3D Printing Patterns for Sand Casting Revolutionizing Manufacturing Processes
The manufacturing landscape has seen revolutionary changes over the past few decades, and one of the most notable advancements is the integration of 3D printing technology into traditional casting processes. Among these processes, sand casting remains one of the most widely used methods for producing metal parts, especially in industries such as automotive, aerospace, and construction. The introduction of 3D printing patterns for sand casting is transforming the way manufacturers design and produce molds, offering unprecedented flexibility, precision, and efficiency.
Understanding Sand Casting
Sand casting is a process where a mold is created using sand, typically mixed with a bonding agent. The mold cavity is formed by compacting the sand around a pattern—a replica of the final part. Once the pattern is removed, molten metal is poured into the mold cavity, solidifying to create the desired part. This traditional technique has been favored due to its low cost, ability to create complex shapes, and versatility in material usage.
The Role of 3D Printing
The incorporation of 3D printing into sand casting is primarily focused on the production of patterns. Traditionally, these patterns require significant time and labor to create, often necessitating the use of skilled machinists. However, with advancements in 3D printing technology, manufacturers can now produce highly detailed and accurate patterns with minimal manual intervention.
3D printing allows for the rapid prototyping of molds, enabling designers to iterate their designs quickly. This not only reduces the time to market for new products but also allows for more experimentation with intricate designs that would have been challenging or impossible to achieve with traditional methods.
Advantages of 3D Printed Patterns
1. Speed and Efficiency One of the most significant advantages of using 3D printing for sand casting patterns is the speed of production. Traditional methods can take weeks or even months to fabricate a single pattern, while 3D printing can reduce this time to mere days.
3d printing patterns for sand casting
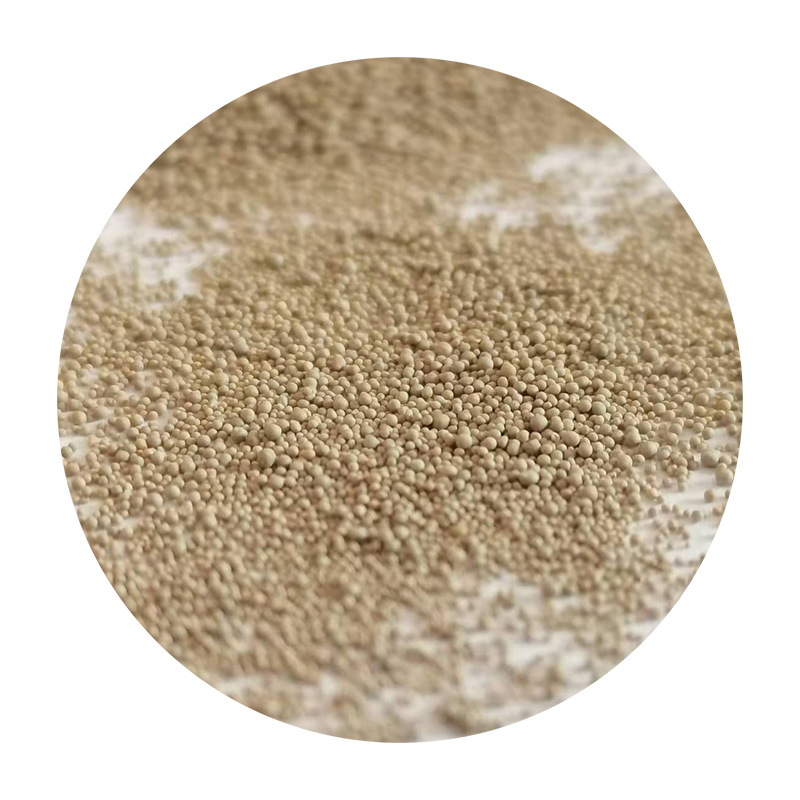
2. Cost-Effectiveness While there may be an initial investment in 3D printing equipment, the long-term savings are substantial. With reduced lead times and the capability to produce patterns on demand, manufacturers can minimize inventory costs and reduce storage requirements.
3. Design Freedom 3D printing eliminates many of the design constraints of traditional machining. This freedom allows for the creation of complex geometries, internal structures, and lightweight designs, which can lead to more innovative product developments.
4. Customization Customers increasingly demand tailored solutions. 3D printing enables manufacturers to easily create customized patterns to meet specific requirements without significant alterations to the production process.
5. Sustainability 3D printing technologies often produce less waste than traditional manufacturing methods. Additionally, the use of eco-friendly materials for 3D printing patterns can further enhance the sustainability of the sand casting process.
Challenges and Considerations
Despite its advantages, the adoption of 3D printing patterns for sand casting is not without challenges. The materials used for 3D printing must be compatible with the sand casting process, and the durability of these patterns during multiple casting cycles needs to be considered. Manufacturers must also navigate the initial learning curve associated with integrating new technologies into their existing workflows.
Furthermore, not all designs may be suitable for 3D printing; some parts may still require traditional machining processes to achieve the desired specifications. Thus, a hybrid approach that leverages both 3D printing and conventional methods may often yield the best results.
Conclusion
The integration of 3D printing patterns into sand casting processes signifies a major leap in manufacturing technology. By combining the strengths of both techniques, manufacturers can create more efficient, cost-effective, and innovative products. As 3D printing continues to evolve, it is poised to further disrupt traditional casting methods, setting new standards for design and production in the years to come. The future of manufacturing is undoubtedly intertwined with the advancements in 3D printing, making it an exciting time for the industry as a whole.
Post time:નવેમ્બર . 10, 2024 16:03
Next:Techniques for Smoothing 3D Prints Through Effective Sanding Methods