Understanding the Importance of Sanding in Glazed Ceramics
Sanding glazed ceramics is a crucial procedure that significantly affects both the aesthetic and functional qualities of ceramic pieces. The process involves carefully abrading the surface of glazed ceramics to achieve desired finishes, improve adhesion for additional layers, or address imperfections. This article explores the reasons behind sanding glazed ceramics, the techniques involved, and the benefits it brings to ceramic art and production.
The Necessity of Sanding
Glazed ceramics often exhibit a glossy finish that is visually appealing but can sometimes lead to issues during the glazing process. For example, bubbles, drips, or uneven surfaces can detract from the overall quality of the piece. Sanding serves to remedy these imperfections by smoothing out rough spots, removing unwanted textures, and preparing the surface for further treatments if necessary.
Sanding is particularly important when working with multiple layers of glaze. In cases where a pottery artist aims to add a new glaze over an existing one, a smooth surface is essential for good adhesion. Without adequate sanding, the new layer may not bond properly, leading to flaking or peeling once the piece has been fired. Thus, sanding is not merely about aesthetics; it is integral to the durability and longevity of the ceramic work.
Techniques for Sanding Glazed Ceramics
The sanding process typically begins with selecting the appropriate tools and materials. Sandpaper comes in various grits, ranging from coarse to fine, allowing the artist to apply different levels of abrasion based on the job requirements. For instance, a coarser grit (around 80-120) is ideal for removing significant imperfections, while a finer grit (200-400) helps achieve a smooth, polished finish.
Before sanding, it's essential to clean the ceramic piece thoroughly to remove any dust or debris. Once the surface is clean, artists can start sanding in a circular motion or following the contours of the piece, ensuring even pressure is applied. It’s advisable to periodically check the surface for any missed spots or uneven areas.
sanding glazed ceramics
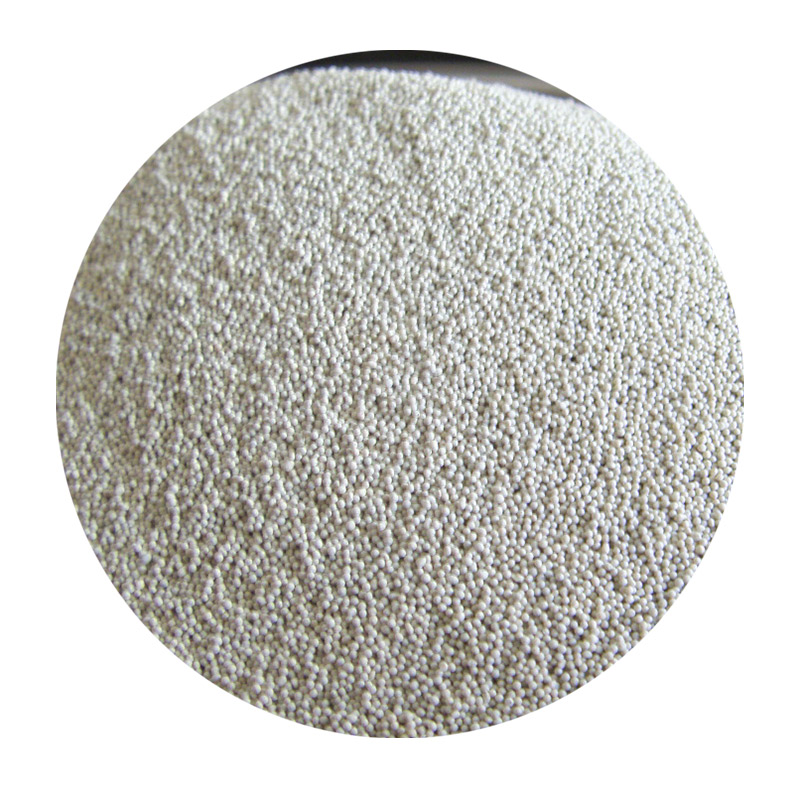
Water can be used to dampen the sandpaper during the process, which not only reduces dust but also helps prevent overheating of the ceramic surface. This is particularly important, as excessive heat can potentially damage the ceramic.
Benefits of Sanded Glazed Ceramics
The benefits of sanding glazed ceramics are manifold. First and foremost, the aesthetic enhancement it provides cannot be overstated. A well-sanded ceramic piece can shine with a reflective quality that attracts attention and admiration. Moreover, the final finish can be tailored to the artist's vision, whether that involves achieving a high-gloss sheen or a more matte appearance.
In addition to aesthetics, sanding plays a pivotal role in the functional aspects of ceramics. Sanded pieces are more likely to endure the rigors of everyday use. By ensuring proper glaze adhesion, artists can create functional items, such as dinnerware or decorative pieces, that stand the test of time.
Lastly, the sanding process provides artists with an opportunity for artistic expression. Many ceramicists view sanding as an extension of their creative process, allowing them to shape their work in ways that align with their individual styles and intentions.
Conclusion
Sanding glazed ceramics is an indispensable technique that enhances both the appearance and functionality of ceramic artworks. By meticulously preparing surfaces for glazing and ensuring adhesion, artists cultivate durable pieces that stand out for their beauty and craftsmanship. Whether for professional production or hobbyist projects, mastering the art of sanding can elevate any ceramic piece to new heights of excellence.
Post time:Dùbh . 23, 2024 07:10
Next:Combining Resin and Sand for Enhanced Durability and Aesthetics in Crafting