The Role of Ceramsite Foundry Sand in Metal Casting A Comprehensive Overview
In the field of metal casting, achieving high-quality castings with excellent surface finish and dimensional accuracy is crucial. One of the materials that have emerged as a viable alternative to traditional foundry sands is ceramsite foundry sand. This innovative material is designed to enhance casting performance while offering several advantages over conventional sand options.
What is Ceramsite Foundry Sand?
Ceramsite foundry sand is made from specially processed clay materials that are sintered at high temperatures. This process transforms the raw materials into granular ceramics, which possess unique properties that contribute to their effectiveness in casting applications. The resultant ceramsite granules are characterized by a spherical shape, enhanced strength, and a consistent particle size distribution. These features are essential for achieving optimal packing density in molds, which leads to improved metal flow and reduced defects in the cast products.
Advantages of Ceramsite Foundry Sand
1. Improved Casting Quality One of the main advantages of using ceramsite foundry sand is the significant improvement in casting quality it provides. Its uniform particle size helps to minimize the occurrence of casting defects such as sand inclusions and surface imperfections. The smooth surface of ceramsite sand also contributes to a better finish on cast products, reducing the need for secondary machining processes.
ceramsite foundry sand
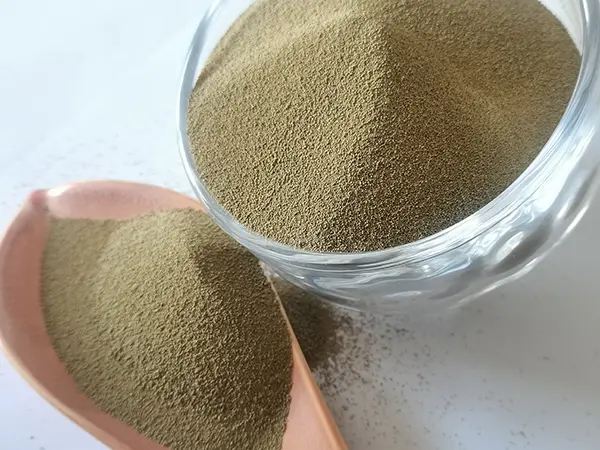
2. High Thermal Stability Ceramsite foundry sand exhibits excellent thermal stability, making it suitable for high-temperature applications. Unlike conventional sands that can break down or change properties under extreme heat, ceramsite maintains its integrity during the casting process. This thermal resilience is crucial for preventing expansion and deformation, which can lead to casting errors.
3. Lower Environmental Impact As the industry moves towards more sustainable practices, ceramsite foundry sand offers a solution with a lower environmental footprint. It is reusable, meaning that after the casting process, ceramsite can be cleaned, reprocessed, and used multiple times. This not only reduces waste but also decreases the need for raw material extraction.
4. Enhanced Strength and Durability The structural integrity of ceramsite foundry sand means it can withstand the mechanical stresses associated with metal casting. This durability leads to longer mold life, which translates to cost savings over time. Foundries can experience reduced downtime, as the need for frequent re-molding is minimal with ceramsite.
5. Versatility in Applications Ceramsite foundry sand is suitable for a wide range of metal casting processes, including sand casting, investment casting, and investment shell molding. Its versatility makes it an attractive option for foundries looking to optimize different metal types and casting techniques.
Conclusion
In conclusion, ceramsite foundry sand represents a significant advancement in the metal casting industry. Its unique properties – including improved casting quality, thermal stability, environmental friendliness, and high durability – make it an excellent choice for foundries aiming to enhance their production processes. As the demand for efficient and sustainable foundry materials continues to rise, ceramsite foundry sand is poised to play an increasingly important role in the future of metal casting. By incorporating this innovative material into their operations, foundries can not only improve their product quality but also contribute to a more sustainable manufacturing ecosystem.
Post time:ઓગસ્ટ . 07, 2024 23:25
Next:Specifications for Enhanced Performance of Resin Coated Sand in Industrial Applications