The Foundry Sand Casting Process An Overview
Foundry sand casting is one of the oldest and most widely used manufacturing processes in the metalworking industry
. This technique involves creating a mold from sand to form metal parts, a process that has remained relevant despite advancements in technology due to its efficiency, cost-effectiveness, and versatility.The sand casting process begins with the creation of a mold. This is achieved by packing sand around a pattern of the desired object. The pattern is typically made of metal, wood, or plastic and is a replica of the part to be cast. The sand used in the molding process is usually a mixture of fine particles of silica and clay, which bind together when moisture is added. This creates a mold that can hold its shape under the weight of molten metal.
Once the mold is formed, it is carefully removed from the pattern, revealing a cavity that precisely matches the shape of the desired part. This cavity is known as the mold cavity. The next step involves preparing the metal for casting, which includes melting the metal to a temperature sufficient for pouring. Common metals used in the sand casting process include aluminum, iron, bronze, and magnesium.
After the metal is melted, it is poured into the mold cavity through a gating system, which channels the molten metal into the space. The gating system is critical as it controls the flow of metal and influences the quality of the final cast. Once the metal fills the mold, it is left to cool and solidify. The cooling process can vary depending on the type of metal used and the thickness of the cast part.
foundry sand casting process
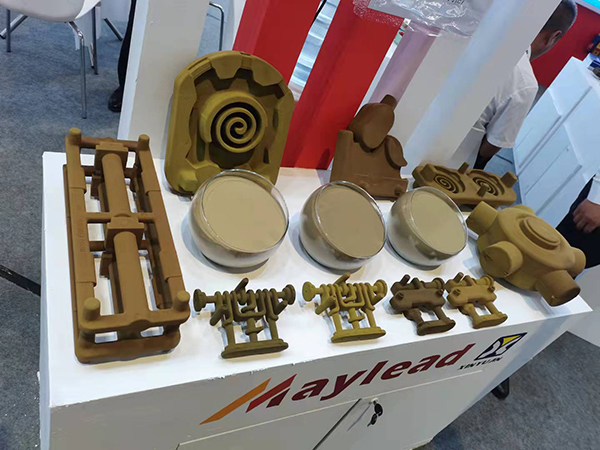
After the metal has fully cooled, the next phase is the removal of the mold. This is typically done by breaking away the sand, a process known as shakeout. The resulting metal part, now called a casting, may have some imperfections or surface roughness, which can be addressed through various finishing processes, such as grinding, sandblasting, or machining.
One of the significant advantages of sand casting is its ability to produce complex shapes and large parts. This method is particularly useful for industries that require intricate designs, such as automotive and aerospace manufacturing. Moreover, sand casting can accommodate a wide range of materials, making it a flexible option for many applications.
Cost-effectiveness is another hallmark of the sand casting process. The materials used, primarily sand, are comparatively inexpensive, and the mold can often be reused multiple times before it wears out. Additionally, the energy requirements for melting metal are manageable, further adding to the process's efficiency.
However, sand casting does have some limitations. The surface finish of cast parts is typically not as smooth as those produced by other methods, such as investment casting. Additionally, while this process is suitable for large production runs, it may not be the most economical choice for small quantities of high-precision components.
In conclusion, the foundry sand casting process remains a vital technique in manufacturing due to its adaptability, cost-effectiveness, and capability to produce complex shapes. As industries continue to evolve, sand casting will likely remain an essential part of the engineering landscape, adapting to meet modern needs and leveraging technological advancements to improve its effectiveness.
Post time:ઓગસ્ટ . 12, 2024 19:26
Next:Advancements and Techniques in Resin Bonded Sand Casting for Enhanced Metal Casting Efficiency