Understanding Sand Casting and Choosing the Right Supplier
Sand casting is one of the oldest and most versatile manufacturing processes used to create metal parts. This method involves using sand as the primary mold material, which allows for the fabrication of a wide range of complex geometries. With applications across various industries including automotive, aerospace, and machinery, understanding the nuances of sand casting and how to select the appropriate supplier is essential for high-quality production.
The sand casting process begins with creating a mold from a mixture of sand and a binding agent. The mold is formed around a pattern that mimics the shape of the desired product. Once the mold is prepared, molten metal is poured into the cavity, where it solidifies, taking on the shape of the mold. After cooling, the mold is broken away to reveal the cast metal piece. This process is favored for its cost-effectiveness, scalability, and ability to create large and complex components.
When choosing a sand casting supplier, several factors come into play. First and foremost, consider the supplier’s experience and reputation in the industry. Established suppliers often have a track record of delivering quality products consistently. Look for testimonials or case studies that demonstrate their capabilities and customer satisfaction.
Another critical aspect is the supplier’s technological capabilities. Modern sand casting requires sophisticated equipment and processes to ensure precision and efficiency. Suppliers using advanced technologies such as 3D printing for patterns and computer simulations for mold designs can significantly enhance the quality of the final product. Ensuring that your supplier utilizes up-to-date techniques will help avoid common pitfalls such as defects and inaccuracies in the casting.
sand casting supplier
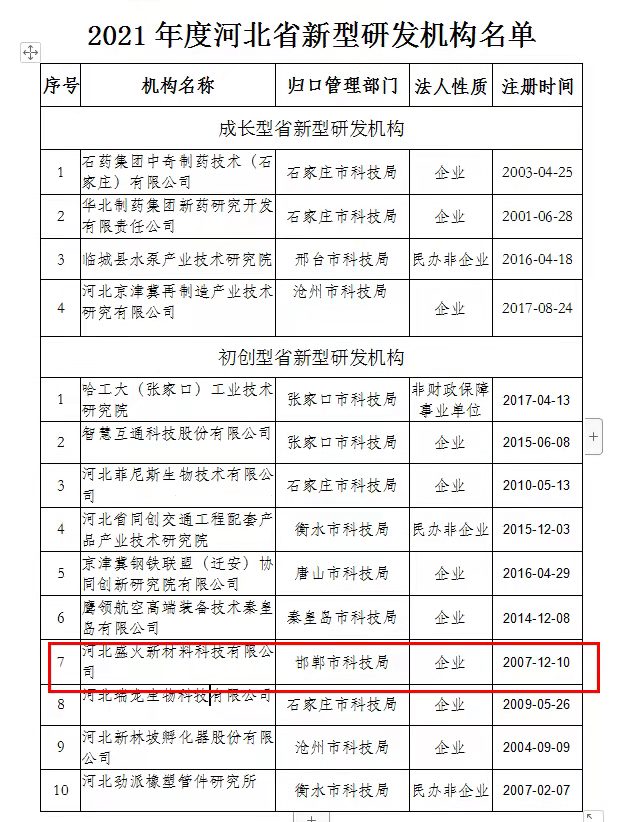
Quality control is also vital when selecting a sand casting supplier. A supplier with stringent quality assurance processes can help minimize the risks of defects. Inquire about their quality control measures, certifications, and testing methods. Ensuring that the supplier adheres to international standards and industry regulations can provide further confidence in their output.
Additionally, consider the supplier’s ability to meet your specific needs regarding production volume, lead times, and customization capabilities. A reliable supplier should be able to handle orders ranging from small-scale prototypes to large production runs. Ensure they can accommodate your timeline and possess the flexibility to adapt to changes in your production requirements.
Communication is another critical element in the supplier relationship. A responsive and transparent supplier can make the process smoother, allowing for quicker resolutions to any issues that may arise and facilitating better collaboration on design changes.
In conclusion, sand casting remains a fundamental method in metal part production due to its adaptability and cost-effectiveness. By carefully selecting a qualified sand casting supplier, businesses can ensure high-quality outputs that meet their specific needs. Focus on experience, technological capabilities, quality control, production flexibility, and communication when making your choice. With the right partner, you can harness the full potential of sand casting for your projects.
Post time:સપ્ટેમ્બર . 19, 2024 02:59
Next:типи піску