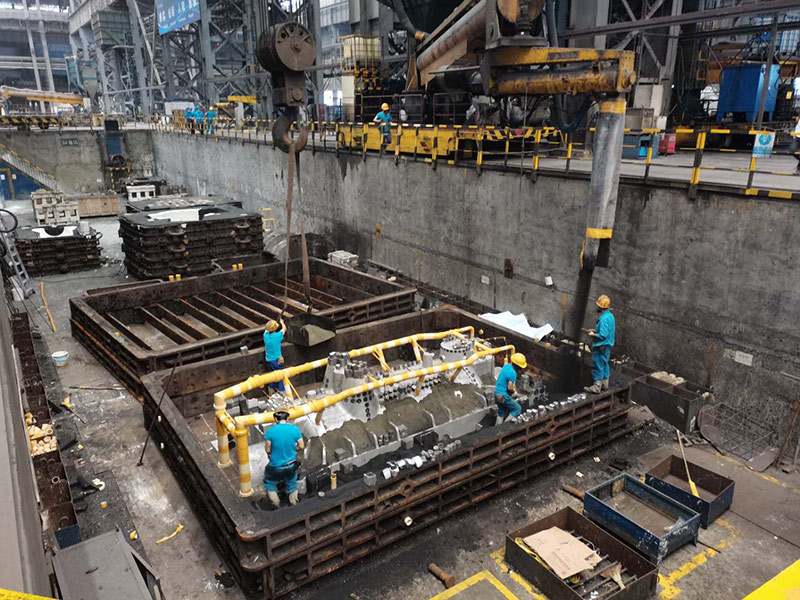
facing sand in foundry. When molten metal is poured into the mold cavity, there is a risk that it may seep into the pores of the facing sand and cause defects in the final cast part. Facing sand must be able to withstand this metal penetration and provide a barrier between the molten metal and the mold cavity. Furthermore, facing sand must have good permeability to allow gases to escape from the mold cavity during the casting process. If gases are trapped in the mold, they can cause defects in the final cast part, such as porosity or shrinkage. Permeable facing sand ensures that any gases generated during the casting process can escape through the mold walls. Overall, facing sand is a critical component in foundry operations. It helps to create high-quality molds that produce clean and defect-free cast parts. Foundries must carefully select and test facing sand to ensure that it meets the necessary characteristics for successful casting. By choosing the right facing sand, foundries can ensure that their final products meet the highest quality standards. Post time:Xul . 11, 2024 02:33
Next:High precision sand casting techniques for improved quality and accuracy in metal parts manufacturing.