector, offering a versatile and cost-effective method for producing metal parts and components. This centuries-old casting process has evolved significantly over the years, driven by advancements in technology and increasing demands for precision and efficiency. In this article, we will delve into the mechanics of sand casting, its applications, advantages, and challenges, as well as its future in the manufacturing landscape.
What is Sand Casting?
Sand casting involves creating a mold from a mixture of sand, clay, and water to form a cavity that represents the desired shape of the final product. The core components of the sand casting process include creating the mold, melting the metal, pouring the molten metal into the mold, and finally, removing the casting once it has cooled and solidified.
The process begins with the design and fabrication of a pattern, usually made from metal, plastic, or wood, that is a replica of the desired component. This pattern is then set into a sand mixture, which is compacted around it to form the mold. In many cases, cores are used to create internal features and hollow sections in the final casting. After the metal is poured into the mold and allowed to cool, the sand is removed, revealing the cast part.
Applications of Sand Casting
Sand casting is used in various industries, including aerospace, automotive, construction, and marine. Its adaptability makes it ideal for producing both small components, like brackets and housings, to large items such as engine blocks and industrial machinery parts. The ability to cast complex shapes and the use of various metals—including iron, aluminum, and bronze—further expands its applications.
For instance, in the automotive industry, sand casting is employed to manufacture engine parts, transmission housings, and other critical components that require durability and strength. Meanwhile, the aerospace sector relies on sand casting for producing lightweight yet robust parts that can withstand extreme conditions.
Advantages of Sand Casting
sand cast industries
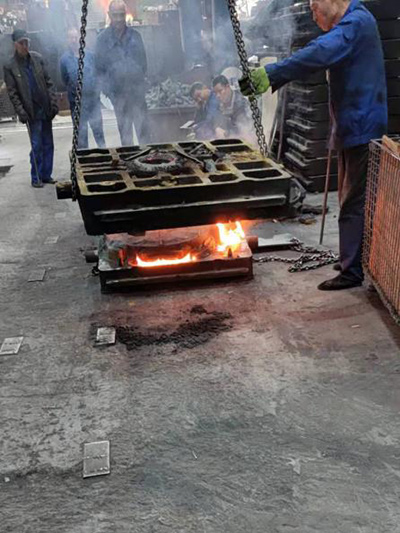
One of the primary benefits of sand casting is its cost-effectiveness, particularly for low to medium production volumes. The materials used—sand, clay, and water—are inexpensive and readily available, making it an attractive option for manufacturers. Furthermore, the process allows for flexibility in design modifications, enabling rapid prototyping and customization.
The sand casting method also accommodates a variety of metal types, allowing for the production of a wide range of parts with different mechanical properties. Additionally, the process can handle large castings that would be challenging or impossible to create using other methods, such as die casting or investment casting.
Challenges in Sand Casting
Despite its advantages, sand casting is not without challenges. One of the significant issues is the surface finish of the final product, which may require additional machining to achieve the desired quality and precision. Furthermore, the casting process can lead to defects such as shrinkage, inclusions, or misalignments, affecting the integrity of the component.
Another challenge is the environmental impact of the process. The sand used in casting must be carefully managed to minimize waste and ensure sustainability. Innovations in reclaiming sand can help address this issue, but continued efforts are necessary to improve the overall footprint of the industry.
The Future of Sand Casting
As technology continues to advance, the sand casting industry is seeing numerous innovations that promise to enhance its efficiency and sustainability. Developments in 3D printing and computer-aided design (CAD) are transforming the way molds and patterns are created, significantly reducing lead times and improving accuracy. Additionally, automation and robotics offer opportunities for streamlining the casting process and improving safety.
Moreover, the push for greener manufacturing practices is prompting sand casting facilities to adopt eco-friendly materials and processes. From using synthetic sands that reduce environmental impact to enhancing energy efficiency in melting operations, the industry is evolving to meet modern sustainability demands.
In conclusion, the sand casting industry stands as a robust and dynamic sector within manufacturing. Its ability to produce complex and varied metal components at a relatively low cost makes it an invaluable method across a range of industries. By addressing its challenges and embracing technological advancements, sand casting is poised to remain a critical component of the manufacturing landscape for years to come.
Post time:નવેમ્બર . 17, 2024 11:36
Next:Techniques for Sanding 3D Prints for a Smooth Finish and Enhanced Detail