Materials Used for Sand Casting
Sand casting, also known as sand mold casting, is a versatile and widely used manufacturing process that involves creating a mold from sand to cast metal parts. The materials used in sand casting play a crucial role in determining the quality of the final product, influencing factors such as surface finish, dimensional accuracy, and overall durability. Below, we explore the primary materials involved in the sand casting process.
1. Sand
The most important material in sand casting is, of course, the sand itself. The sand used must have specific properties to create a successful mold. Commonly, silica sand is utilized due to its availability and high melting point, which makes it suitable for casting metals. The grain size of the sand is crucial; finer grains offer a smoother finish, while coarser grains allow for better flow of the molten metal. Additionally, the sand is often mixed with a bonding agent, typically clay, to enhance its cohesiveness and strength.
2. Bonding Agents
Bonding agents are critical in sand casting as they help to hold the sand particles together to maintain the integrity of the mold. The most common bonding agent used in sand casting is clay, particularly sodium bentonite. Other types of bonding agents such as resin-coated sands are also used, which provide greater strength and lower gas permeability. These alternatives often improve the mold's surface finish and dimensional accuracy.
3. Additives
Additives are used to enhance the properties of the mold sand and may include various agents such as water, which is added to activate the clay and improve mold strength. Other additives, like surfactants, can be used to improve the flow of the sand and minimize defects. In certain specialized applications, coatings can be added to enhance the surface properties of the molds, providing an additional layer of protection and improving release characteristics.
what materials are used for sand casting
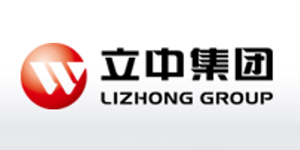
4. Metals
The metal castings produced in sand casting come from a variety of alloys, depending on the specific application and desired properties of the final product. Common metals used in sand casting include aluminum, iron, magnesium, and bronze. Each metal provides distinct benefits; for example, aluminum is lightweight and resistant to corrosion, making it ideal for automotive components, whereas cast iron is favored for its good wear resistance and machinability.
5. Coatings
To improve the mold's performance, coatings are often applied to the sand molds. These coatings can help enhance the surface finish of the casting, reduce the risk of sticking, and improve the thermal properties of the mold. Common coating materials include graphite, which also helps reduce oxidation during the metal pouring process.
6. Release Agents
Release agents are used to facilitate the easy removal of the casting from the mold. These agents create a barrier between the molten metal and the mold surface, preventing them from sticking together. Common release agents include oils and lubricants, which ensure that the cast product can be removed without damaging either the mold or the casting.
Conclusion
In conclusion, the materials used in sand casting are crucial for achieving high-quality metal castings. From the type of sand and bonding agents to the choice of metals and additives, each component plays a significant role in determining the efficiency of the casting process and the quality of the final product. Understanding these materials can help foundries optimize their processes and produce superior castings tailored to specific applications.
Post time:Sult . 22, 2024 19:15
Next:resin coated sand