Facing Sand in Foundry An Essential Element for Quality Casting
In the world of metal casting, the use of sand is paramount in creating molds that can withstand the rigors of high-temperature metal pours. Among the various types of sand used in foundries, facing sand emerges as a critical component for producing high-quality castings. This article delves into the role of facing sand, its composition, properties, and its impact on the overall casting process.
What is Facing Sand?
Facing sand is the top layer of the sand in a mold that is in direct contact with the molten metal. It provides several essential functions it forms the surface of the casting, influences the finish quality, and ensures that the molten metal adheres to the mold. Essentially, facing sand plays a vital role in determining the accuracy and texture of the final product.
Composition and Properties
Typically, facing sand consists of fine-grained sand that is coated with a mixture of bonding agents and additives to enhance its performance. The most common materials used include silica, clay, and various organic materials. The composition of facing sand can vary depending on the type of metal being cast and the complexity of the mold design.
Key properties of effective facing sand include
1. Particle Size The grain size affects the surface finish of the casted metal. Finer sands result in smoother surfaces while coarser sands may lead to a rougher texture. 2. Refractoriness It needs to withstand high temperatures without deforming or breaking down. The refractoriness is determined by its mineral composition and any additives used.
3. Moisture Retention The ability to retain moisture is crucial for preventing the sand from drying out during the casting process. Proper moisture levels help in achieving a good bond between sand particles and ensure a durable mold.
4. Bonding Properties The right bonding agents must be selected to enhance the sand's cohesiveness, which ensures the mold maintains its shape during pouring.
facing sand in foundry
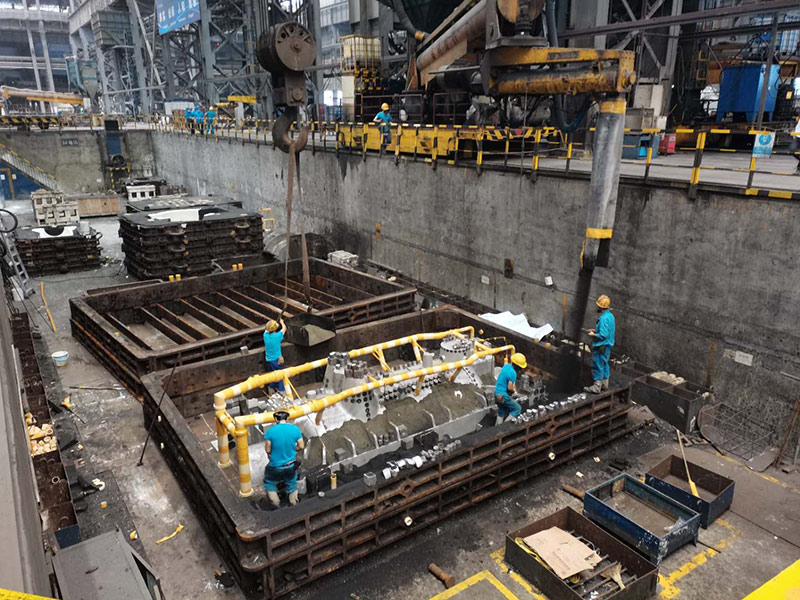
5. Thermal Conductivity This property affects how quickly heat is transferred from the metal to the sand. Optimal thermal conductivity helps prevent defects, such as burn-on, which can occur when molten metal reacts with the sand.
Impact on Casting Quality
The quality of facing sand directly correlates to the success of the casting process. When the right type of facing sand is chosen, it results in several benefits
- Improved Surface Finish A well-prepared facing sand will create a clean and smooth surface on the casting, reducing the need for extensive post-casting finishing processes.
- Decreased Defects Properly selected and mixed facing sand minimizes defects such as sand inclusion, misruns, and cold shuts, ultimately leading to less scrap and rework.
- Better Mold Stability The right sand composition contributes to the overall stability of the mold, reducing the risk of collapses during the metal pouring process.
- Enhanced Detail Reproduction For complex patterns, high-quality facing sand can reproduce intricate details without distortion, which is especially important for precision engineering applications.
Conclusion
Facing sand is undeniably a vital ingredient in the foundry casting process. Its properties and composition play an integral role in determining product quality and impacting overall efficiency within the foundry. As the industry continues to evolve with advancements in materials and technology, the importance of selecting the right facing sand will remain a key consideration for foundry specialists aiming to produce superior castings. Continuous research and development in this area promise to enhance casting methodologies and outcomes, ensuring that the foundry sector can meet the growing demands for high-quality components across various industries.
Post time:ડીસેમ્બર . 05, 2024 03:20
Next:Top Suppliers for Steel Sand Casting Services and Solutions