Sand Casting Processes An Overview
Sand casting, a process that has stood the test of time, is one of the oldest and most utilized methods of metal casting worldwide. It involves creating a mold from a sand mixture to produce metal parts and components, making it a versatile and cost-effective solution for various industries, including automotive, aerospace, and heavy machinery.
The sand casting process begins with the creation of a mold, typically made from a mixture of sand, clay, and water. The sand serves as the primary material due to its excellent ability to retain shape and withstand high temperatures. The process begins by compacting the sand around a pattern, which represents the object to be cast. Patterns can be made from various materials, including metals or plastics, and are designed to accommodate the shrinkage that occurs during the cooling of the molten metal.
Sand Casting Processes An Overview
Before pouring the molten metal into the mold, it is essential to create vents to allow gases to escape during the pouring process. This helps to prevent defects in the final casting. The metal is then heated to a liquid state and poured into the mold through a pouring basin and runner system, filling the cavity created by the pattern.
sand casting processes
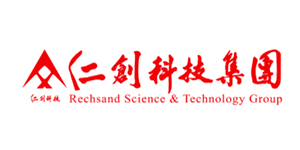
After the metal has cooled and solidified, the next step is to remove the mold. This can be done by breaking apart the sand mold, which can be reused for future castings after being reconditioned. The final casting is then cleaned of any sand or impurities, often requiring machining processes to achieve the desired surface finish and dimensions.
One of the significant advantages of sand casting is its ability to produce large and complex shapes that would be difficult or costly to manufacture using other methods. Additionally, sand casting is adaptable to a wide range of metals, including aluminum, iron, and bronze, making it suitable for diverse applications. The process also allows for the production of both small and large quantities, catering to the needs of different projects.
Despite its many advantages, sand casting does have some limitations. The surface finish of sand castings is generally rougher compared to other casting methods, and achieving tight tolerances may require additional machining. However, for many applications, the benefits of sand casting outweigh these drawbacks.
In conclusion, sand casting remains a fundamental process in the manufacturing landscape. Its flexibility, cost-effectiveness, and ability to create intricate designs make it an indispensable method in industries that rely on durable metal components. As technology continues to evolve, innovations in sand casting processes are likely to enhance its efficiency and effectiveness, ensuring its relevance for many years to come.
Post time:સપ્ટેમ્બર . 05, 2024 02:37
Next:3d print sand casting