Properties of Foundry Sand An Essential Component in Metal Casting
Foundry sand is a key material in the metal casting industry, primarily used to create molds for iron, steel, and non-ferrous alloys. Understanding the properties of foundry sand is crucial for ensuring high-quality castings and optimizing the manufacturing process. This article explores the fundamental characteristics of foundry sand, including its composition, physical properties, and its role in the foundry industry.
Composition of Foundry Sand
The main component of foundry sand is silica, typically in the form of quartz. Silica sand is preferred due to its high melting point, durability, and resistance to thermal shock. In addition to silica, foundry sand may contain other materials such as clay, silt, and various additives that enhance its performance. The specific composition can vary based on the type of metal being cast and the desired properties of the final product.
Physical Properties
1. Grain Size The size of the sand grains plays a significant role in determining the mold's surface finish and the overall quality of the cast. Foundry sands are usually classified into different grades based on mesh size, which affects their permeability and strength. Fine sands can produce a smoother surface finish but may be less durable, while coarser sands are more robust but may create rough surfaces.
2. Shape The shape of the sand grains can be angular, sub-angular, or spherical. Angular grains provide better interlocking and strength, making them suitable for molds that require high resistance to collapse. Spherical grains, while less common, can improve flowability and reduce the amount of binder needed.
3. Permeability This property is critical for allowing gases produced during the casting process to escape from the mold. High permeability prevents defects such as blowholes and ensures that the molten metal fills the mold effectively. The permeability of foundry sand can be influenced by its grain size, shape, and the amount of binder used.
properties of foundry sand
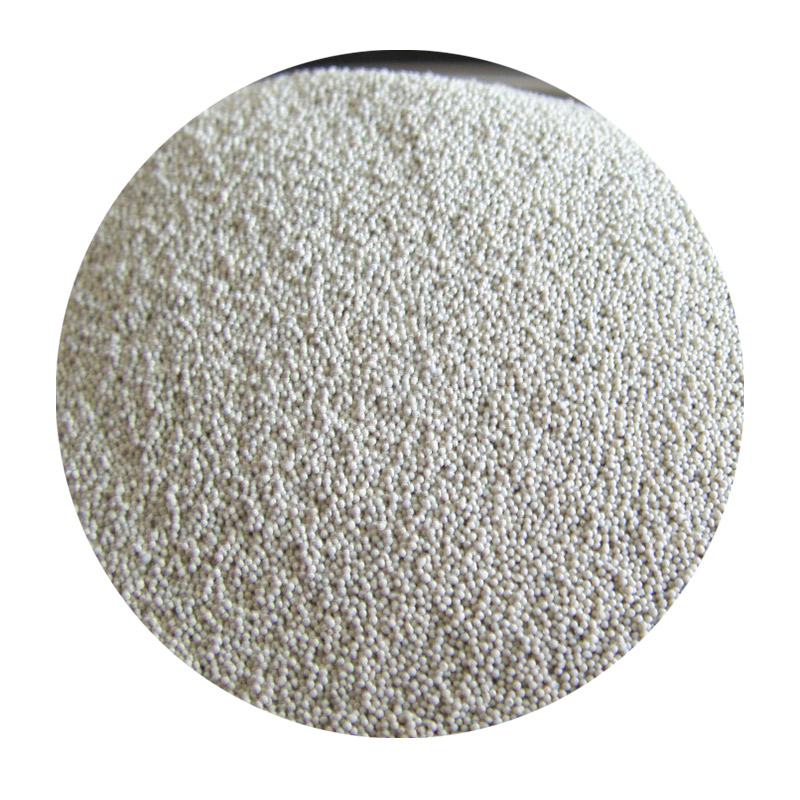
4. Strength The strength of foundry sand, particularly its compressive and tensile strength, is essential for maintaining the integrity of the mold during casting. Molds must withstand the weight of the molten metal and any mechanical forces during pouring. Various additives, such as clay and resin, can enhance the strength of the sand mixture, making it more suitable for demanding applications.
5. Thermal Stability Foundry sand must possess high thermal stability to withstand the extreme temperatures of molten metal without breaking down. Silica sand generally exhibits excellent thermal resistance, but the presence of impurities or the addition of binders can affect this property. Ensuring thermal stability is vital to prevent deformation of the mold and achieve precise casting dimensions.
Environmental Considerations
The use and disposal of foundry sand have raised environmental concerns in recent years. As foundry operations generate a significant amount of used sand, the industry has been exploring ways to recycle this material. Used foundry sand can often be treated and repurposed in construction applications, providing a sustainable solution that mitigates waste.
In addition to recycling efforts, there has been a push towards using more environmentally friendly binders in the sand mixture. This shift aims to reduce harmful emissions during the casting process while maintaining optimal performance qualities.
Conclusion
The properties of foundry sand play a vital role in the casting process, directly affecting the quality of the final product. From its composition to its physical characteristics, understanding these properties enables foundry professionals to make informed decisions that enhance the efficiency and effectiveness of metal casting. As the industry continues to evolve, focusing on sustainable practices and innovative materials will be crucial for the future of foundry sand and the metal casting sector as a whole. By prioritizing the study and application of these properties, foundries can achieve better operational performance, reduce environmental impact, and produce superior casting results.
Post time:Out . 16, 2024 16:11
Next:sanding 3d printed objects