The Art and Science of Large Sand Casting A Comprehensive Overview
Sand casting, one of the oldest and most versatile metal casting processes, remains a cornerstone in manufacturing large and complex components across various industries. As technology advances, the techniques and materials used in large sand casting have evolved, yet the fundamental principles of this casting method have stood the test of time. This article explores the process, advantages, considerations, and applications of large sand casting.
The Sand Casting Process
The sand casting process involves several key steps that transform raw materials into finished products. It begins with the creation of a mold, which is typically made from a mixture of sand, clay, and water. The sand is packed around a pattern—usually made from metal, plastic, or wood—that represents the shape of the final product. Once the mold is formed, the pattern is removed, leaving a cavity that will hold the molten metal during pouring.
Next, the molten metal, often aluminum, iron, or bronze, is poured into the cavity of the mold. After the metal cools and solidifies, the mold is broken apart to reveal the cast component. This process allows for the production of intricate shapes and large components that would be challenging or impossible to create with other methods.
Advantages of Sand Casting
One of the significant advantages of large sand casting is its ability to produce large and heavy parts without compromising detail and complexity. The sand mold can withstand high temperatures and is capable of adapting to various shapes, making it suitable for a wide range of applications.
Another benefit of sand casting is its cost-effectiveness. The materials used for the mold are relatively inexpensive, and the process itself requires minimal setup time compared to other casting methods, such as die casting or investment casting. This characteristic makes sand casting an ideal choice for low to medium production runs, where the cost of tooling can be a significant factor.
Moreover, sand casting is highly adaptable, allowing manufacturers to modify the design easily
. Whether it’s changing the mold or altering the composition of the metal, this flexibility means that large sand casting can accommodate specific industry needs and innovations effectively.large sand casting
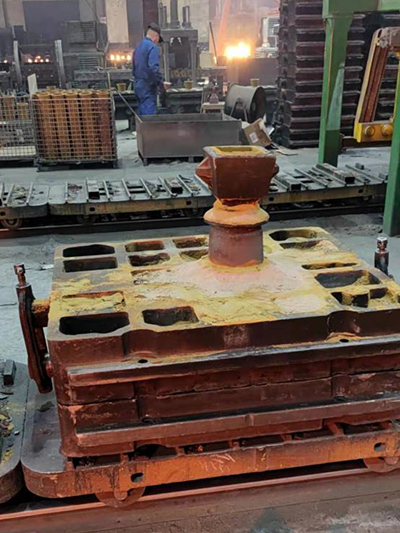
Challenges in Large Sand Casting
Despite its many benefits, large sand casting does present several challenges. One of the primary concerns is the dimensional accuracy of the final product. While the process can create complex shapes, achieving tight tolerances can be difficult, especially in larger casts. As a result, post-casting machining may be necessary to meet specific requirements.
Additionally, sand casting can lead to defects such as inclusions, air pockets, or surface roughness that may require additional processing. Hence, quality control throughout the casting process is crucial. Implementing measures like non-destructive testing can help identify and rectify potential issues early.
Another consideration is the environmental impact. The traditional sand casting process uses natural sand and binders, which may create waste and pollution. Therefore, many manufacturers are now exploring sustainable alternatives, using recycled materials or innovative molding techniques that minimize environmental footprints.
Applications of Large Sand Casting
Large sand casting is widely utilized in various industries, including automotive, aerospace, construction, and machinery. Components such as engine blocks, housing parts, and large structural elements are commonly produced using this method. The aerospace sector, for instance, benefits from sand casting's ability to create lightweight yet robust components, essential for flight efficiency and safety.
Additionally, in the energy sector, large sand castings are used in the production of turbine housings and pump casings, where durability and reliability are paramount. The ability to produce parts that can withstand extreme conditions makes sand casting an ideal method for these applications.
Conclusion
Large sand casting is a time-tested method that combines art and science, allowing manufacturers to create intricate and robust components for various applications. While it presents certain challenges, its advantages in flexibility, cost-effectiveness, and adaptability make it a preferred choice in several industries. As technology continues to advance, the future of large sand casting looks promising, with ongoing innovations likely to further enhance its efficiency and sustainability. Embracing these advancements will be essential as manufacturers strive to meet the growing demands of modern engineering and sustainable practices.
Post time:Dec . 14, 2024 01:53
Next:Innovative Techniques in 3D Sand Printing for Enhanced Manufacturing Applications