The Importance of Foundry Sand in Metal Casting
Foundry sand plays a critical role in the metal casting industry, serving as a primary ingredient in the creation of molds for various metal components. This specific type of sand, often characterized by its unique properties including high silica content and fine particle size, enables the production of high-quality castings while maintaining cost-effectiveness and efficiency in manufacturing processes.
Traditionally, foundry sand is composed mainly of silica, which is derived from quartz and is renowned for its ability to withstand high temperatures. When mixed with binders, foundry sand is molded into various shapes to create molds. The quality of the sand directly affects the integrity and surface finish of the final cast product. A well-prepared foundry sand allows for precise detail reproduction and minimizes defects, ensuring that the cast parts meet stringent specifications.
The Importance of Foundry Sand in Metal Casting
Moreover, the reusable nature of foundry sand contributes to its popularity in industrial applications. After the casting process is complete, used sand can be reclaimed and recycled for subsequent use. This not only reduces waste but also lowers the overall cost of the casting process. Reclamation technologies have advanced over the years, providing methods to clean and reuse foundry sand multiple times without significant loss in quality. As industries become more conscious of sustainability, the ability to recycle foundry sand aligns well with current environmental practices.
making foundry sand
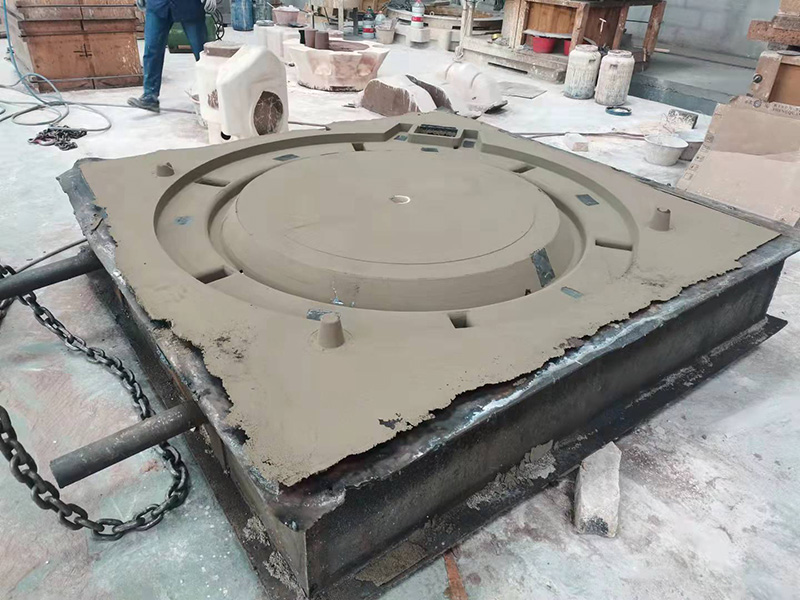
However, the use of foundry sand is not without challenges. The demand for quality raw materials can lead to sourcing competition, impacting prices and availability. Additionally, the process of preparing and reclaiming foundry sand requires careful management to prevent contamination from metal residues, binders, and other materials. Manufacturers must continuously invest in research and development to enhance reclamation techniques and ensure the quality of reclaimed sand meets industry standards.
Innovation in foundry sand alternatives is also emerging, driven by the need for more sustainable practices in casting. Some manufacturers are exploring the use of by-products or synthetic alternatives that can mimic the properties of traditional foundry sand. These alternatives aim to reduce the environmental impact associated with sand extraction and processing while maintaining the required performance characteristics.
As we look to the future, it is clear that foundry sand will continue to be a cornerstone of the metal casting industry. The ongoing advancements in recycling methods and the exploration of alternative materials will contribute to a more sustainable and efficient industrial landscape. Foundry sand not only plays a pivotal role in ensuring quality and precision in metal casting but also aligns with the growing demand for environmentally responsible manufacturing practices.
In conclusion, foundry sand is an indispensable material within the metal casting framework. Its unique properties, combined with the ability to be recycled, position it as a valuable resource. As the industry evolves, ongoing efforts to improve foundry sand management and explore sustainable alternatives will ensure that this vital material continues to support innovation and excellence in the metal casting sector.
Post time:ડીસેમ્બર . 15, 2024 17:22
Next:sand casting foundry