The Art and Process of Sanding Glazed Ceramics
Sanding glazed ceramics may seem like an unconventional practice, but it plays a crucial role in enhancing the aesthetics and functionality of ceramic pieces. This process is often required when dealing with imperfections or preparing items for additional finishes. Understanding the significance, techniques, and tips for sanding glazed ceramics can greatly benefit both hobbyists and professional ceramicists.
Understanding Glazed Ceramics
Glazed ceramics refer to pottery that has been coated with a vitreous enamel, a glass-like layer that provides a smooth finish, decorative color, and increased durability. While glaze serves as a protective barrier, it is not impervious to imperfections such as bumps, drips, or uneven surfaces that can arise during the firing process or as a result of handling.
Importance of Sanding
Sanding is an essential technique used to achieve a flawless finish on glazed ceramics. It allows artists to refine surfaces, eliminate unwanted textures, and prepare ceramics for further decoration or sealing. A well-sanded piece becomes more visually appealing and enhances the grip when handling functional ware like cups or plates, minimizing the risk of slips.
Preparing for Sanding
Before embarking on the sanding journey, gather necessary tools which typically include
- Different grits of sandpaper (from coarse to fine) - A sanding block or sponge - Water (if using wet sanding) - Safety goggles and a mask (to protect against dust)
Make sure to choose the right sandpaper grit depending on the severity of imperfections. Coarser grits (around 80-120) are suitable for initial sanding, while finer grits (220-600) should be employed for smoothing out the final surface.
sanding glazed ceramics
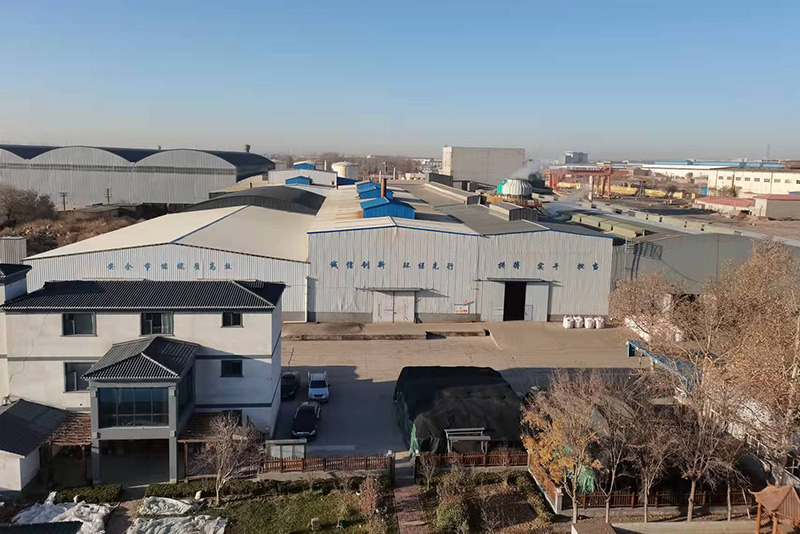
Techniques for Sanding Glazed Ceramics
1. Dry Sanding vs. Wet Sanding Dry sanding is straightforward but can produce a lot of dust, which is not ideal for delicate works. Wet sanding, on the other hand, involves using water to reduce dust and provide a smoother finish. It also helps to prevent the sandpaper from clogging.
2. Sanding in Circular Motions Start by gently sanding the affected area using light, circular motions. This technique promotes even sanding and helps avoid creating flat spots.
3. Applying Light Pressure It’s essential to apply minimal pressure while sanding glazed ceramics. Excessive force can easily damage the glaze or create uneven surfaces.
4. Check Progress Regularly Periodically wipe the surface to remove dust and check your progress. This practice allows for more control over your work and prevents over-sanding.
5. Finishing Touches Once the surface feels smooth, switch to a higher grit sandpaper to finalize the finish. The aim is to create a soft, seamless surface that showcases the glaze’s natural beauty.
Post-Sanding Care
After sanding, it is vital to clean the ceramic item thoroughly to remove any dust particles that may interfere with any subsequent glazing or finishing processes. A damp cloth or sponge can be used for this purpose. If the piece will undergo another glazing process, ensure it is completely dry before proceeding.
Conclusion
Sanding glazed ceramics is an art that requires patience and precision. From understanding the properties of glaze to applying the right techniques, each step is critical in refining ceramic pieces. By mastering the art of sanding, artists and ceramics enthusiasts can elevate their work, creating stunning, functional art that is both beautiful and long-lasting. Whether you are a professional potter or a DIY enthusiast, incorporating sanding into your ceramic processes can enhance not only the craftsmanship but also the joy involved in the creative journey.
Post time:Out . 08, 2024 21:40
Next:Exploring the Innovations of Super Sand Bond Technology for Enhanced Construction Solutions