Why Sand Casting is Used
Sand casting, also known as sand mold casting, is one of the most widely used metal casting processes. It utilizes sand as the primary molding material, creating molds that allow for the fabrication of intricate and complex metal components. This method has been employed for centuries and continues to be favored in various industries today. In this article, we will explore the various reasons why sand casting is so extensively utilized.
Versatility
One of the primary reasons sand casting is so popular is its versatility. It can accommodate a wide range of metal types, including aluminum, bronze, iron, and steel. This flexibility makes it suitable for numerous applications, from automotive and aerospace components to artistic sculptures and industrial machinery parts. Whether the desired shape is simple or complex, sand casting can adapt to the requirements of the project.
Cost-Effectiveness
Another reason for the widespread use of sand casting is its cost-effectiveness. The materials used in sand casting—primarily sand, clay, and water—are relatively inexpensive compared to other metal forming processes. Additionally, the equipment used in sand casting can be less costly to set up and maintain. For foundries, this means they can produce high-quality components without incurring excessive expenses, allowing them to offer competitive pricing to their customers.
Complex Geometries
Sand casting excels at producing complex geometries that may be challenging or impossible to achieve with other casting methods. The process permits the creation of detailed patterns that can include intricate designs and features. This capability is particularly advantageous in industries such as aerospace and automotive, where lightweight yet complex components are often necessary for performance. The ability to cast complex shapes reduces the need for additional machining processes, ultimately saving time and costs.
Scalability
why is sand casting used
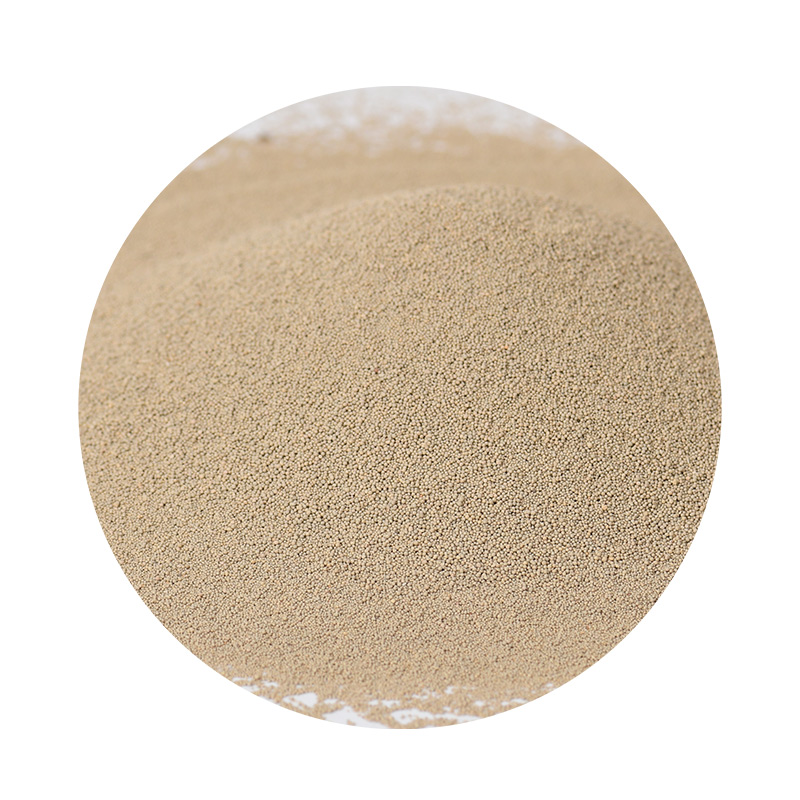
Sand casting is highly scalable, making it suitable for both small and large production runs. Whether a single prototype or thousands of units need to be produced, sand casting can accommodate the demands of the project. For instance, it allows for both small batch production of custom parts and mass production of standardized components. This scalability is a significant advantage for manufacturers looking to adapt to varying market needs.
Tolerances and Surface Finish
While sand casting might not always achieve the tight tolerances of other casting methods, advancements in technology have improved its accuracy. Modern sand casting techniques can produce components with a high degree of dimensional precision, reducing the need for secondary machining. Additionally, the surface finish of sand-cast parts can be improved through various finishing processes, such as shot blasting or machining. This ensures that the final product meets the required specifications and performance standards.
Ease of Pattern Making
Creating patterns for sand casting is relatively straightforward compared to other casting methods. Patterns can be made from various materials, including wood, aluminum, or plastic, and the process does not typically require the same level of precision or complexity needed for permanent molds. This ease of pattern making means that prototypes can be produced quickly, allowing manufacturers to bring their products to market faster.
Environmental Considerations
Finally, sand casting is often considered a more environmentally friendly option compared to other manufacturing processes. The materials used in sand casting can be recycled and reused multiple times, reducing waste. Moreover, advancements in green sand casting techniques increase sustainability by minimizing the environmental footprint of the casting process.
Conclusion
In conclusion, sand casting remains an essential method in metal fabrication due to its versatility, cost-effectiveness, and capability to produce complex geometries. The scalability of the process, combined with improvements in accuracy and environmental sustainability, makes it a preferred choice for manufacturers across various industries. As technology continues to evolve, sand casting is likely to maintain its significance in the world of casting and manufacturing for years to come.
Post time:Dàmh . 02, 2024 00:45
Next:Bauxite and Frac Sand Key Minerals for Energy and Industrial Applications