Foundry Sand Contamination Causes, Impacts, and Solutions
Foundry sand is an essential material used in the manufacturing and metal casting industries. It serves as a mold material for a variety of metal products, providing the right thermal and mechanical properties needed for high-quality casting. However, the contamination of foundry sand is an emerging concern that can significantly affect both the production process and the environment. Understanding the causes, impacts, and potential solutions for foundry sand contamination is vital for industry stakeholders.
Causes of Foundry Sand Contamination
Contamination of foundry sand occurs due to a variety of factors. One of the primary causes is the degradation of the sand itself during the casting process. High temperatures and the presence of molten metal can lead to the breakdown of the sand grains, generating fine dust or particles that may mix with the reusable sand. Additionally, impurities in the raw materials used for sand preparation, such as clay, silt, or organic matter, can also introduce contaminants.
Another significant factor contributing to foundry sand contamination is the recycling processes employed in many foundries. Although recycling helps reduce waste and lower costs, the repeated use of sand can accumulate various contaminants such as oils, resins, and metal residues. This accumulation not only affects the sand's physical properties but can also lead to inconsistencies in final product quality.
Impacts of Contamination
The contamination of foundry sand can have serious implications for both the production process and the final product. First and foremost, contaminated sand can result in defects in castings, such as surface imperfections, inclusions, and dimensional inaccuracies. These defects can compromise the structural integrity of the final product, leading to costly rework or even failure in critical applications.
Moreover, the use of contaminated sand can adversely impact the efficiency of the casting process itself. The presence of contaminants can affect the thermal properties of the sand, leading to uneven cooling and longer cycle times. This inefficiency can result in increased energy consumption and higher operational costs for foundries.
foundry sand contamination
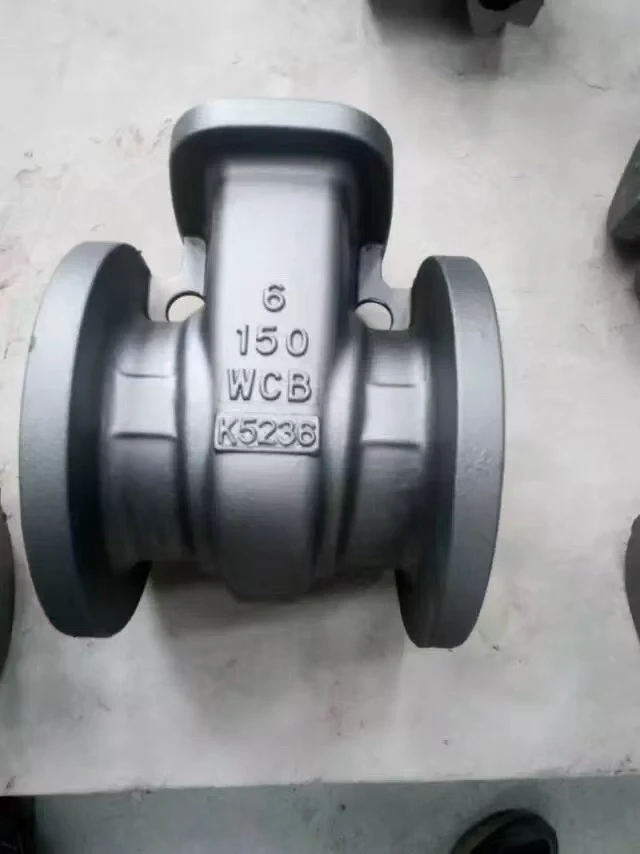
Environmental concerns are also significant when it comes to foundry sand contamination. Contaminated sand can contribute to soil and water pollution when disposed of improperly. Heavy metals and chemical additives from the casting process can leach into the environment, posing risks to ecosystems and human health.
Solutions and Best Practices
To mitigate the issues associated with foundry sand contamination, several solutions and best practices can be implemented. Regular monitoring of sand quality is essential to identify contamination early. Utilizing advanced screening techniques can help separate clean sand from contaminated materials, allowing for more effective recycling.
Another approach is the use of cleaner production techniques. By optimizing the composition of the sand mix and utilizing eco-friendly binders, foundries can reduce the likelihood of contamination. Additionally, investing in technology that allows for better sand reclamation can significantly enhance sand purity and reduce the environmental footprint.
Training and educating employees about the importance of proper handling and storage of foundry sand can also play a crucial role in minimizing contamination. Employees should be encouraged to follow strict protocols to avoid introducing foreign materials into the sand mix.
Lastly, collaboration with regulatory bodies and adherence to industry standards can help ensure that foundries maintain high levels of quality and environmental responsibility. Implementing waste management strategies that focus on recycling and reusing contaminated sand can also lead to more sustainable practices within the foundry industry.
Conclusion
Foundry sand contamination is a multifaceted issue that presents challenges for manufacturers, the environment, and the broader economy. By understanding the causes and impacts of this contamination, industry stakeholders can adopt effective solutions to minimize risks and maintain high-quality production. Through continuous improvement and innovation, the foundry industry can work towards a more sustainable and efficient future, ensuring that the materials used are not only effective but also environmentally sound.
Post time:ડીસેમ્બર . 02, 2024 01:24
Next:Techniques and Processes for Sand Preparation in Metal Foundries