Foundry Casting Sand The Backbone of Metal Casting
Foundry casting sand is a critical component in the metal casting process, playing an integral role in shaping and forming intricate metal parts and components that are essential in various industries, from automotive to aerospace. The process of metal casting involves pouring liquid metal into a mold, which is created using sand and other materials. This article explores the significance of foundry casting sand and its applications in modern manufacturing.
Types of Foundry Casting Sand
There are several types of foundry sands used in casting processes, each possessing unique properties that make them suitable for different applications. The most common types include
1. Silica Sand This is the most widely used type of casting sand, composed primarily of silicon dioxide. Silica sand is known for its high melting point, thermal stability, and excellent strength, making it ideal for creating molds that can endure the heat of molten metal.
2. Clay-Bonded Sand Often enhanced with clay, this type of sand is used for its plasticity and ability to hold its shape. The clay acts as a binding agent that helps the sand retain its form during the casting process.
3. Zircon Sand Known for its high thermal resistance and low expansion, zircon sand is often used for casting in applications that require tight tolerances and high precision.
4. Chromite Sand This sand type is favored for its thermal stability and low thermal expansion. It is often used in steel foundries for casting applications where high temperatures are prevalent.
The Casting Process
foundry casting sand
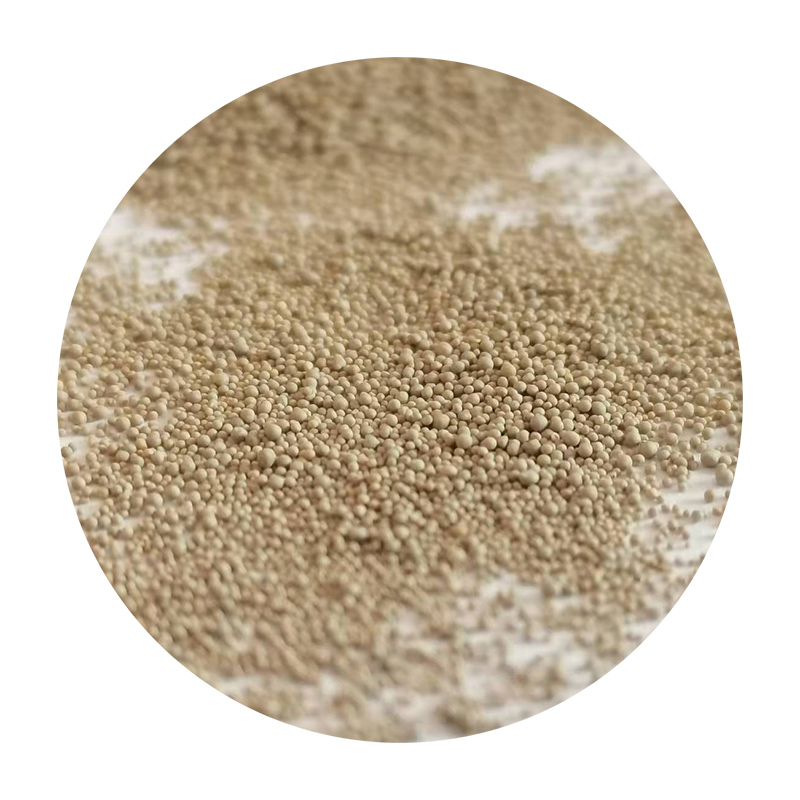
The process of casting with foundry sand involves several steps. First, a pattern of the object to be cast is created, which is often made of metal, plastic, or wood. This pattern is then used to create a mold in the sand. The sand is packed around the pattern to form a mold cavity. Once the mold is ready, it is removed from the pattern and prepared for casting.
After preparation, molten metal is poured into the mold cavity and allowed to cool and solidify. After cooling, the mold is broken away, revealing the final cast metal object. The quality of the casting is heavily dependent on the properties of the sand used, as well as the skill of the foundry workers in preparing the molds.
Advantages of Using Foundry Casting Sand
One of the primary advantages of using foundry casting sand is its flexibility. Sand can be reused multiple times, making it an economically viable option for manufacturers. Additionally, the ability to easily mold and form various shapes allows for high levels of customization in the casting process.
Another significant benefit is the thermal conductivity of sand, which helps manage the cooling rates of the metal, reducing the risk of defects such as warping or cracking during the solidification process.
Environmental Considerations
In recent years, there has been an increased focus on the environmental impact of foundry operations. Many foundries are now adopting eco-friendly practices, such as the use of synthetic sands and the recycling of spent sands. This shift not only helps reduce waste but also minimizes the carbon footprint of the casting process.
Conclusion
Foundry casting sand is a vital material in the manufacturing landscape, providing the foundational structure needed for successful metal casting. As technology advances and industries evolve, the importance of innovation in sand materials and casting techniques will continue to grow, ensuring that foundry casting remains an essential part of production in various sectors. Whether in creating simple components or complex machinery parts, the role of foundry casting sand is, and will remain, indispensable in modern manufacturing.
Post time:ડીસેમ્બર . 12, 2024 11:53
Next:when was sand casting invented